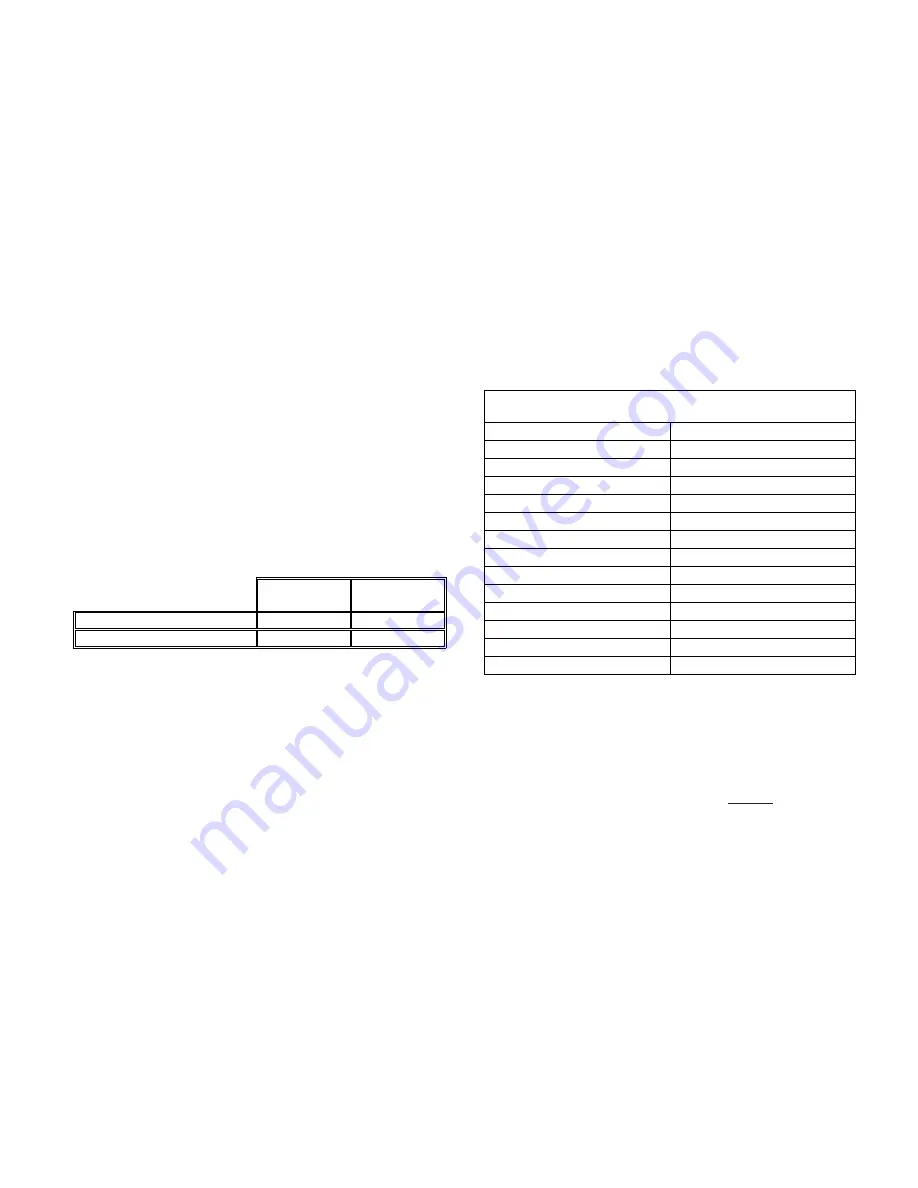
13
3.2 GAS
PIPING
All gas connections must be made with pipe joint
compound resistant to the action of liquefied petroleum and
natural gas. All piping must comply with local codes and
ordinances.
3.3
INSTALL PIPING
•
The gas line should sufficient to handle the total
installed capacity. Verify pipe size with your gas
supplier.
•
Use new, properly threaded black iron pipe free from
burrs. Avoid flexible gas connections. Internal diameter
of flexible gas lines may not provide appliance with
proper volume of gas.
•
Install a manual main gas shutoff valve at the
appliance gas inlet, outside of the appliance and before
the gas valve. Install a joint union at the appliance gas
line connection for ease of service and removal of the
gas train.
•
Run pipe to the Appliance gas inlet.
•
Install a sediment trap in the supply line to the
Appliance gas inlet.
