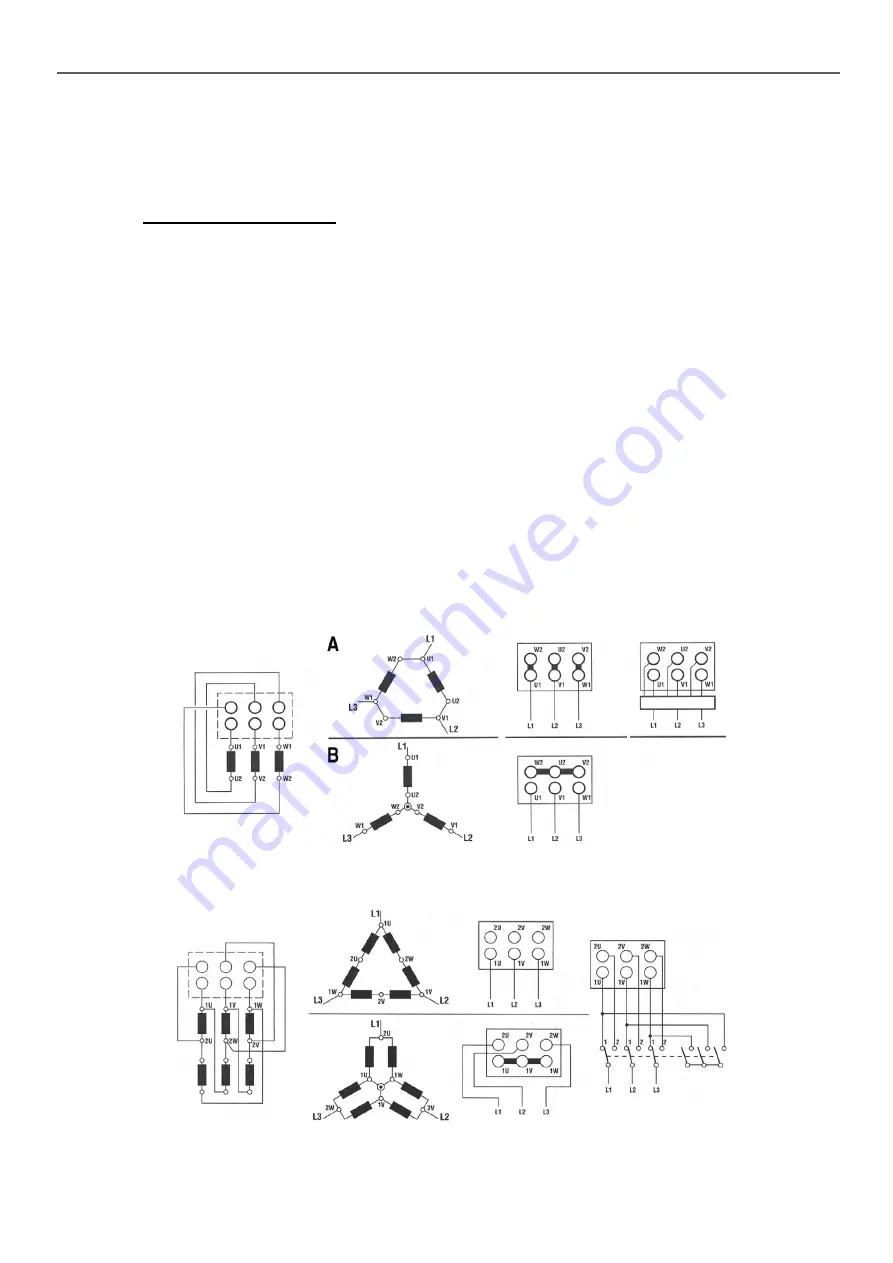
4 - SYSTEM START-UP
Keep all inspection doors closed while the unit is operating.
A safety device protecting against insufficient air flow must inserted in the fan control.
IMPORTANT: Connect all electric components to earth.
4.1 - Connecting the electric motor
The connection must be made by a qualified technician, as per the diagrams below and those included with the motor.
IMPORTANT: Before powering up the motor
, test the insulation resistance. Failure to follow this recommendation will void
the motor warranty.
■
Operating mode:
-Before carrying out any work, disconnect and uncouple the motor or the driven machine.
-Measure the motor's insulation resistance before starting it up, particularly if the windings may be wet.
•
The insulation resistance, corrected to 25°C, must exceed the reference value (100 MΩ) (measured under 500 or 1000 V CC).
• The insulation resistance value is reduced by 50% if the room temperature increases by 20°C.
-Fit the motor casing and discharge the cables against the casing immediately after each measurement to prevent the risk of
electric shocks.
-If you do not obtain the reference resistance value, the windings are too wet. They must then be dried in an oven at a temperature
of 90°C for 12 to 16 hours, then at 105°C for 6 to 8 hours.
•
During drying, remove the covers from the bleed holes and open the closure valves (if fitted to the motor). Remember to close
them after drying. If the bleed caps are fixed, it is recommended to remove the terminal box flanges and covers for the drying
operation.
• Windings which have taken in sea water must normally be rewound.
IMPORTANT: The motors are equipped with a heat protection sensor which must be connected. Check the supply voltage,
the input current and the calibration of the protective devices.
IMPORTANT: For motors with a power of 5.5 kW or above, we recommend Y/∆ starting in order to limit the starting current
(Id/In) and reduce the wear on the drive.
■
Dual voltage type motor with Y coupling, ∆ (6 terminals):
230/400 V motor
-
230 V supply voltage, connection (∆): diagram A.
-400 V supply voltage: (Y) connection: diagram B.
400/690 V motor
-
400 V supply voltage, connection (∆): diagram A.
-690 V AC supply voltage (for P>5.5 kW), connection (Y): diagram B.
■
Dahlander dual-speed motor or motor with reversible poles, 6 terminals.
These diagrams apply to three-phase, 3000/1500 rpm and 1500/750 rpm motors.
Low
speed
(LS)
High
Speed
(HS)
LS and HS for “2” contacts
17
Summary of Contents for 39CZ
Page 2: ...2...