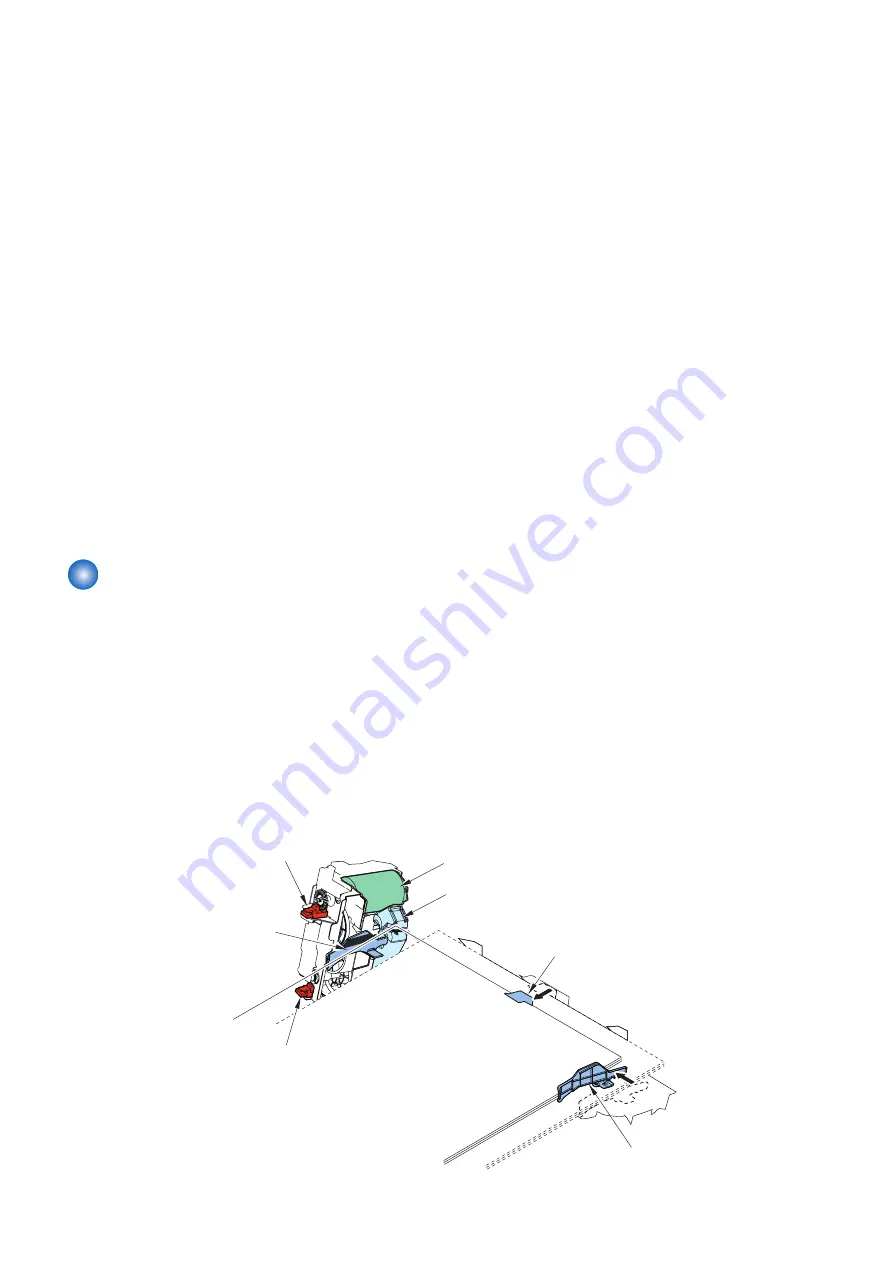
If the staple setting exceeds the stapling capacity (small size: 50sheets, large size: 30 sheets) that can be bound, divided delivery
is performed.
If the upper limit is exceeded, shift-sort mode is used for the second and subsequent copies.
Example: Divided delivery for 51 A4 (80g/m
2
) sheets 50 sheets are delivered in a stack
without stapling. The 51st sheet is delivered by itself.
Related service mode
• Adjustment of front 1-stapling position:
SORTER > ADJUST > INSTP-F1
• Adjustment of rear 1-stapling position:
SORTER > ADJUST > INSTP-R1
• Adjustment of 2-stapling position:
SORTER > ADJUST > STP-2P
• Setting of the duration of time to keep manual staple mode enabled after execution of manual stapling:
SORTER > OPTION > MSTP-WT
• Setting of the duration of time before executing automatic stapling at manual staple mode:
SORTER > OPTION > MSTP-TMG
• Adjustment of manual stapling position:
SORTER > ADJUST > MSTP-2P
Related error code
• E531-8001: Stapler motor error
• E531-8002: Stapler motor error
• E532-8001: Stapler shift motor error
• E532-8002: Stapler shift motor error
Staple-free Staple Operation
■ Outline
When staple-free stapling is specified, the paper is moved to the staple-free stapling position by the front alignment plate and
assist guide. The paper stack is clinched by the clinch arm.
The clinch arm's home position is detected by the clinch HP sensor (PS15).
After power ON, the finisher controller PCB drives the clinch motor (M9) to return the clinch arm to the home position. If the clinch
arm is at the home position to begin with, it remains there and waits.
Clinch errors are detected using clock pulses from the clinch motor drive detection sensor (PS13).
The staple-free staple unit is fixed in place in the rear of the finisher. Only a single stapling position is used, which is at the rear.
Stapling at four locations (upper left, upper right, lower right, lower left) is possible using the host machine's LUI through image
processing of the printed surface.
After staple-free stapling, the paper stack is delivered by the assist guide.
Clinch HP Sensor (PS15)
Clinch Motor
Drive Detection Sensor (PS13)
Clinch Motor (M9)
Front Alignment Plate
Rear Alignment
Plate
Assist Guide
Clinch Arm
2. Technical Explanation
29
Summary of Contents for Inner Finisher-L1
Page 11: ...Product Overview 1 Features 5 Specifications 6 Name of Parts 9 ...
Page 46: ...Periodical Service 3 List of Work for Scheduled Servicing 40 ...
Page 58: ...1x 1x 1 2 5 Remove the Interface Cover 1 2 Claws 2 1 2 4 Parts Replacement and Cleaning 51 ...
Page 122: ...Troubleshooting 6 Making Initial Checks 116 Processing Tray Area 117 ...
Page 126: ...APPENDICES Service Tools 120 General Circuit Diagram 121 ...