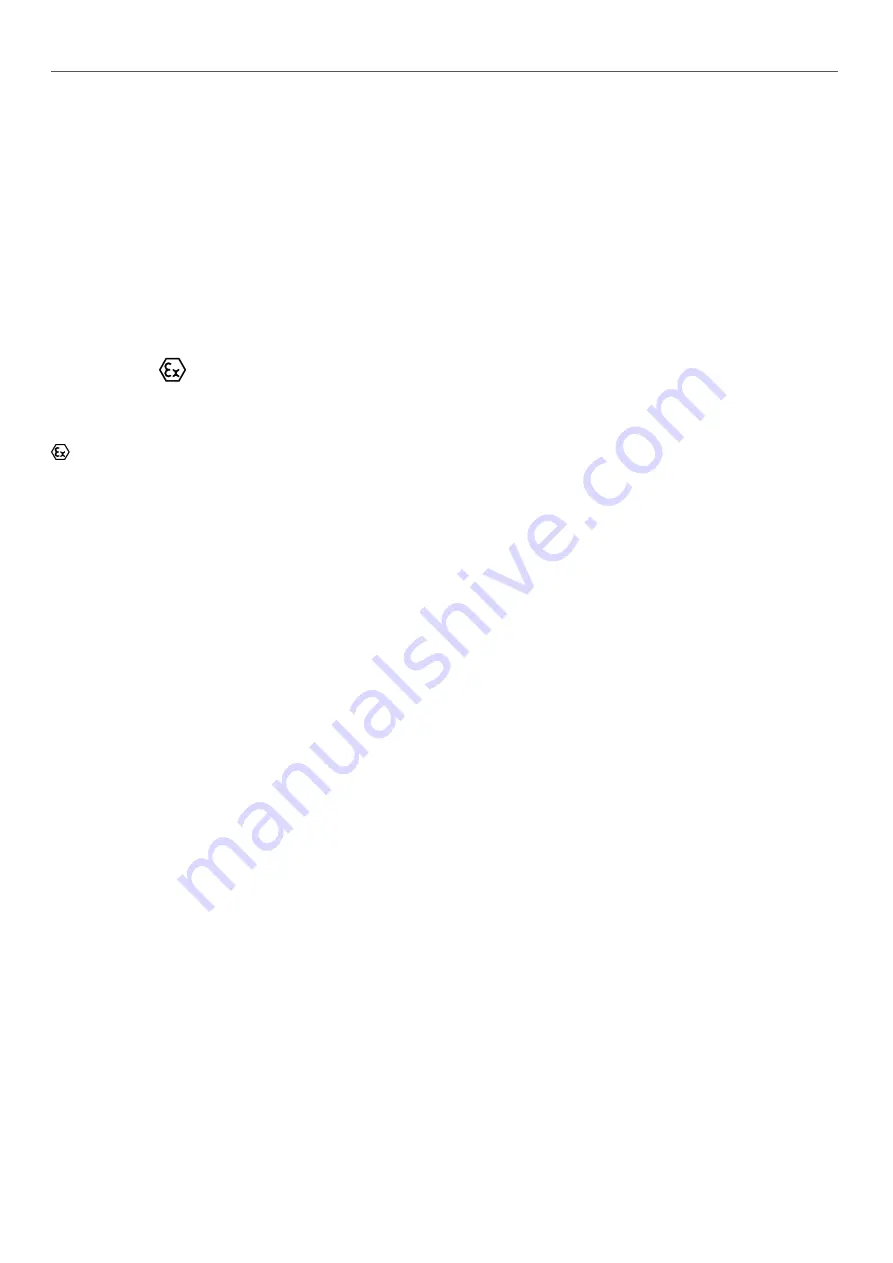
7 - SPECIAL INFORMATION FOR ATEX AREAS
in accordance with directive 2014/34/UE (explosive atmospheres)
7.1 - General information
-Evaluation of the level of danger of explosion established in
accordance with standards EN 13463-1 : 2009 and
EN 1127-1 : 2011.
