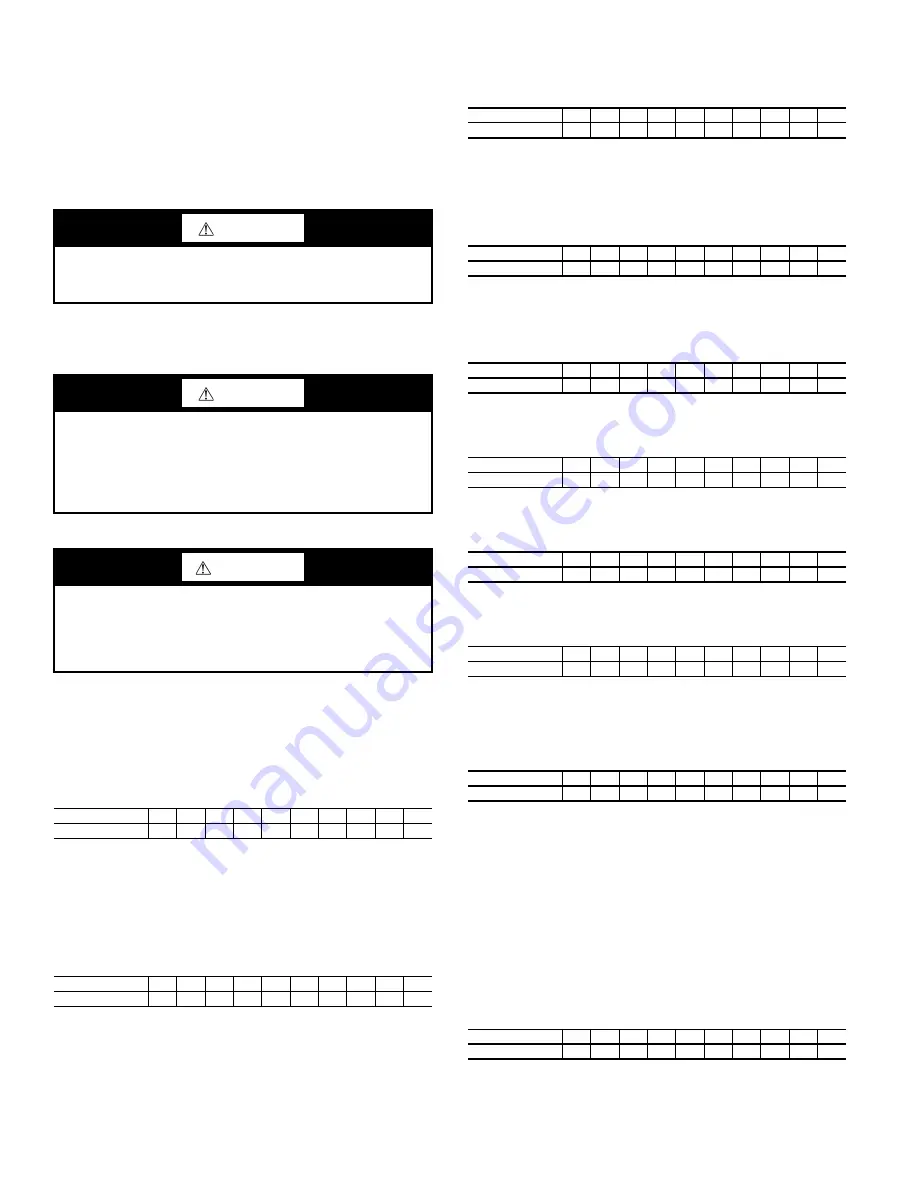
34
1. The display on the chiller control panel is suitable for
determining refrigerant-side pressures and low (soft) vac-
uum. To assure the desired range and accuracy when mea-
suring evacuation and dehydration, use a quality vacuum
indicator or manometer. This can be placed on the
Schrader connections on each vessel by removing the
pressure transducer.
2. To determine pumpout storage tank pressure, a 30 in. Hg
vacuum –0-400 psi (101-0-2758 kPa) gage is attached to
the storage tank.
POSITIVE PRESSURE CHILLERS WITH STORAGE TANKS
In the Valve/Condition tables that accompany these instruc-
tions, the letter “C” indicates a closed valve.
Transfer Refrigerant from Pumpout Storage Tank to Chiller
1. Equalize refrigerant pressure.
a. Turn on chiller water pumps and monitor chiller pressures.
b. Close pumpout and storage tank valves 2, 4, 5, and
10, and close refrigerant charging valve 7; open
chiller isolation valve 11 and any other chiller isola-
tion valves, if present.
c. Open pumpout and storage tank valves 3 and 6; open
chiller valves 1a and 1b.
d. Gradually crack open valve 5 to increase chiller pres-
sure to 35 psig (241 kPa). Slowly feed refrigerant to
prevent freeze-up.
e. Open valve 5 fully after the chiller pressure rises
above the freezing point of the refrigerant. Let the
storage tank and chiller pressure equalize. Open
refrigerant charging valve 7 and storage tank charging
valve 10 to let liquid refrigerant drain into the chiller.
