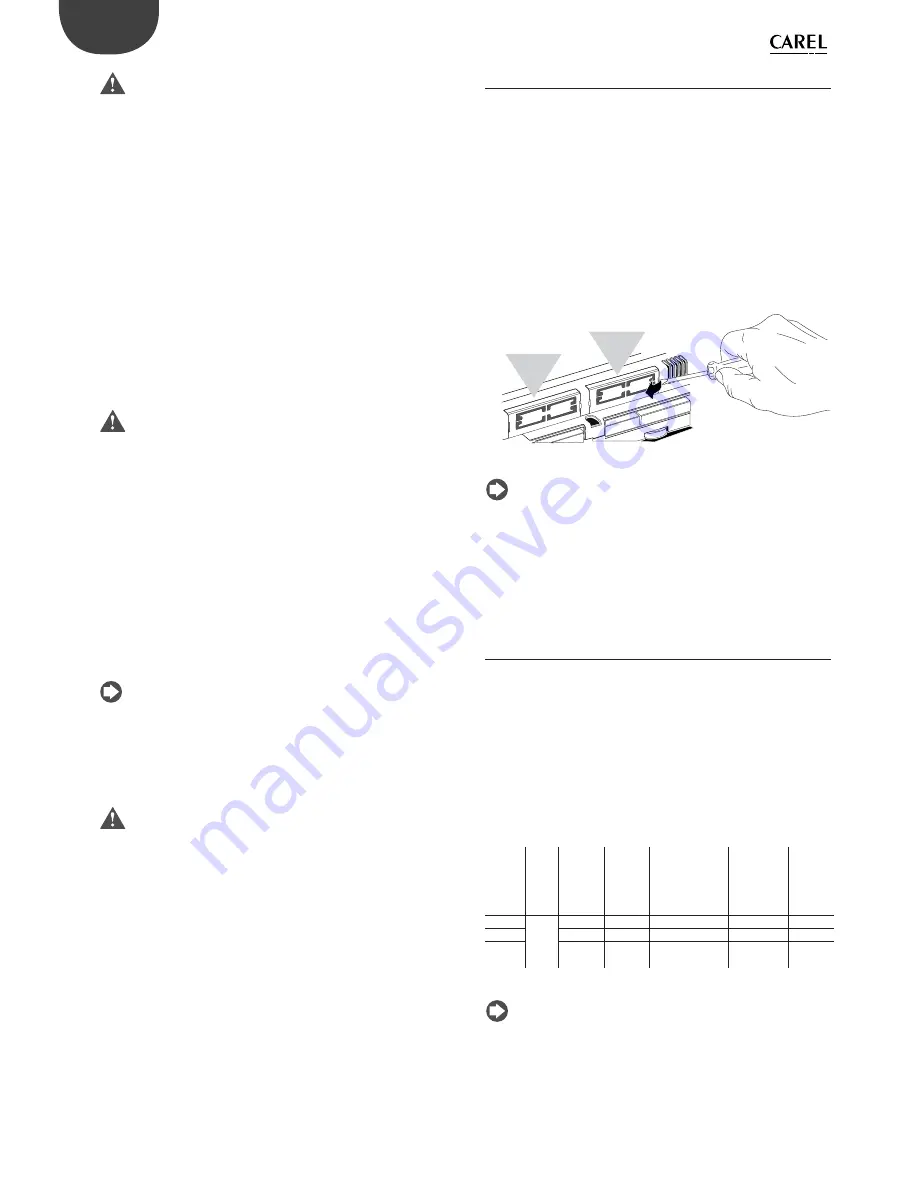
16
ENG
pC0300020EN rel. 1.2 - 07.11.2013
Important:
•
For safety reasons the controller should be installed inside an electrical
panel so that the only accessible parts are the display and the built-in
terminal’s keypad.
•
Install the controller so that the disconnection devices can be used
safely and without hindrance.
•
When laying out the wiring, separate as much as possible the probe
cables, digital input cables and serial line cables from the power
cables (connected to contactors, thermomagnetic devices, etc.) avoid
electromagnetic interference.
•
Never run power cables and probe signal cables in the same conduits
(including the ones in the electrical panels).
•
For control signals, use shielded cables with twisted wires. If the control
cables have to cross over power cables, the intersections should be as
close as possible to 90 degrees; under no circumstances should the
control cables be laid parallel to the power cables.
•
Keep the paths of the probe cables as short as possible and avoid
making spiral paths that enclose power devices.
•
In case of malfunctions do not attempt to repair the device, but
contact a CAREL service centre.
Electrical installation
Important:
Before servicing the equipment in any way disconnect
the controller from the power mains by putting the system’s main switch
on OFF.
