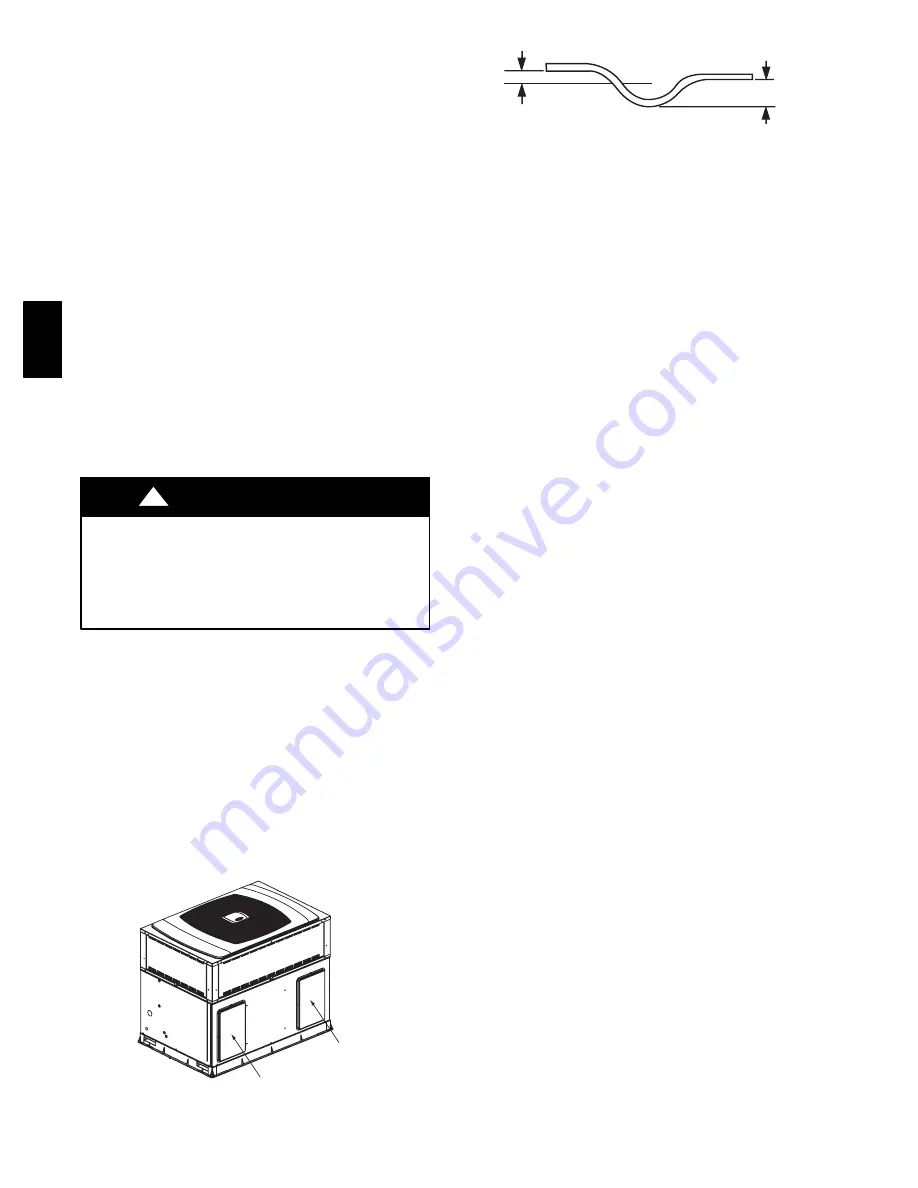
10
Step 6—Provide for Condensate Disposal
NOTE
: Ensure that condensate--water disposal methods comply
with local codes, restrictions, and practices.
The units dispose of condensate through a 3/4 --in. NPT female
fitting that exits on the compressor end of the unit. Condensate water
can be drained directly onto the roof in rooftop installations (where
permitted) or onto a gravel apron in ground level installations.
Install a field--supplied condensate trap at end of condensate
connection to ensure proper drainage. Make sure that the outlet of
the trap is at least 1 in. lower than the drain--pan condensate
connection to prevent the pan from overflowing. Prime the trap with
water. When using a gravel apron, make sure it slopes away from the
unit.
