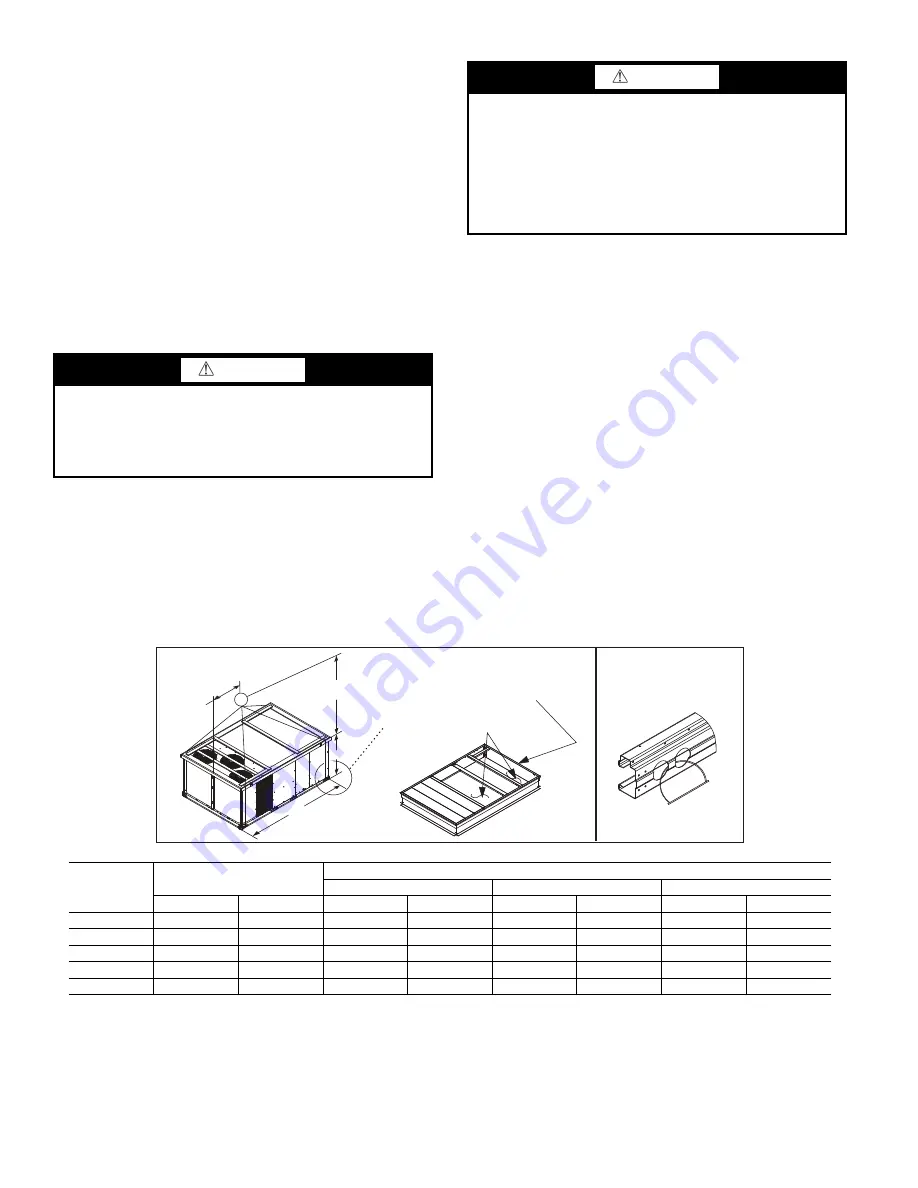
22
Step 5 — Field Fabricate Ductwork
Cabinet return-air static pressure (a negative condition) shall not
exceed 0.5 in. wg (87 Pa) with economizer or without economizer.
For vertical ducted applications, secure all ducts to roof curb and
building structure. Do not connect ductwork to unit.
Fabricate supply ductwork so that the cross sectional dimensions
are equal to or greater than the unit supply duct opening dimen-
sions for the first 18-in. (458 mm) of duct length from the unit
basepan.
Insulate and weatherproof all external ductwork, joints, and roof
openings with counter flashing and mastic in accordance with ap-
plicable codes.
Ducts passing through unconditioned spaces must be insulated
and covered with a vapor barrier.
If a plenum return is used on a vertical unit, the return should be
ducted through the roof deck to comply with applicable fire codes.
A minimum clearance is not required around ductwork.
Step 6 — Rig and Place Unit
Keep unit upright and do not drop. Spreader bars are not required
if top crating is left on the unit. Rollers may be used to move unit
across a roof. Level by using unit frame as a reference. See Table 2
and Fig. 19 for additional information.
Lifting holes are provided in base rails as shown in Fig. 19. Refer
to rigging instructions on the unit.
Before setting the unit onto the curb, recheck gasketing on curb.
POSITIONING ON CURB
Position unit on roof curb so that the following clearances are
maintained:
1
/
4
-in. (6 mm) clearance between the roof curb and the
base rail inside the right and left,
1
/
2
-in. (12 mm) clearance be-
tween the roof curb and the base rail inside the front and back.