Make sure the system is provided with a power disconnector conforming
to regulations. Use cable lugs that are suitable for the terminals used.
Loosen each screw and insert the cable lugs, then tighten the screws.
There is no limit to the number of wires that can be connected to
each individual terminal. When tightening the terminal screws apply
a tightening torque no greater than 0.6 Nm. For information on the
maximum allowable length of the connections to the analogue/digital
inputs and to the analogue outputs please refer to the “Technical
Specifi cations” table. In environments subject to strong disturbance use
shielded cables with the braiding bonded to the earthing conductor
in the electrical panel. The terminals can accept wires with a maximum
cross-section of 2.5 mm2 (12 AWG). After making the connection, gently
tug on the cables to make sure they are suffi
ciently tight.
Note:
•
secure the cables connected to the controller with clamps placed at 3
cm from the connectors;
•
if the power transformer's secondary winding is earthed, make sure
the earth conductor is bonded to the conductor that goes to the
controller and is connected to terminal G0. This applies to all the
devices connected to the controller through a serial network.
Important:
•
Using a supply voltage other than specifi ed can seriously damage the
system.
•
Connect the fuse close to the controller.
•
Installing, servicing and inspecting the controller should be done
only be qualifi ed personnel and in compliance with national and local
regulations.
•
All the very low voltage connections (24 Vac/Vdc or 28 to 36 Vdc
analogue and digital inputs, analogue outputs, serial bus connections,
power supplies) must have reinforced or double insulation from the
power mains.
•
Avoid touching or nearly touching the electronic components
mounted on the boards to avoid electrostatic discharges from the
operator to the components, which can be very damaging.
•
Do not press the screwdriver on the connectors with excessive force,
to avoid damaging the controller.
•
Using the device in any way other than specifi ed by the Manufacturer
can compromise its protection system.
•
Use only optional boards and connectors supplied by CAREL.
4.3 Preliminary
operations
Installing the serial cards
If the Fieldbus and BMS serial cards built into the pCO5+ are insuffi
cient
for the required application, you can add a Fieldbus serial port and a BMS
serial port, which are available as accessories (see chap.1).
To install them, proceed as follows:
1.
Locate the Fieldbus or BMS serial port.
2.
Using a screwdriver, take off the cover.
3.
Using a pair of nippers, cut out the perforated plastic part to create
an opening.
4.
Plug the optional card into the edge-card connector, making sure it
is fi rmly secured and makes contact.
5.
Put back the cover so that the serial card’s connector is aligned with
the opening.
6.
Make the electrical connections required.
F
ie
l
dB
u
s
card
BMS
card
Fig. 4.b
Note:
For details, refer to the instructions sheets of the cards to
install.
Installing the pCOe expansion card
See instructions sheet code +050003265.
Installing the Ultracap module
See instructions sheets codes +0500042IE and +0500041IE.
4.4 Serial network electrical connections
To improve the controller’s immunity against electromagnetic
interference, the serial connection cable should be a shielded twisted
pair cable, 2-pole or 3-pole depending on the insulation of the serial
connection. The following rule applies:
•
if the serial port is isolated (functionally) from the power supply, a third
wire is required in the serial cable to act as a common reference for the
controllers. If the serial port is not optically isolated and the common
reference is already present, no third wire is required.
Technical specifi cations for connections
Use a shielded, twisted pair cable (AWG 20-22) with inter-conductor
capacitance <90pF/m.
Master
device
HW
Lmax(m)
Wire/
wire
capaci-
tance
(pF/m)
Resistance on
fi rst and last
devices
Max. no.
of slave
devices on
bus
Data rate
(bit/s)
FBUS
RS485
1000
< 90
120 Ω
64
19200
PC
1000
< 90
120 Ω
207
38400
pLAN
500
< 90
-
32
62500/
115200
Tab. 4.b
Note:
In case of a Master–Slave network the max. allowable length
is 1000 m. If the network is longer than 100 m, apply 120Ω, 1/4W
terminating resistors to the fi rst and last devices in the network.
Non-optically-isolated serial port
This is the case of the serial ZERO - pLAN (J11), Fieldbus 2 (J23 and J26)
and BMS2 if not optically isolated (on models with built-in ports that are
not optically isolated).
Summary of Contents for pCO5+
Page 2: ......
Page 4: ...4 ENG pCO5plus 0300020EN rel 1 2 07 11 2013...
Page 6: ...6 ENG pCO5plus 0300020EN rel 1 2 07 11 2013...
Page 43: ...43 ENG pCO5plus 0300020EN rel 1 2 07 11 2013...
Page 59: ......