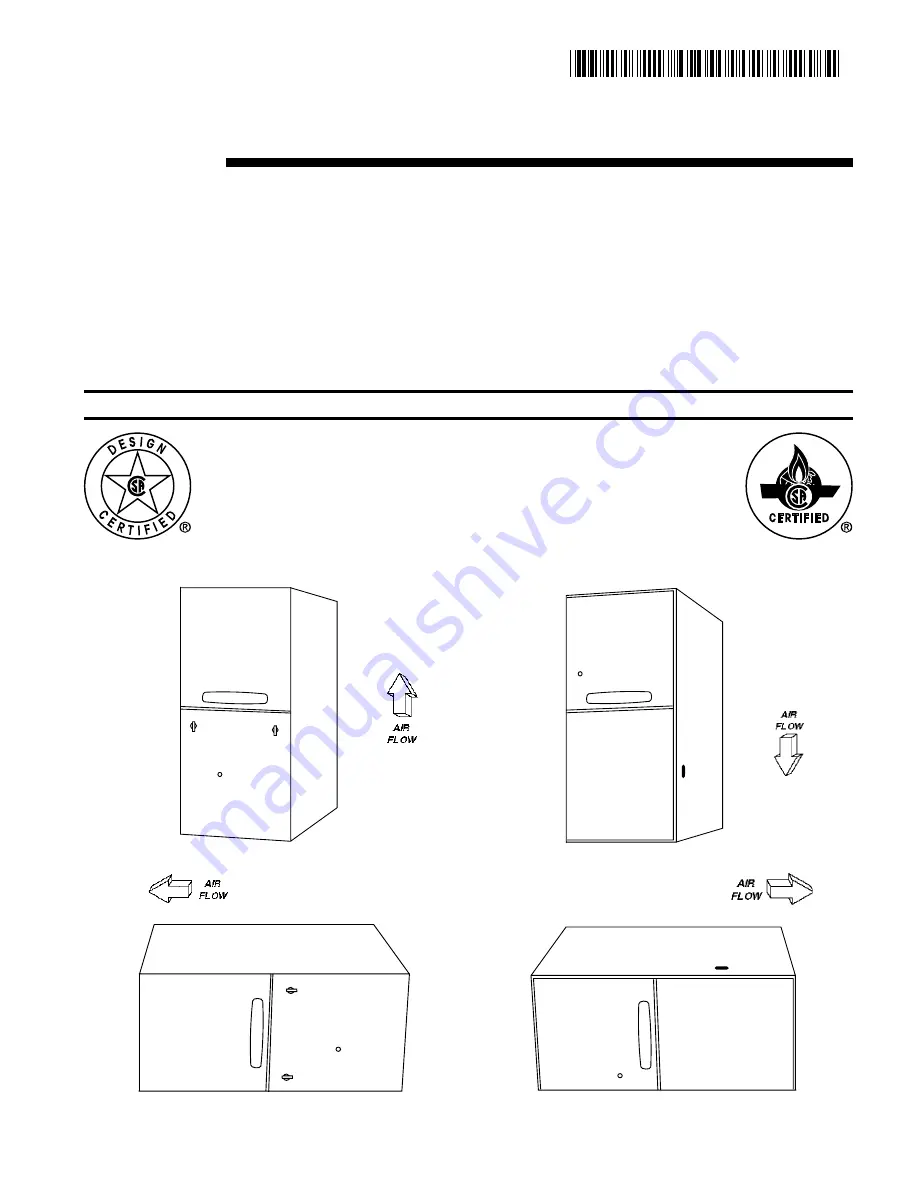
*UX1B040A9H21B
*UX1B060A9H31B
*UX1B080A9H31B
*UX1C100A9H41B
*UX1D120A9H51B
High Efficiency Single Stage Upflow / Horizontal
and Downflow / Horizontal Gas-Fired, Direct Vent
Condensing Furnaces
ALL phases of this installation must comply with NATIONAL, STATE AND LOCAL CODES
IMPORTANT — This Document is customer property and is to remain with this unit.
Please return to service information pack upon completion of work.
Installer’s Guide
*DX1B040A9H21B
*DX1B060A9H31B
*DX1B080A9H31B
*DX1C100A9H31B
*DX1D120A9H51B
*__First letter may be “A” or “T”
UPFLOW
*UX1-H
UPFLOW/HORIZONTAL
*DX1-H
DOWNFLOW
DOWNFLOW/HORIZONTAL
A341624P08
1 8 - CD2 2 D1 - 5