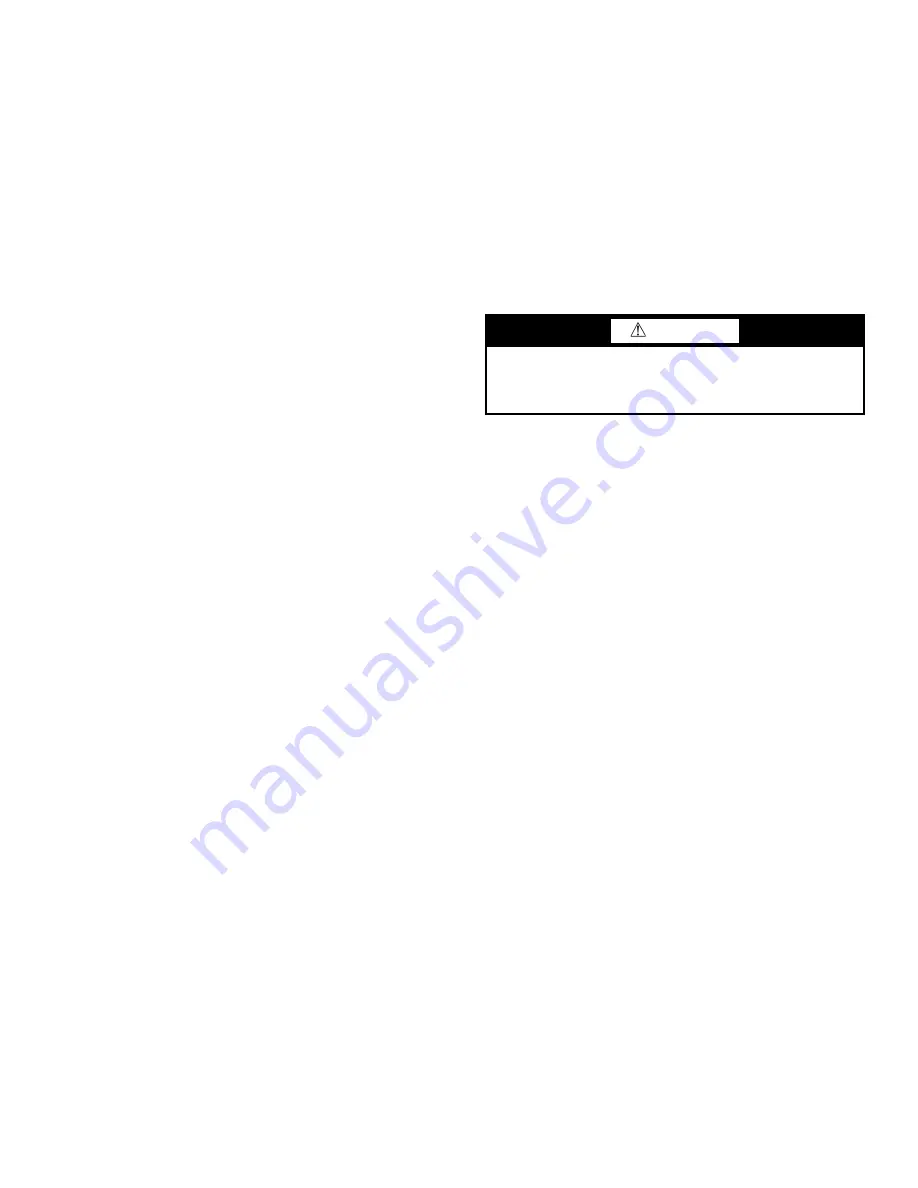
41
TROUBLESHOOTING GUIDE
Overview
The PIC6 control system has many features to help the operator
and technician troubleshoot a 19MV chiller.
• The HMI shows the chiller’s actual operating conditions
and can be viewed while the unit is running.
• The HMI default screen indicates when an alarm occurs.
Once all alarms have been cleared (by correcting the prob-
lems), the HMI default screen indicates normal operation.
For information about displaying and resetting alarms and
a list of alert codes, see the 19MV with PIC6 Controls Op-
eration and Troubleshooting manual.
