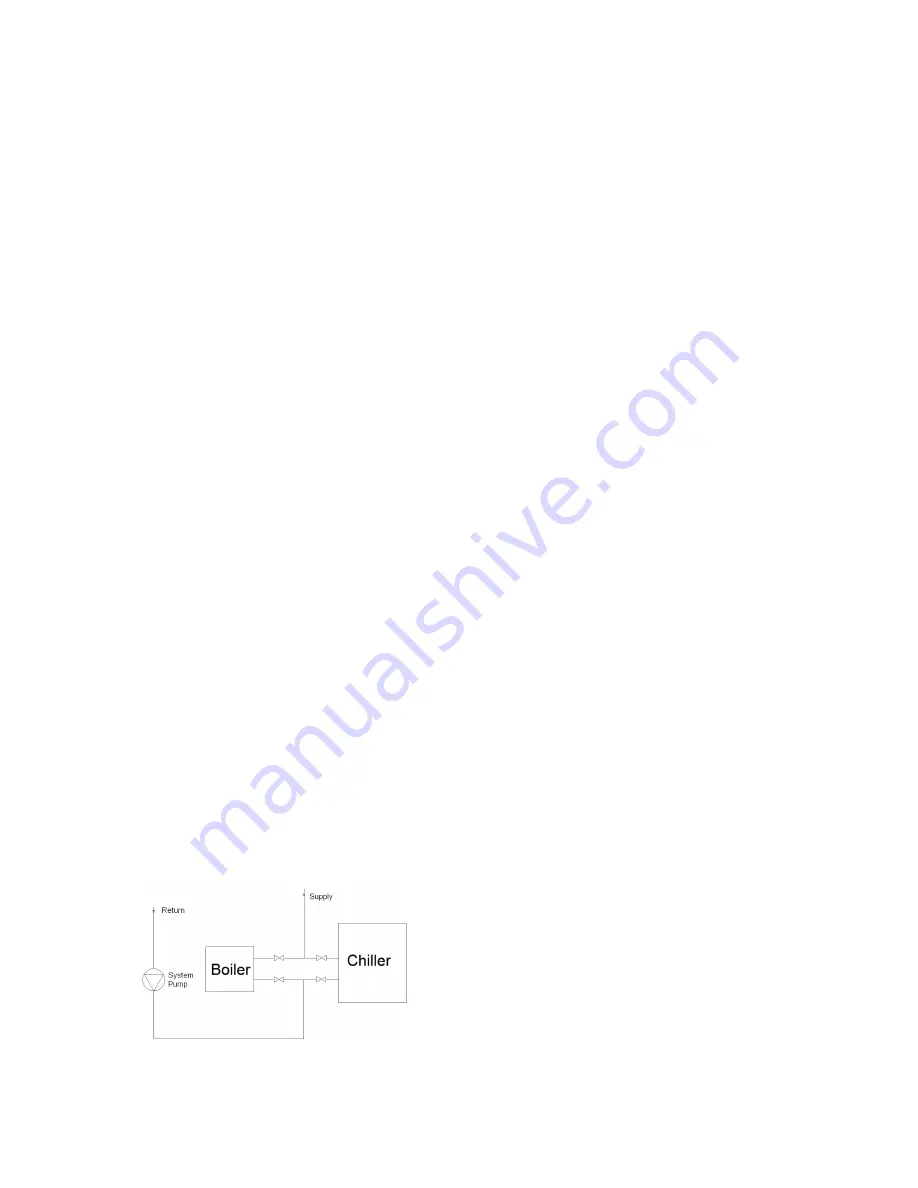
14
increase the GPM flow by 15% and the
head loss by 20%.
The
following
example
demonstrates
the
procedure to follow for calculating the revised
head for the heat exchanger when using a water /
glycol mixture.
Given that Camus is showing a heat
exchanger flow and head loss of 100
gpm @ 10 feet
Increasing the flow by 15% now results in a
head loss of 13 feet at 115 gpm (from B&G
system syzer). At this increased flow
Camus now recommends to increase the
head loss by 20%.
The requirement for the heat exchanger
with water / glycol mixture will now be
115 gpm @ 15.6 feet. (ie. 1.2 x 13ft. =
15.6 ft.)
A similar procedure must be followed to
calculate the additional head loss in pipe
and fittings in order to arrive at the proper
pump selection.
For Outdoor installations regular inspections
should be made to ensure that air intake and vent
are clear. Always consider the use of a shelter
such as a garden shed in lieu of direct exposure
of the appliance to the elements. The additional
protection afforded by the shelter will help to
minimize nuisance problems with electrical
connections and will allow easier servicing of the
appliance under severe weather conditions.
7.3
CHILLED WATER SYSTEMS
When an appliance is connected to an air
conditioning system where the same water is
used for heating and cooling, the chiller must be
piped in parallel with the appliance. Appropriate
flow control valves; manual or motorized must be
provided to prevent the chilled water from
entering the appliance. (See figure 6)
Figure 6 – Typical Chilled Water System
When an appliance is connected to heating
coils located in air handling units (where they
may be exposed to refrigerated air circulation),
the appliance piping system shall be equipped
with a flow control valve or other automatic
means to prevent gravity circulation of chilled
water through the appliance. Chilled water in
the appliance will create condensate on the
appliance tubes, which will collect in the
combustion chamber causing corrosion.
7.4
HEATING SYSTEM PIPING
In larger systems, it is advisable to connect the
appliance to the piping employing the primary-
secondary pumping system. This system is
used to provide system advantages that would
not be available with a single pumping system.
Primary-secondary pumping is illustrated in
Figure 7.
The following are some advantages of the
primary-secondary pumping system:
Greatly reduce the stand by losses
through the appliance
Minimize heat exchanger wear.
Reduce power consumption
7.5
LOW
WATER
TEMPERATURE
SYSTEMS
In applications where the heating system
requires supply water temperatures below
115°F, a recirculation line must be installed
upstream of the appliance pump so that outlet
water can be re-circulated to raise the inlet
temp to a minimum of 115 °F. Balancing
valves, preferably globe valves are used to
adjust flow. (See figure 8)
Adjustment procedure.
a. Fully open bypass and outlet
valves.
b. With appliance running, read
inlet temperature after 15
minutes.
c. If the inlet temperature is less
than 115°F slowly close outlet
valve until the inlet temperature
climbs to 115°F
d. If the inlet temperature is
greater than 115°F but not
greater than 140°F no further
adjustment is required.
Summary of Contents for MICOFLAME GRANDE Series
Page 2: ......
Page 4: ......
Page 20: ...16 Figure 7 Typical Heating System ...
Page 21: ...17 Figure 8 Typical Low Water Temperature System Figure 9 Typical Instantaneous Water System ...
Page 47: ...43 ...
Page 48: ...44 ...
Page 49: ...45 16 EXPLODED VIEW MicoFlame Grande ...
Page 50: ...46 EXPLODED VIEW MicoFlame Grande Outdoor and or Condensing ...