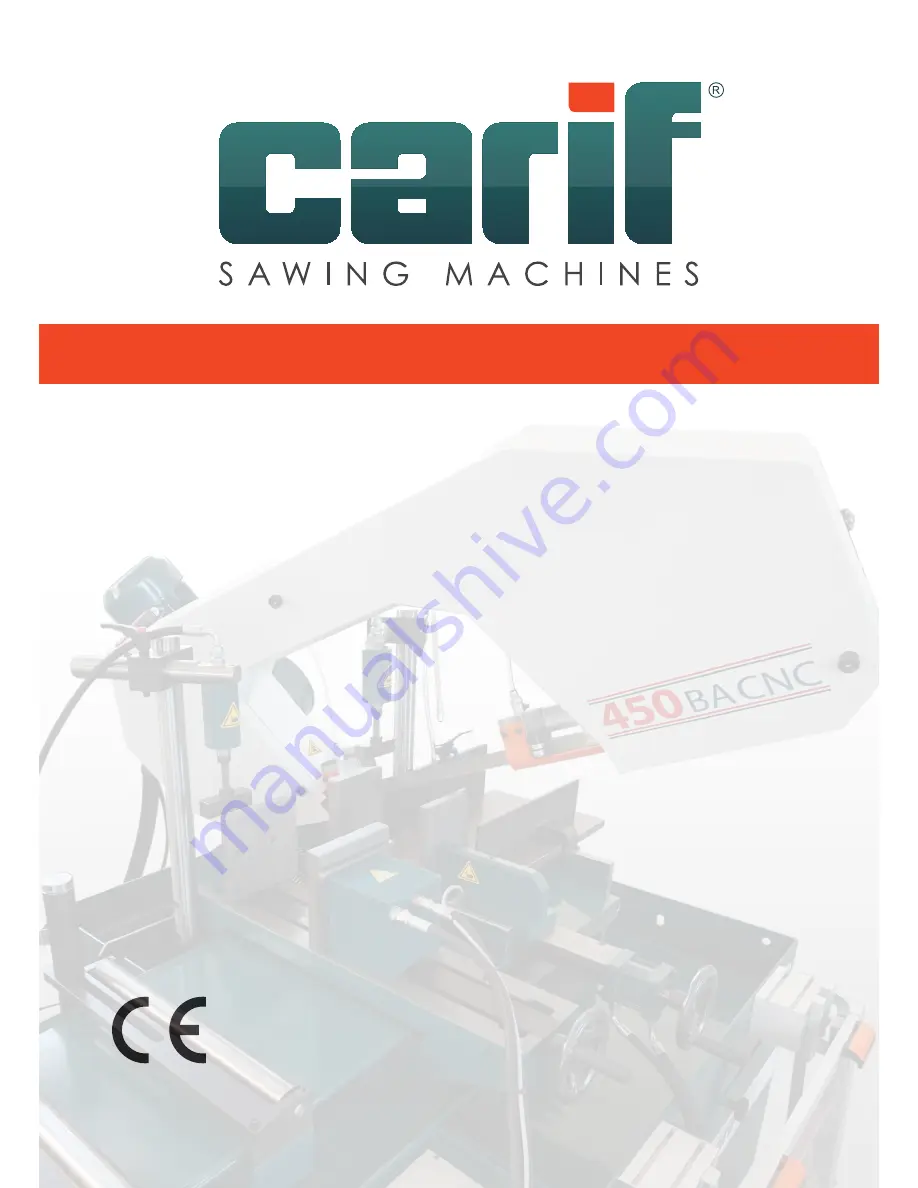
WARNING:
Before starting the machine, please read these instructions completely.
CARIF SAWING MACHINES S.R.L.
Via Tre Salti, 1
I-20029 Turbigo (Ml)
Italy
+39 331 899015
+39 331 898484
www.carif.it
AUTOMATIC HYDRAULIC BAND SAWING MACHINE
“CARIF 450 BA CNC”
Manufacturer:
Address:
Tel :
Fax:
Email:
Web:
Type of machine:
CARIF 450 BA
Instruction manual
Summary of Contents for 450 BA
Page 2: ...450 BA...