2. Transfer remaining refrigerant.
a. Close valve 5 and open valve 4. Turn off pumpout con-
denser water, and turn on pumpout compressor in man-
ual mode to push liquid refrigerant out of storage tank.
Monitor the storage tank level until tank is empty.
b. Close refrigerant charging valves 7 and 10.
c. Turn off the pumpout compressor.
d. Turn off the chiller water pumps.
e. Close valves 3 and 4.
f. Open valves 2 and 5.
g. Turn on pumpout condenser water.
h. Run the pumpout compressor in manual mode until
the storage tank pressure reaches 5 psig (34 kPa),
18 in. Hg vacuum (41 kPa absolute).
i. Turn off the pumpout compressor.
j. Close valves 1a, 1b, 2, 5, and 6.
k. Turn off pumpout condenser water.
Transfer the Refrigerant from Chiller to Pumpout Storage Tank
1. Equalize refrigerant pressure.
a. Valve positions:
b. Slowly open valve 5 and refrigerant charging valves 7
and 10 to allow liquid refrigerant to drain by gravity
into the storage tank.
2. Transfer the remaining liquid.
a. Turn off pumpout condenser water. Place valves in the
following positions:
b. Run the pumpout compressor in automatic mode until
vacuum switch is satisfied and compressor stops.
Close valves 7 and 10.
c. Turn off the pumpout compressor.
3. Remove any remaining refrigerant.
a. Turn on chiller water pumps.
b. Turn on pumpout condenser water.
c. Place valves in the following positions:
d. Run the pumpout compressor until the chiller pressure
reaches 35 psig (241 kPa); then shut off the pumpout
compressor. Warm chiller condenser water will boil
off any entrapped liquid refrigerant and chiller pres-
sure will rise.
e. When chiller pressure rises to 40 psig (276 kPa), turn
on the pumpout compressor until the pressure again
reaches 35 psig (241 kPa); then turn off the pumpout
compressor. Repeat this process until the chiller pres-
sure no longer rises; then turn on the pumpout com-
pressor and pump out until the chiller pressure
reaches 18 in. Hg vacuum (41 kPa absolute). This can
be done in On or Automatic mode.
f. Close valves 1a, 1b, 3, 4, and 6.
g. Turn off the pumpout condenser water.
4. Establish vacuum for service. To conserve refrigerant,
operate the pumpout compressor as described in Step 3e
CAUTION
Transfer, addition, or removal of refrigerant in spring-isolated
chillers may place severe stress on and damage external piping
if springs have not been blocked in both up and down directions.
CAUTION
Always run chiller cooler and condenser water pumps and
always charge or transfer refrigerant as a gas when chiller
vessel pressure is less than 35 psig (241 kPa). Below these
pressures, liquid refrigerant flashes into gas, resulting in ex-
tremely low temperatures in the cooler/condenser tubes and
possibly causing tube freeze-up.
WARNING
During transfer of refrigerant into and out of the 19XR stor-
age tank, carefully monitor the storage tank level gage. Do
not fill the tank more than 90% of capacity to allow for re-
frigerant expansion. Overfilling may result in damage to
the tank and personal injury.
VALVE
1A
1B
2
3
4
5
6
7
10
11
CONDITION
C
C
C
C
C
VALVE
1A
1B
2
3
4
5
6
7
10
11
CONDITION
C
C
VALVE
1A
1B
2
3
4
5
6
7
10
11
CONDITION
C
C
C
C
VALVE
1A
1B
2
3
4
5
6
7
10
11
CONDITION
C
C
C
C
C
C
C
C
C
VALVE
1A
1B
2
3
4
5
6
7
10
11
CONDITION
C
C
C
C
C
VALVE
1A
1B
2
3
4
5
6
7
10
11
CONDITION
C
C
VALVE
1A
1B
2
3
4
5
6
7
10
11
CONDITION
C
C
VALVE
1A
1B
2
3
4
5
6
7
10
11
CONDITION
C
C
C
C
VALVE
1A
1B
2
3
4
5
6
7
10
11
CONDITION
C
C
C
C
VALVE
1A
1B
2
3
4
5
6
7
10
11
CONDITION
C
C
C
C
C
C
C
C
C
Summary of Contents for AquaEdge 19MV
Page 49: ...49 Fig 46 SIOB...
Page 50: ...50 Fig 47 IOB2...
Page 51: ...51 Fig 48 19MV Auxiliary Controls Wiring...