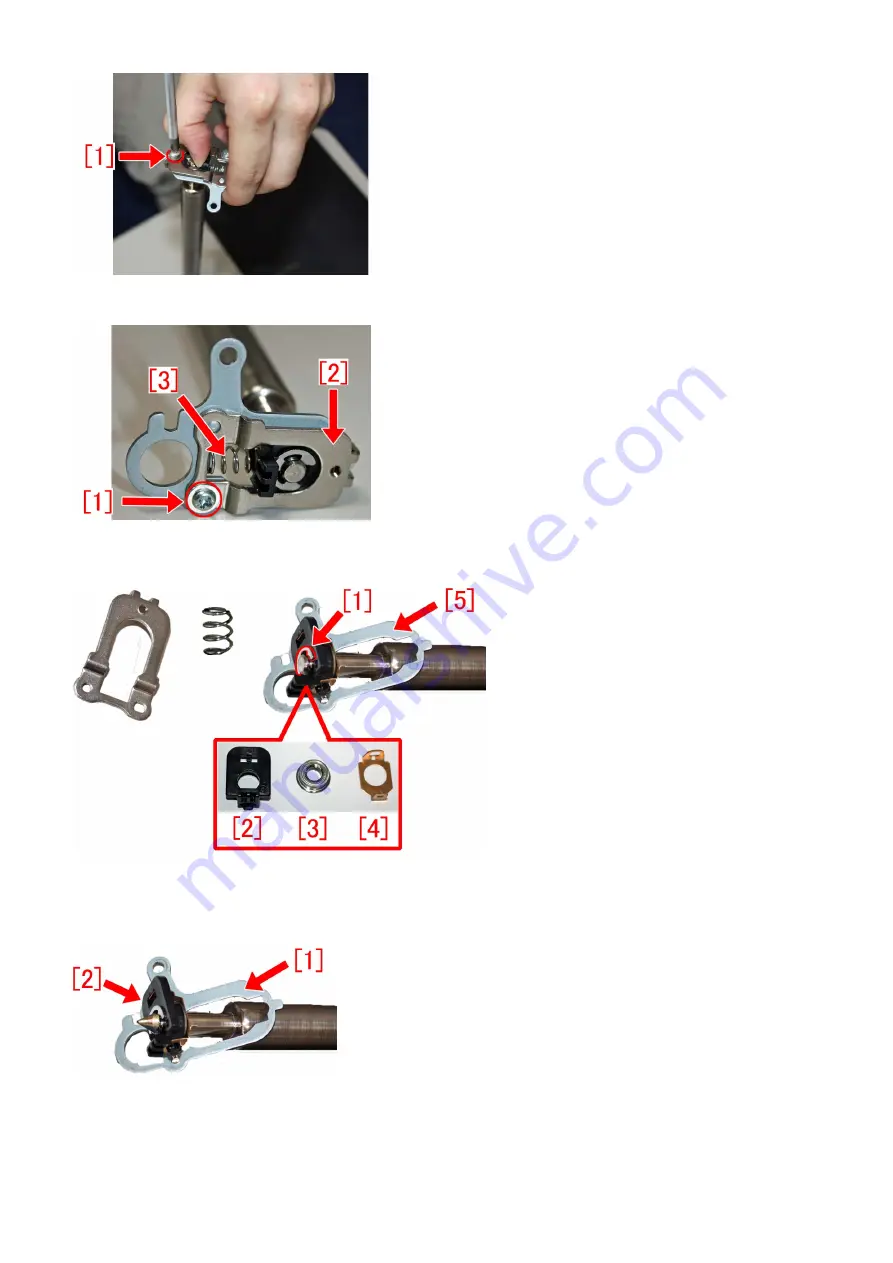
c-3) Remove the screw [1]. Then, remove the sheet metal [2] and the spring [3].
c-4) Remove the E-ring [1]. Then, remove the roller holder [2], the ball bearing [3], the stopper plate [4] and the sheet metal [5]
from the shaft.
c-5) Attach the ball bearing and the stopper plate removed in the step c-4) to the new type roller holder (FE4-6074-010).
c-6) Insert the sheet metal [1] to the front shaft part of the new type tension roller (FE4-6069-010) and fix the roller holder [2]
assembled in the step c-5) by the new type E-ring (XD2-1100-502).
[Reference]
- There is a groove on the front shaft part of the tension roller. Be sure to attach the roller holder to the shaft part with a groove.
112
Summary of Contents for imagePRESS C10000VPSeries
Page 1: ...Troubleshooting Guide imagePRESS C10000VPSeries July 16 2019 Canon U S A Inc ...
Page 28: ...4 If the symptom does not improve then check other factors 23 ...
Page 42: ...3 Output about 10 test prints to verify the effect 37 ...
Page 142: ...Model Serial number PAPER DECK UNIT_ F1 A4 WES05369 137 ...
Page 164: ...4 5 Make some prints and check that the above issue does not occur 159 ...
Page 179: ...C 2 24VB system C 3 24VC system C 4 24VD system C 5 24VE system 174 ...
Page 180: ...C 6 24VF system C 7 24VH system C 8 24VI system C 9 24VJ system 175 ...
Page 181: ...176 ...
Page 261: ... Service parts CABLE MOTOR CONNECTING FM1 T808 256 ...