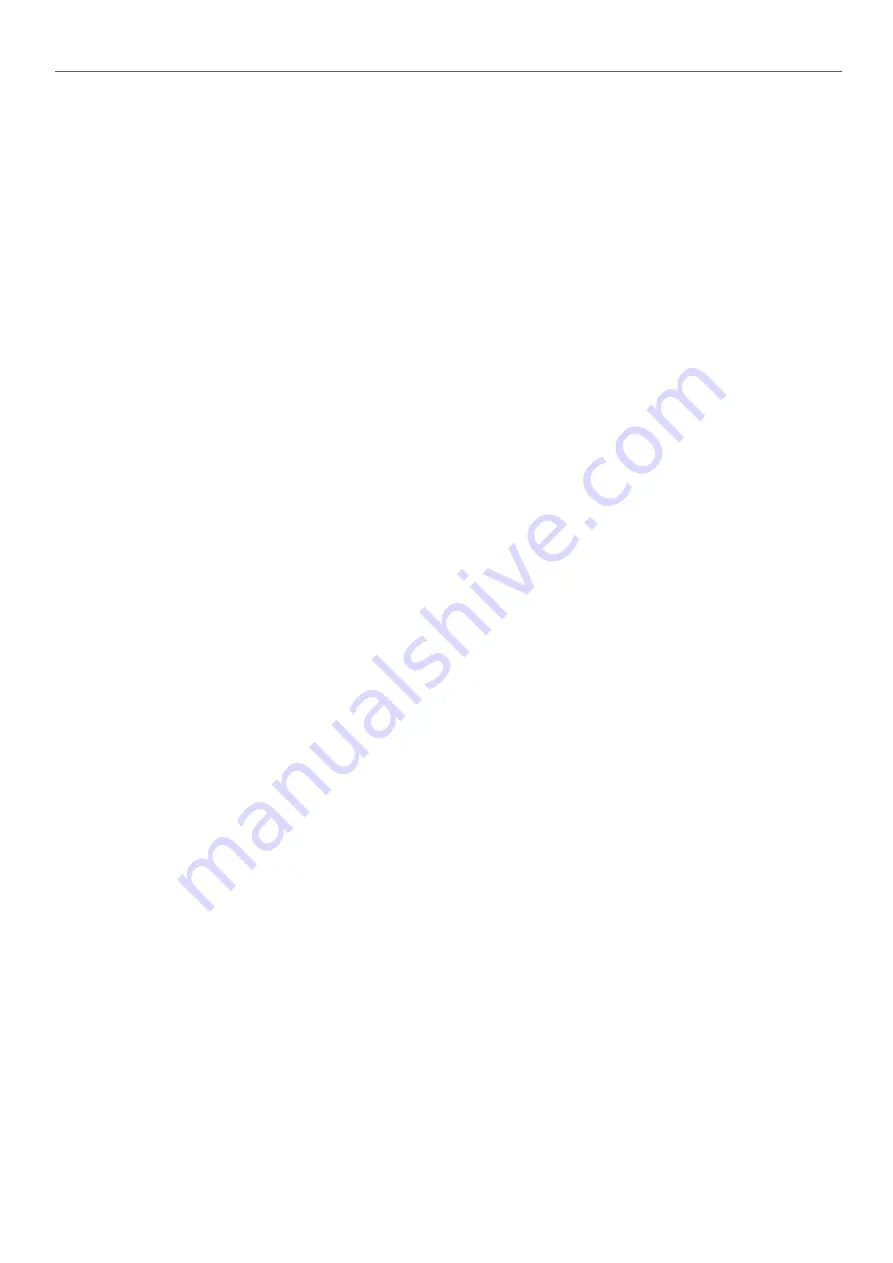
71
The water connection of the heat exchanger is a Victaulic
connection. As an option the evaporator is available with frost
protection (evaporator frost protection option).
The products that may be added for thermal insulation of the
containers during the water piping connection procedure must be
chemically neutral in relation to the materials and coatings to which
they are applied. This is also the case for the products originally
supplied by Carrier.
12.2.2 - Oil separator
In these units, the oil separator is a pressure vessel that is mounted
under the outside vertical condenser coils. Dis-charge gas at the
compressor outlet is directed towards the bottom of the oil separator
ring and most of the oil separates from the gas by strong
deceleration and by gravity. The gas then flows through a wire
mesh screen where the remaining oil is separated by coalescence
and flows to the bottom of the ring. The gas is now free from oil
and leaves the ring at the top towards the condenser.