• The Configuration menu screens display information that
helps to diagnose problems with chilled water temperature
control, chilled water temperature control overrides, surge al-
gorithm status, and time schedule operation.
• The quick test and quick calibration feature facilitates the
transducers, the guide vane actuator, EXVs, water pumps,
tower control, and other on/off outputs while the compres-
sor is stopped. It also has the ability to lock off the com-
pressor and turn on water pumps for pumpout operation
(Maintenance Menu). The HMI shows the temperatures
and pressures required during these operations.
• If an operating fault is detected, an alarm indicator is dis-
played on the HMI default screen. A more detailed mes-
sage — along with a diagnostic message — is also stored
in the Current Alarms table.
• Review the Alarms History table to view other less critical
events which may have occurred. Compare timing of rele-
vant events and alarms.
For detailed information about alarms, see the 19MV with Con-
trols Operation and Troubleshooting manual. Press the bell icon
in the top right corner of the home screen to access current alarms
and alarm history, and to reset alarms.
Checking Display Messages
The first area to check when troubleshooting the 19MV is the
HMI display. Status messages are displayed at the bottom of the
screen, and the alarm icon indicates a fault. For a complete list of
alarms, see the 19MV with Controls Operation and Trouble-
shooting manual.
Checking Temperature Sensors
All temperature sensors are thermistor-type sensors. This means
that the resistance of the sensor varies with temperature. All sen-
sors have the same resistance characteristics. If the controls are
on, determine sensor temperature by measuring voltage drop; if
the controls are powered off, determine sensor temperature by
measuring resistance. Compare the readings to the values listed
RESISTANCE CHECK
Turn off the control power and, from the module, disconnect the
terminal plug of the sensor in question. With a digital ohmmeter,
measure sensor resistance between receptacles as designated by
the wiring diagram. The resistance and corresponding temperature
are listed in Tables 20 and 21. Check the resistance of both wires
to ground. This resistance should be infinite.
VOLTAGE DROP
The voltage drop across any energized sensor can be measured
with a digital voltmeter while the control is energized. Tables 20
and 21 list the relationship between temperature and sensor volt-
age drop (volts dc measured across the energized sensor). Exer-
cise care when measuring voltage to prevent damage to the sen-
sor leads, connector plugs, and modules. Sensors should also be
checked at the sensor plugs.
CHECK SENSOR ACCURACY
Place the sensor in a medium of known temperature and compare
that temperature to the measured reading. The thermometer used
to determine the temperature of the medium should be of laborato-
ry quality with 0.5
F (0.25
C) graduations. The sensor in question
should be accurate to within 2
F (1.2
C).
Note that the PIC6 control module, MAINTENANCE menu, of-
fers a temperature sensor calibration feature where the sensor tem-
perature can be offset. Note that only the four water temperatures
can be calibrated. To use this feature, place the sensor at 32°F
(0
C) or other known temperature. Read the raw temperature and
calculate offset based on the reading seen in the TEMP_CAL
menu. Enter and execute the offset, which cannot exceed ± 2
F
(1.2
C).
See Fig. 2 for sensor locations. The sensors are immersed direct-
ly in the refrigerant or water circuits. When installing a new sen-
sor, apply a pipe sealant or thread sealant to the sensor threads.
An additional thermistor, factory installed in the bottom of the
evaporator barrel, is displayed as Evap Refrig Liquid Temp on the
TEMPERATURES display screen. This thermistor provides addi-
tional protection against a loss of water flow.
MOTOR TEMPERATURE SENSORS
See Fig. 40 for the location and wiring of the two motor tempera-
ture sensors.
CAUTION
Relieve all refrigerant pressure or drain the water before
removing any thermowell threaded into the refrigerant
pressure boundary. Failure to do so could result in personal
injury and equipment damage.
Summary of Contents for AquaEdge 19MV
Page 49: ...49 Fig 46 SIOB...
Page 50: ...50 Fig 47 IOB2...
Page 51: ...51 Fig 48 19MV Auxiliary Controls Wiring...