This will result in the distance between the roof curb and the base
rail inside on the condenser end of the unit being approximately
equal to Details A and B in Fig. 16-18.
Do not attempt to slide unit on curb after unit is set. Doing so will
result in damage to the roof curb seal.
Although unit is weatherproof, guard against water from higher
level runoff and overhangs.
Flue vent discharge must have a minimum horizontal clearance of
48-in. (1220 mm) from electric and gas meters, gas regulators, and
gas relief equipment. Minimum distance between unit and other
electrically live parts is 48-in. (1220 mm).
Flue gas can deteriorate building materials. Orient unit such that
flue gas will not affect building materials. Locate mechanical draft
system flue assembly at least 48-in. (1220 mm) from an adjacent
building or combustible material.
After unit is in position, remove rigging skids and shipping
materials.
Fig. 19 — Rigging Details
CAUTION
PROPERTY DAMAGE HAZARD
Failure to follow this caution may result in damage to roofing
materials.
Membrane roofs can be cut by sharp sheet metal edges. Be
careful when placing any sheet metal parts on such roof.
CAUTION
UNIT DAMAGE HAZARD
Failure to follow this caution may result in equipment damage.
All panels must be in place when rigging. Unit is not designed
for handling by fork truck when packaging is removed.
If using top crate as spreader bar, once unit is set, carefully
lower wooden crate off building roof top to ground. Ensure
that no people or obstructions are below prior to lowering the
crate.
NOTES:
1. Dimensions in ( ) are in inches.
2. Hook rigging shackles through holes in base rail, as shown in detail “A.” Holes in base rails are centered around the unit center of gravity.
3. Use wooden top skid, when rigging, to prevent rigging straps from damaging the unit.
UNIT
MAX WEIGHT
DIMENSIONS
A
B
C
LB
KG
in.
mm
in.
mm
in.
mm
48TC**17
2355
1068
127.8
3249
58.7
1491
52.3
1328
48TC**20
2370
1075
127.8
3249
58.7
1491
52.3
1328
48TC**24
2516
1141
141.5
3595
71.5
1816
52.3
1328
48TC**28
2652
1203
141.5
3595
71.5
1816
60.3
1532
48TC**30
2976
1353
157.8
4007
80.3
2040
60.3
1532
B
C
A
(914-1371)
36"-54"
DETAIL A
SEE DETAIL A
PLACE ALL
S
EAL
S
TRIP
S
IN PLACE BEFORE PLACING
UNIT ON ROOF CURB.
DUCT END
Summary of Contents for 48TC D/E17 Series
Page 5: ...5 Fig 2 48TC 17 20 Vertical Airflow...
Page 6: ...6 Fig 3 48TC 17 20 Back View and Condensate Drain Location...
Page 7: ...7 Fig 4 48TC 17 20 Corner Weights and Clearances...
Page 8: ...8 Fig 5 48TC 17 20 Bottom View...
Page 9: ...9 Fig 6 48TC 24 28 Vertical Airflow...
Page 10: ...10 Fig 7 48TC 24 28 Back View and Condensate Drain Location...
Page 11: ...11 Fig 8 48TC 24 28 Corner Weights and Clearances...
Page 12: ...12 Fig 9 48TC 24 28 Bottom View...
Page 13: ...13 Fig 10 48TC 30 Vertical Airflow...
Page 14: ...14 Fig 11 48TC 30 Back View and Condensate Drain Location...
Page 15: ...15 Fig 12 48TC 30 Corner Weights and Clearances...
Page 16: ...16 Fig 13 48TC 30 Bottom View...
Page 19: ...19 Fig 16 Roof Curb Details 17 and 20 Size Units...
Page 20: ...20 Fig 17 Roof Curb Details 24 and 28 Size Units...
Page 21: ...21 Fig 18 Roof Curb Details 30 Size Units...
Page 47: ...47 Fig 52 PremierLink Wiring Diagram...
Page 48: ...48 Fig 53 PremierLink Wiring Diagram with Humidi MiZer System...
Page 49: ...49 Fig 54 Typical RTU Open System Control Wiring Diagram...
Page 50: ...50 Fig 55 Typical RTU Open System Control Wiring Diagram with Humidi MiZer System...
Page 51: ...51 Fig 56 48TC 17 30 Control Wiring Diagram...
Page 52: ...52 Fig 57 48TC 17 30 Power Wiring Diagram 208 230 3 60...
Page 53: ...53 Fig 58 48TC 17 30 Power Wiring Diagram 460 3 60...
Page 54: ...54 Fig 59 48TC 17 30 Power Wiring Diagram 575 3 60...
Page 55: ...55 Fig 60 48TC 17 30 Control Wiring Diagram with Humidi MiZer System...
Page 56: ...56 Fig 61 48TC 17 30 Power Wiring Diagram with Humidi MiZer System 208 230 3 60...
Page 57: ...57 Fig 62 48TC 17 30 Power Wiring Diagram with Humidi MiZer System 460 3 60...
Page 58: ...58 Fig 63 48TC 17 30 Power Wiring Diagram with Humidi MiZer System 575 3 60...