•
Apply a moderate amount of good quality pipe
compound.
•
For LP gas, consult your LP gas supplier for expert
installation.
The appliance and its individual gas shut-off valve must be
disconnected from the supply piping when pressure testing
the gas supply piping at pressures above ½ PSI
Table 7 – Gas pressures at inlet to appliance
PROPANE
NATURAL
GAS
Minimum (inches W.C.)
11
3
Maximum (inches W.C.)
11
14
The gas supply line must be of adequate size to prevent
undue pressure drop and must never be smaller than the
size of the connection on the appliance. Sizing based on
Table 6 is recommended.
Before operating the appliance, the complete gas train and
all connections must be tested using soap solution.
Verify that the appliance is supplied with the type gas
specified on the rating plate. Heating values of local natural
gas are to be between 950 and 1010 Btu/ft
3
. Consult factory
if heating values are outside this range or if a gas with a
mixture of constituents is being used.
3.4
DIFFERENTIAL AIR PRESSURE
•
The Dynaflame operates on the principle of differential
pressures. Operation of the fan generates a signal
which is matched on the gas side by the 1 to 1 air/gas
ratio control valve.
•
The differential air pressure measurement is made
between the high and low pressure taps across the fan
discharge and the flue vent. All differential air
pressures are noted at full firing rate. There are two
pressure taps at the fan discharge and care must be
taken to tee into the correct line. The correct line may
be identified by tracing it back to the ratio control valve
where the identification of the tapping is stamped into
the die cast actuator.
•
The differential gas pressure measurement is made
between the high and low pressure taps across the in-
line metering gas orifice. Check this value to confirm
that it matches the differential air pressure while the
appliance is firing.
•
The controls on this appliance may fire the burner from
35% up to 100% for non-condensing and from 20% up
to 100 % for condensing of rated input.
•
Differential manifold gas pressure will be reduced as
burner input is reduced.
•
All reference gas pressure measurements must be
made at 100% of rated burner input.
•
The differential gas manifold pressure is pre-set at the
factory through the ratio gas valve. Adjustment of
manifold pressure is not normally required for proper
operation. In the field it may be necessary to adjust the
low fire adjustment screw located on the ratio control
valve actuator in order to achieve acceptable light off
under soft start field conditions.
Table 8
NOMINAL DIFFERENTIAL AIR PRESSURE SETTINGS
AT FULL FIRE (inches W.C.)
Model No.
Natural Gas & L. P. Gas
500 1.3
750 1.8
1100 2.6
1200 3.4
1500 2.7
1750 3.0
2000 3.7
2500 4.0
3000 4.8
3500 3.7
4000 5.0
4500 7.6
5000 9.5
3.5
GAS MANIFOLD DIFFERENTIAL
PRESSURE ADJUSTMENT
Tampering with gas valve adjustments after startup and
commissioning will void the warranty on the gas valve
assembly and the burner.
The appliance’s manifold gas pressure
IS NOT
field
adjustable after startup and commissioning. The gas valve
pressure ratios have been factory set with an internal bias
adjustment to ensure a 1:1 air/gas ratio on operation.
Tampering with this adjustment will void the warranty on the
gas valve assembly and the burner. An appliance supplied
with a properly sized gas line, properly sized meter and a
minimum gas supply pressure (See table 7 for minimum
allowable inlet gas supply pressure) while firing at full rate
will ensure full burner input. The manifold pressure supplied
to the burner is a differential pressure. This pressure is the
result of the difference in two gas pressure measurements.
A differential manifold gas pressure measurement should
not be made until you have measured the gas supply
pressure. Gas supply pressure must be at least at minimum
allowed with all appliances on the gas line firing at full rate
before a manifold pressure measurement is made. Use the
following procedure to check gas supply pressure with a
manometer connected to the inlet pressure tap on the gas
line connection at the rear of the appliance.
Summary of Contents for DFH500
Page 31: ...28 PART 9 TROUBLE SHOOTING ...
Page 32: ...29 ...
Page 39: ...36 PART 12 EXPLODED VIEW ...
Page 40: ...37 ...
Page 41: ...38 ...
Page 46: ...43 PART 13 ELECTRICAL DIAGRAMS ...
Page 47: ...44 ...
Page 48: ...45 ...
Page 49: ...46 ...
Page 50: ...47 ...
Page 51: ...48 ...