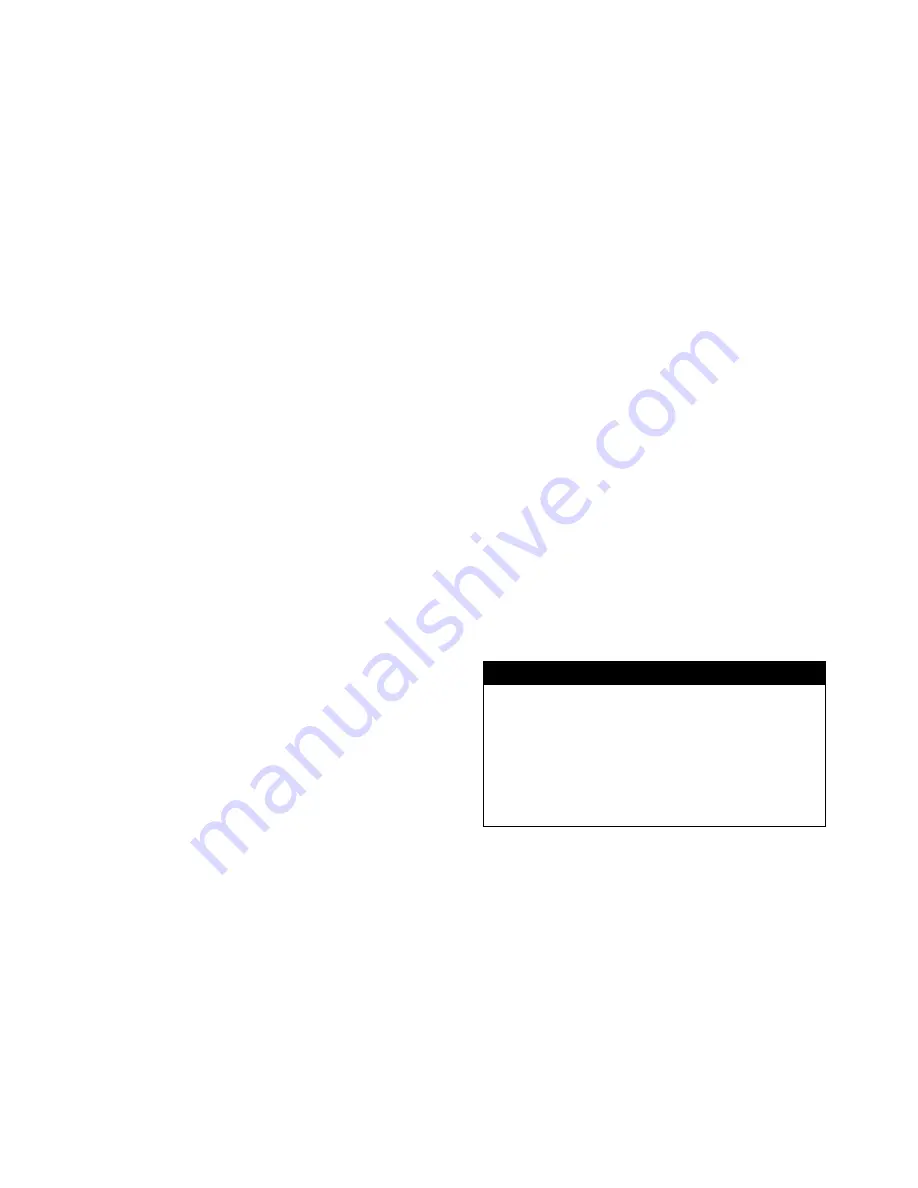
57
10.4.1
CONDENSATE VOLUME
There are several factors affecting the amount of
condensation created by the appliance however for rough
approximation use.
Condensation Volume, US Gallon/Hr = Input, MBH/1000 x
5.0
Many codes will require the acidic condensate to be
neutralized before it can be placed in a drain system. A
neutralizer to control the pH of the liquid discharged to a
drain system is recommended with every appliance. The
neutralizer consists of an industrial grade, non-corrosive
reservoir for collection of the condensate. As the reservoir
fills, it provides an extended residency time to neutralize the
condensate. The neutralized condensate exits from the
reservoir outlet. A ‘P’ trap is installed upstream of
neutralizer at the heat exchanger. Prime the installed
assembly with water to prevent flue gas spillage from the
drain. Use standard ½" vinyl, PVC, CPVC or suitable hose
to run to floor drain.
