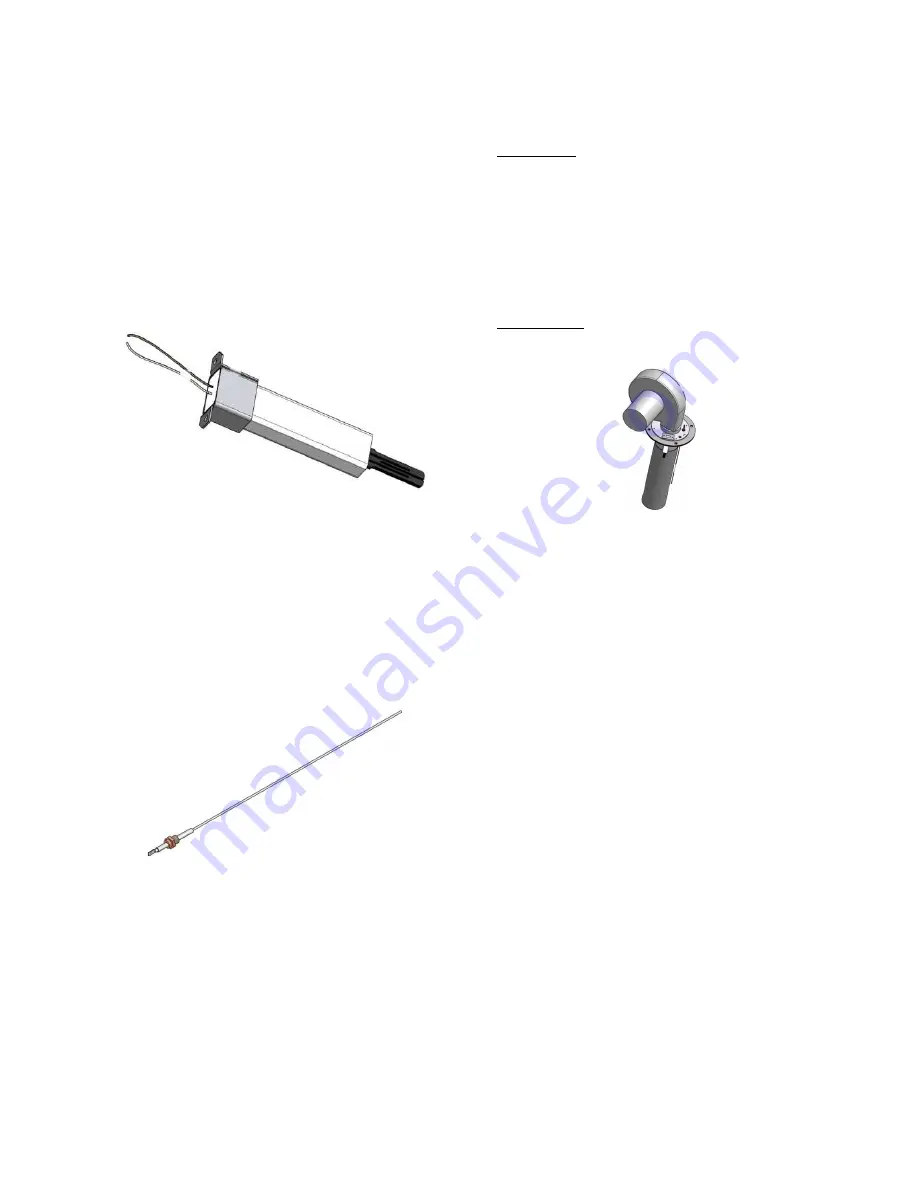
45
PART 7
COMPONENTS
7.1
HOT SURFACE IGNITER (GLOW BAR)
The silicon carbide igniter is inserted directly through the fan
flange and held in place by two screws. A hold down bracket
as well as sealing gasket above and below the igniter assures
a good seal. Care must be taken when removing and/or
installing the igniter since the silicon carbide element is brittle.