The oil separator is equipped with a trace heater regulated by the
control.
12.2.3 - Economiser function
The economiser function includes a liquid line valve, a filter drier,
two EXVs, a plate heat exchanger as well as protection devices
(fuse or valve).
At the condenser outlet a part of the liquid is expanded via the
secondary EXV in one of the heat exchanger circuits and then
returns as gas at the compressor economiser. This expansion
permits increase of the liquid sub-cooling of the rest of the flow that
penetrates the evaporator via the prin-cipal EXV. This permits
increasing the cooling capacity of the system as well as its
efficiency.
12.3 - High pressure safety loop (SRMCR)
12.3.1 - General description
The device is equipped with a high pressure safety loop, also known
as safety related measurement control and regulation system
(SRMCR), consisting of
2 PZHH type high pressure switches (HPS) with manual reset
located at the outlet of each compressor
A control relay on the compressor board.
2 compressor main contactors
See the wiring diagram and bill of material of the unit for details of
identification and references.
This safety loop is designed according to EN 61508 for :
SIL level (Safety Integrity): 2.
Demand mode: high and low.
Mission Time : 20 years.
Periodic test: The safety loop operation must be tested at least once
a year to maintain its integrity.
12.3.2 - Function description and reset
Diagram below describes the description of operation: refer to the
machine documentation to obtain the detailed wiring diagram”
“The HPS switches are wired in series to the control relays of the
A_C board which controls the KM and KM-D main contactors. Both
switches are closed during continuous operation of the compressor.
When one of the HPS switches opens, the control relay interrupts
the supply voltage of the KM-and KM-D contactor coil: the main
contactor opens, which causes the compressor to lose power and
stop.
The operation of this safety loop is electromechanical: it is not based
on software or an electronic component.
12.3.3 - Restart after high pressure detection
After detecting the overpressure, it is necessary to manually reset
the switched HPS (s). Using a dull tool with a diameter of less than
6 mm if the PZHH HPS is deactivated.
12.3.4 - Checks in case of apparent failure of the
safety accessory
If the operating pressure of the unit appears to have been exceeded
(for example: after opening of the relief valves), the unit must be
stopped immediately. The unit and the safety loop must pass all
periodic checks before any possible restart.
If the test reveals any malfunctions that could have led to exceed
the maximum allowable pressure (PS) of the device, a complete
check of all pressure equipment must be performed to verify their
mechanical integrity.
12.3.5 - High pressure safety loop periodic test
In order to verify the full integrity of the safety loop, the following
checks have to be performed periodically:
Contactors check
Complete loop operation check
12.3.5.1 -
Power contactor check procedure
This procedure shall be applied for each compressor of the unit.
1. Switch off the power of the electrical equipment.
Apply all safety procedures for access to equipment with
hazardous voltage.
2. Measure the resistance between upstream and downstream
terminals of the main power contactors KM- and KM-D for each
phase.
Note: calibrated Ohmmeter shall be used for this task.
3. Confirm resistance is more than 1.0 MOhm.
A resistance lower than 1.0 MOhm, indicates that contactor KM_
or KM_D is defective: further investigations and replacement of the
failed part is required.
12.3.5.2 - Complete safety loop test
The purpose of this periodic test is to verify the proper functioning
and setting of the high-pressure safety loop of a refrigerant circuit.
In order to reach the triggering pressure of the loop, the pressure
and temperature thresholds activating the discharge of the
compressor by the regulation system are raised.
This procedure must be repeated for each circuit of the unit.
1. Set up a calibrated pressure gauge on the high pressure part
of the circuit (compressor discharge)
2. Reset all activated alarms
3. Activate the HP test mode for the corresponding circuit via the
control interface.
Enable Quick Test Mode (Quick Test Menu> [ QCK_TEST ]
parameter active )
Activate the high pressure test for the desired circuit (Menu
Quick Test> parameter [HP_TEST] to 0 for circuit A or 1 for
the B circuit. The corresponding circuit starts to perform the
HP test.
4. Getting Started Machine
12 - MAJOR SYSTEM COMPONENTS AND OPERATION DATA