When the condensate level in the reservoir rises to the
drain, it spills out into the condensate bin and from there
exits to the external neutralizer. As the pH number
increases in numerical value, the relative acidity of the
discharge decreases. The neutralized condensate may
then be discharged into a suitable drain system without fear
of damage to the drain system. Always check with local
codes for specific pH requirements. Neutralizers may be
used in series to raise pH.
The condensate collection box supplied with the
Dynaforce® is supplied with an initial charge of neutralizer
medium. This neutralizer medium is expected to last
approximately 3 to 6 months depending on the amount of
condensate produced. Neutralizer refills are available from
Camus®.
10.5
BURNER MAINTENANCE
The burner should be removed for inspection and cleaning
on an annual basis. An appliance installed in a dust or dirt
contaminated environment will require inspection and
cleaning on a more frequent schedule. The fan assisted
combustion process may force airborne dust and dirt
contaminants, contained in the combustion air, into the
burner.
With
sustained
operation,
non-combustible
contaminants may reduce burner port area, reduce burner
input or cause non-warrantable damage to the burner.
Airborne contaminants such as dust, dirt, concrete dust or
dry wall dust can be drawn into the burner with the
combustion air and block the burner port area. An external
combustion air filter is provided with the appliance. An
additional filter is located at the fan inlet (DR1200 – 5000)
and like the external filter may be washed in the sink under
the tap. This internal filter should be checked and cleaned
at the time of appliance commissioning and on a six month
interval or more often in a contaminated environment.
10.5.1
BURNER REMOVAL
Access to the burner will require the following steps:
•
Turn off main electrical power to the appliance.
•
Turn off main manual gas shutoff to the
appliance
•
Remove the top cover.
•
Disconnect the gas supply connection to the fan
inlet.
•
Disconnect the fan motor power wires at the
harness.
•
Remove the hot surface igniter and the flame
sensor.
•
Remove the sensing tubes from the air ratio gas
valve to the combustion air fan.
•
Remove the 4 nuts holding the fan assembly to
the heat exchanger and remove the fan assembly.
On occasion the red silicone gasket may adhere to
the underside of the fan’s flange. Carefully pry the
flange away from the gasket prior to removing the
fan assembly.
•
The burner can now be lifted vertically out of the
heat exchanger cavity. A graphite-backed ceramic
paper gasket is located directly under the burner
flange. This gasket must be replaced if it is
damaged.
•
Use care to prevent damage to the knitted metal
fiber of the burner surface.
•
Check all gaskets and replace as necessary.
Gaskets affected by heat will not reseal properly
and must be replaced.
•
Replace the burner in the reverse order that it was
removed. Insert the igniter and sensor before
doing the final tightening on the fan mounting nuts.
Evenly tighten the nuts to 20 ft-lbs (models 300 –
1000) and 25 ft-lbs (models 1200 – 5000)
NOTE:
When the combustion air fan is removed for any reason,
the inlet to the burner must be covered to prevent further
foreign objects from falling into the burner. Always look
inside the burner to check for dents. Do not place a burner
back into operation if the inner distribution screen has been
dented during the service operation, call the factory for
recommendations. Use care when removing and handling
the burner, Sharp objects or impact may damage or tear
the metal fiber surface rendering the burner unfit for
service.
10.5.2
BURNER CLEANING PROCEDURE
Remove any visible dust or dirt blockage from the surface
of the burner using water from a garden house. Wash the
burner with low pressure water. Never wipe or brush the
surface of the burner nor use high pressure water or air.
The burner may best be cleaned by immersing the burner
port area in a solution of dishwashing detergent and hot
water. Allow the burner to remain in the solution for a
short period of time to remove dust, dirt and oil or grease
laden contaminants. Rinse the burner thoroughly with
clean water to remove any residue from the detergent
cleaner. The burner should be air dried after removal
from the cleaning solution and rinsing. DO NOT use
chlorine based solvents or cleaning agents on the burner.
Summary of Contents for DRH300
Page 2: ......
Page 6: ......
Page 38: ...32 13 Place toggle switch setting to REMOTE for remote operation if required...
Page 69: ...63 PART 12 EXPLODED VIEW 19 1 2 3 4 5 6 7 8 9 10 11 12 13 14 15 16 17 18 20...
Page 70: ...64 21 22 23 24 26 35 34 33 32 31 30 29 28 27 25 36 37 38 39 40 42 43 56...
Page 77: ...71 PART 13 ELECTRICAL DIAGRAMS...
Page 78: ...72...
Page 79: ...73...
Page 81: ...75...
Page 82: ...76...
Page 83: ...77...
Page 86: ......