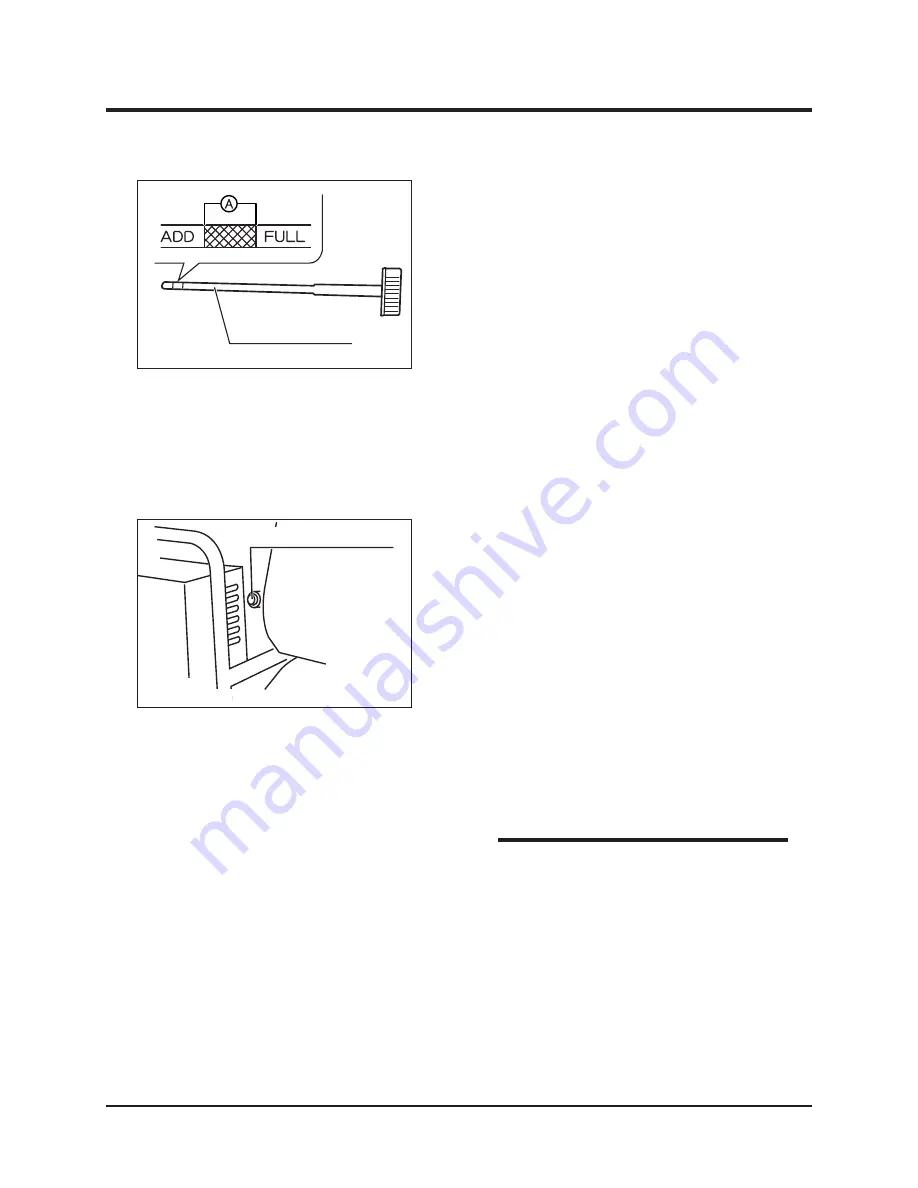
Maintenance
-50-
7
4. Add the specified engine oil when the oil level
is lower than range indicated by "A" on the oil
level gage.
5. Replace the present engine oil with new
oil if present oil is noticeably dirty or has
deteriorated into poor viscosity.
Oil level gauge
5310M-0601-050-E
Oil drain plug
1. Position a vessel suitable for receiving the
engine oil under the oil drain plug.
2. Remove the drain plug and drain the engine oil
into the vessel.
3. Securely replace oil drain plug.
4. Remove the cap from the oil filler port.
5. Add fresh specified engine oil to the oil filler
port.
6. Confirm that the new oil level is within range
indicated by “A” on the oil level gage.
7. Securely attach the cap to the oil filler port.
Replacing Oil
Adding Oil
1. Add the specified engine oil to the oil filler port.
2. Confirm that the oil level is within range
indicated by “A” on the oil level gage.
3. Securely attach the cap to the oil filler port.
* Specified engine oil: See page 47
* Amount of engine oil: See page 47
NOTE
5310M-0701-010-E