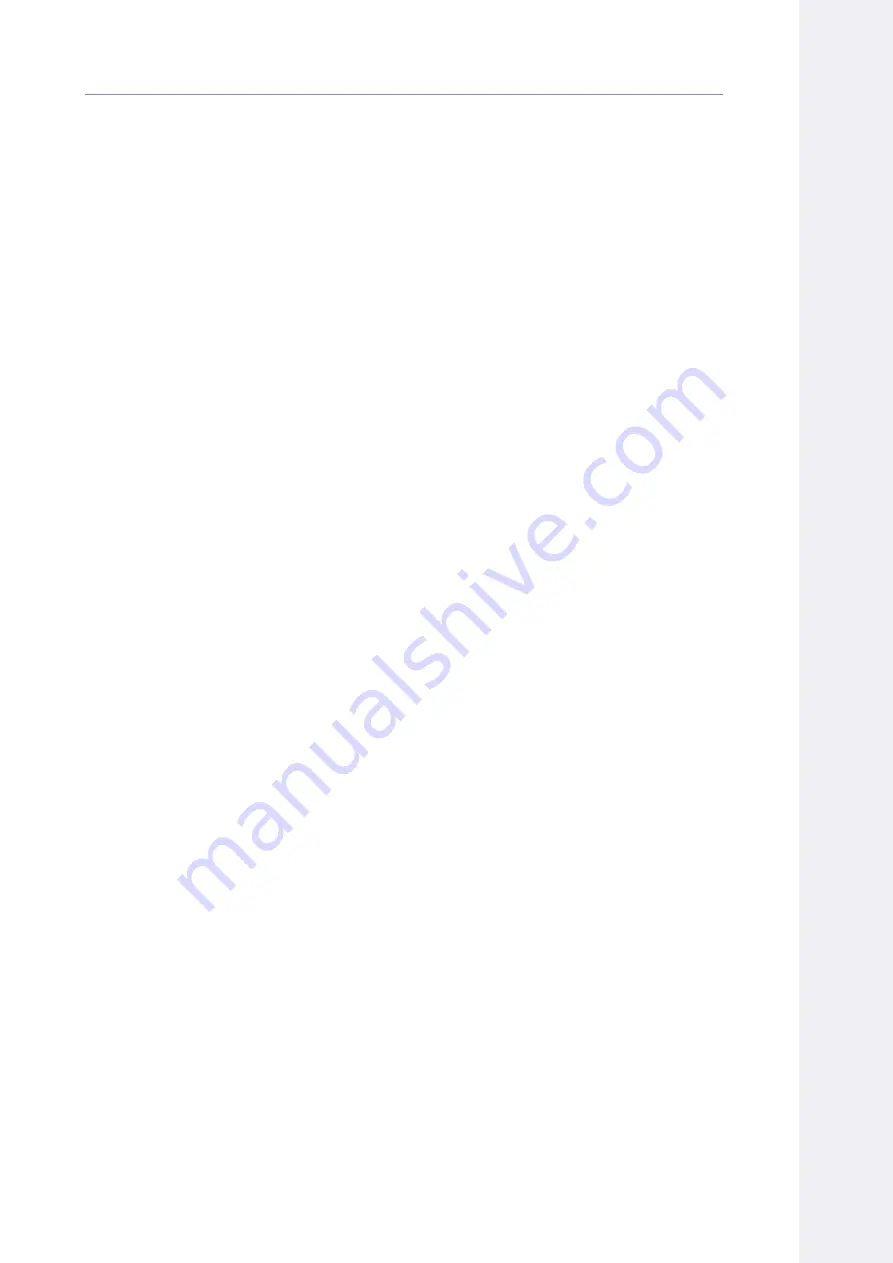
CARBATEC.C OM.AU
WDS-4080P
INTRODUCTION TO DRUM SANDING
C.
REMOVING LUMBER CUP
The ideal machine for removing cup from lumber is a jointer. However, because of
the minimal pressure exerted by the drum sander, it is possible to remove cup, since
the lumber is not compressed flat on feed belt and table. Be patient, this process
can take quite a while depending on cup depth. Feed the stock into the machine cup
crown up (edges resting on feed belt) and use a coarse grit abrasive. Repeat until the
crown is flat. With one face now flat, flip the board over and sand it flat. Do not be
shocked by how thin the board may become after all cup has been removed.
Board wrap and twist will not be remedied by a drum sander, or a planer, for that
matter. Always inspect your lumber for warp and twist before drum sanding since
it is prone to hanging-up in the machine, shorter length lumber in this condition is
especially troublesome.
D.
PLAN YOUR WORK IN ADVANCE
Planning your drum sanding operations in advance will minimize setups, work time,
and frustration level. Group material to be sanded by thickness and grit requirements
and work through each required sanding grit starting with the thickest material
through the thinnest, then change over to the next finer grit and begin the process again.
We suggest that you experiment with the various sanding grits and wood species to
determine the results you can expect before ruining project material. With new set-
ups, always test with scrap lumber before sanding your project material.
E.
WOOD SPECIES TO BE CAUTIOUS WITH
Highly resinous species will tend to quickly clog (load-up) abrasives and in many
cases abrasive loading cannot be removed with belt cleaning sticks. The most
notorious abrasive loaders are some common pine species. It is nearly impossible to
clear the abrasive of the pitch, sap, sawdust combination.
Be aware of species that have toxic properties, such as members of the rosewood
family (i.e. cocobolo). Despite dust control, you may inhale small airborne particular
or suffer allergic reactions through handling of stock.
Wear applicable AS/ANZ approved PPE.
15