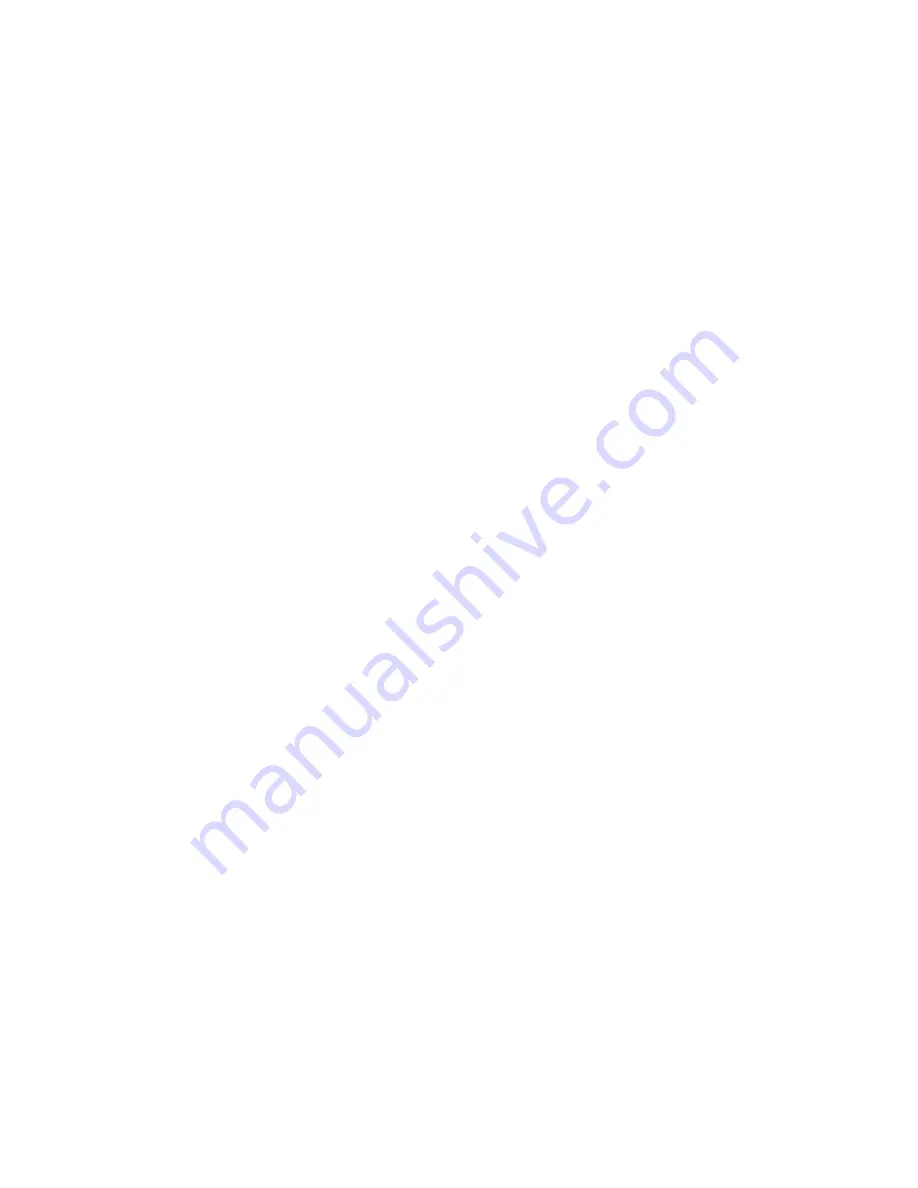
36
9.3
OPERATION SQUENCE
POWER ON
Demand for heat
BTC Staging control 30 seconds count down
before energizing the first stage. Next the stage
switch closes.
Pre-purge
Fan manager energizes starting 15 seconds of
pre-purge cycle.
Ignition Trial
On proof of air flow, the air proving switch closes
and energizes the ignition module. The module
first initiates a self check and then starts the pilot
ignition sequence. The safety shutoff valve
opens, which allows gas to flow to the pilot
burner. At the same time, the electronic spark
generator in the module produces 10,000 Volt
spark pulse output. The voltage generates a
spark at the igniter that ignites the pilot. If the
pilot does not light, or the pilot flame current is
not at least, on average, 1.5 μA and steady, the
module will not energize the combination valve
and the main burner will not light. The ignition
module provides 100% gas shutoff, followed by
retry for ignition. If required (e.g. CSD1) a
module with lockout feature can be provided.
Main Burner
When the pilot flame is established, a flame
rectification circuit is completed between the
sensor and the burner ground. The flame
sensing circuit in the ignition module detects the
flame current, shuts off the spark generator and
energizes the combination valve operator. The
combination valve opens and gas flows to the
main burner, where it is ignited by the pilot
burner. On the lock out ignition module, the
flame current also holds the safety lockout timer
in the reset operating condition. When the call
for heat ends, both valve operators are de-
energized, and both valves in the gas control
close.
Normal Operation
Staging
is
controlled
from
the
Boiler
Temperature
Controller
(BTC).
The BTC
operates the boiler stages to maintain the target
temperature.
Demand Satisfied
Boiler Temperature Controller senses that the
boiler target temperature was reached and de-
energizes the stage 1 contact.
Staging Control Alarms
High limit or low water flow will de-energize all
gas valves, and the blower. Condition indicators
are visible on the control panel. Each
burner/blower set is provided with its own air
pressure switch. If a low air pressure condition is
present, power will not be supplied to the ignition
module. The blower will remain on and the air
indicator will remain on for as long as there is a
call for heat.
Summary of Contents for MICOFLAME GRANDE Series
Page 2: ......
Page 4: ......
Page 20: ...16 Figure 7 Typical Heating System ...
Page 21: ...17 Figure 8 Typical Low Water Temperature System Figure 9 Typical Instantaneous Water System ...
Page 47: ...43 ...
Page 48: ...44 ...
Page 49: ...45 16 EXPLODED VIEW MicoFlame Grande ...
Page 50: ...46 EXPLODED VIEW MicoFlame Grande Outdoor and or Condensing ...