-The user must classify the various potentially explosive areas
in accordance with directive 1999/92/EC.
-The air handling units are selected and manufactured based
on the type of area defined by the user.
IMPORTANT: A unit must never operate under conditions
other than those it was designed for.
7.2 - Marking
Each unit is supplied with an ATEX Conformity Certificate; the
ATEX marking is inscribed on the name plate as shown below:
Example:
II
2G/3G Ex h
IIB / IIC
(or IIB+ H2) T...°C or TX Gb/Gc (*)
* The labelling and the equipment integrated into the unit are
adapted according to the conditions defined by the customer
in the sheet completed prior to ordering
: standardised ATEX logo
II: Group II = surface industries
Equipment category (2 or 3 depending on zone 1 or 2).
-Ex h: Regulatory markings according to standard NF EN ISO
80079-36:2016
-Gas group subdivision IIA, IIB or IIC
-The IIB labelling is suitable for gas group subdivisions IIA
and IIB
-For group IIC, in the presence of hydrogen, depending on
the labelling of the integrated components, the device
labelling may be IIB + H2
-TX (indicates the maximum permitted surface temperature)
may either :
• Be replaced in the labelling by the temperature class given
in the operating conditions defined by the customer - T1
(450 °C) to T6 (85 °C).
• State the actual temperature (Preceded by the letter T and
followed by the unit °C).
-EPL: (“Explosion Protection Level”) G for gas, followed by
the level b or c depending on the category of equipment.
For category 2, a copy of the technical conformity dossier is saved
and archived for 10 years by a notified body. The archiving number
for the dossier is sent to the customer.
7.3 - System start-up, maintenance
-
The units must be installed and commissioned by a qualified
professional.
-All the provisions set out by the current directives and
standards must be respected during installation, for example,
automatically linking the unit’s supply to the presence of a
flow rate detected by a sensor.
-In all cases, refer to the general information section of this
manual, to the specific manuals for the ATEX components
built into the unit and listed in the ATEX dossier, and to the
specific precautions below:
• Install the units so that the temperatures at and around the
intake are between – 20 and + 60 °C.
• The units and the additional metal elements must be
connected electrically by a grounding cable linked to the
frame.
• Select and install all the electrical connection and control
components according to the risk zone in which they will
be installed.
• All remote metal components (sheaths, pipes, etc.) must
be grounded, if necessary by grounding cables.
• A l w a y s c o n n e c t t h e m o t o r h e a t p r o t e c t i o n
(see § 4 – SYSTEM START-UP)
-The installer must use all available devices to ensure that
the temperature of the various elements of the installation
remains below the autoignition temperature of the gas and/
or the dust in question.
-If the connections to the various pieces of built-in equipment
require feeding through walls (passage of cables, sensors,
etc.), these feedthroughs must be sealed to prevent the
“ATEX” atmosphere from dispersing. The same is true for the
connections between the various blocks which form the unit
and for the connections to the ducts.
-
Any modification to the unit without prior approval from
CARRIER is prohibited.
-Ensure that, during assembly or maintenance operations, no
element (tools, screws, components) are left in the unit, as
this could cause a dangerous situation to arise (see section
“Information concerning the use of tools in explosive
atmospheres”).
-Prior to any maintenance operation, ensure that the unit is
powered off.
-After each maintenance operation, check that all the removed
components have been refitted and secured in their original
position.
-Ensure that the ground straps are in good condition and
reconnected.
-Regularly check that removable components, such as
enclosures or covers, and movable components, such as
damper blades or filter runners, are secure.
■
Exchanger coils:
-
The temperature of the fluids circulating in the coils must not
exceed the value given on the unit’s name plate.
-It must be below the surface temperature limit (or temperature
class) corresponding to the ATEX atmosphere for which the
unit is certified. (see § 7.2)
24
Summary of Contents for 39CZ
Page 2: ...2...