If the installation requires draining the condensate water away from
the unit, install a field--supplied 2--in. trap at the condensate
connection to ensure proper drainage. Condensate trap is available
as an accessory or is field--supplied. Make sure that the outlet of the
trap is at least 1 in. lower than the unit drain--pan condensate
connection to prevent the pan from overflowing. Connect a drain
trough using a minimum of field--supplied 3/4 --in. PVC or
field--supplied 3/4 --in. copper pipe at outlet end of the 2 --in. trap
(See Fig. 9). Do not undersize the tube. Pitch the drain trough
downward at a slope of at least 1 in. for every 10 ft. of horizontal run.
Be sure to check the drain trough for leaks. Prime the trap at the
beginning of the cooling season start--up.
Step 7—Install Flue Hood
CARBON MONOXIDE POISONING HAZARD
Failure to follow this warning could result in personal injury
or death.
The venting system is designed to ensure proper venting. The
flue hood assembly must be installed as indicated in this
section of the unit installation instructions.
!
WARNING
Install the flue hood as follows:
1. This installation must conform with local building codes and
with the National Fuel Gas Code (NFGC), ANSI Z223.1 (in
Canada, CAN/CGA B149.1, and B149.2) or NFPA
(National Fire Protection Association) latest revision. Refer
to provincial and local plumbing or wastewater codes and
other applicable local codes.
2. Remove flue hood from shipping location (inside the return
section of the blower compartment--See Fig. 8). Remove the
return duct cover to locate the flue hood. Remove two screws
on flue panel. Place flue hood assembly over flue panel.
Orient screw holes in flue hood with holes in the flue panel.
3. Secure flue hood to flue panel by inserting a single screw on
the top and the bottom of the hood.
Supply Duct Cover
Return Duct Cover
A06320
Fig. 8 -- 48DU with Duct Covers On
1” (25mm) MIN.
2” (50mm) MIN.
TRAP
OUTLET
C99013
Fig. 9 -- Condensate Trap
Step 8—Install Gas Piping
The gas supply pipe enters the unit through the access hole
provided. The gas connection to the unit is made to the 1/2--in. FPT
gas inlet on the gas valve.
Install a gas supply line that runs to the heating section. Refer to
Table 2 and the current edition of NFGC in the U.S. and the current
NSCNGPIC in Canada. Do not use cast--iron pipe. It is
recommended that a black iron pipe is used. Check the local utility
for recommendations concerning existing lines. Size gas supply
piping for 0.5 in. wg maximum pressure drop. Never use pipe
smaller than the 1/2--in. FPT gas inlet on the unit gas valve.
For natural gas applications, the gas pressure at unit gas connection
must not be less than 4.0 in. wg or greater than 13 in. wg while the
unit is operating. For propane applications, refer to propane
conversion kit instructions.
A 1/8--in. NPT plugged tapping, accessible for test gauge
connection, must be installed immediately upstream of the gas
supply connection to the gas valve and downstream of manual
equipment shutoff valve.
When installing the gas supply line, observe local codes pertaining
to gas pipe installations. Refer to the NFGC ANSI Z223.1--2005
NFPA latest edition (in Canada, CAN/CGA B149.1).
NOTE
:In the state of Massachusetts:
1. Gas supply connections MUST be performed by a licensed
plumber or gas fitter.
2. When flexible connectors are used, the maximum length
shall not exceed 36 inches (915 mm).
3. When lever handle type manual equipment shutoff valves
are used, they shall be T--handle valves.
4. The use of copper tubing for gas piping is NOT approved by
the state of Massachusetts.
In the absence of local building codes, adhere to the following
pertinent recommendations:
1. Avoid low spots in long runs of pipe. Grade all pipe 1/4 in.
for every 15 ft of length to prevent traps. Grade all horizontal
runs downward to risers. Use risers to connect to heating
section and to meter.
2. Protect all segments of piping system against physical and
thermal damage. Support all piping with appropriate straps,
hangers, etc. Use a minimum of one hanger every 6 ft. For
pipe sizes larger than 1/2 in., follow recommendations of
national codes.
3. Apply joint compound (pipe dope) sparingly and only to
male threads of joint when making pipe connections. Use
only pipe dope that is resistant to action of liquefied
petroleum gases as specified by local and/or national codes.
Never use Teflon tape.
4. Install sediment trap in riser leading to heating section (See
Fig. 10). This drip leg functions as a trap for dirt and
condensate.
5. Install an accessible, external, manual main shutoff valve in
gas supply pipe within 6 ft of heating section.
6. Install ground--joint union close to heating section between
unit manual shutoff and external manual main shut off valve.
48D
U