Always remove the igniter prior to removing the fan assembly
for inspection of the burner and heat exchanger. A properly
prepared igniter will have a bead of silicone sealing the end
mounting bracket to the ceramic shaft.
Figure 29: Hot Surface Igniter
During trial for ignition a properly operating igniter will generate
a minimum 3.2+/-0.2A which is the current required for reliable
ignition. It is recommended that the hot surface igniter be
replaced every 4,000 hours of appliance operation to maintain
peak ignition efficiency.
7.2
FLAME SENSOR
The flame sensor is inserted directly through the fan flange and
is screwed into the fan flange. Care must be taken, when
installing the flame sensor, to align it perpendicular to the fan
flange and parallel to the burner tube and not to over tighten.
Always remove the flame sensor prior to removing the fan
assembly for inspection of the burner and heat exchanger.
Figure 30: Flame Sensor
The ignition module relies on the flame sensor to provide a
flame rectification signal. Oxide deposits, improper placement
or damaged ceramic insulator will result in insufficient signal
leading to ignition module lock out. For proper operation
minimum 0.8 Vdc must be fed back to the module. Oxide
deposit on the sensor rod must be removed with steel-wool. Do
not use sand-paper since this will contaminate the surface.
7.3
COMBUSTION AIR FAN
DR300 – 1000
Uses a modulating air fan to provide combustible air/gas
mix to the burner and push the products of combustion
through the heat exchanger and venting system. The fan
assembly consists of a sealed housing and fan wheel
constructed from spark resistant material. The fan is
operated by a fully enclosed 120 VAC, Single-Phase
EC/DC electric motor. The fan housing and motor
assembly is fully sealed and SHOULD NOT be field
serviced. The power draw of the motor is proportional to
the modulated gas input rate of the appliance.
DR 1200 - 5000
Figure 31: Fan, Burner, Hot Surface Igniter and Flame
Sensor Arrangement (DR 1200 – 5000)
Uses a sealed air fan to provide combustible air/gas mix to
the burner and push the products of combustion through
the heat exchanger and venting system. The fan assembly
consists of a sealed housing and fan wheel constructed
from spark resistant cast aluminum. The fan is operated
by a fully enclosed 230 VAC, 3 Phase electric motor. The
fan housing and motor assembly is fully sealed and
SHOULD NOT be field serviced. The power draw of the
motor is proportional to the modulated gas input rate of the
appliance.
7.4
INNER JACKET
The inner jacket assembly is constructed from a special
corrosion resistant stainless steel. All screws, bolts, nuts
and fasteners used for assembly
of the inner jacket are
also stainless steel.
DO NOT mix stainless steel and standard plated
fasteners when disassembling and reassembling the
inner jacket sheet metal components. Standard plated
fasteners will be damaged by the flue product
condensate
when
used
on
the
inner
jacket
assemblies.
7.5
OUTER JACKET
The outer jacket assembly is constructed from mirror finish
stainless steel. This ensures a long life for the jacket
assembly, with full integrity
7.6
VENTING TRANSITION
All appliances are shipped with a round stainless steel
adapter. Depending on the appliance category an
increaser will be required for the proper vent configuration.
Please refer to Table 3 dimensions and specifications.
When installing Category II or IV appliances care must be
taken to properly seal all joints and provide slope for
drainage of condensate away from the boiler.
Summary of Contents for DRH300
Page 2: ......
Page 6: ......
Page 38: ...32 13 Place toggle switch setting to REMOTE for remote operation if required...
Page 69: ...63 PART 12 EXPLODED VIEW 19 1 2 3 4 5 6 7 8 9 10 11 12 13 14 15 16 17 18 20...
Page 70: ...64 21 22 23 24 26 35 34 33 32 31 30 29 28 27 25 36 37 38 39 40 42 43 56...
Page 77: ...71 PART 13 ELECTRICAL DIAGRAMS...
Page 78: ...72...
Page 79: ...73...
Page 81: ...75...
Page 82: ...76...
Page 83: ...77...
Page 86: ......