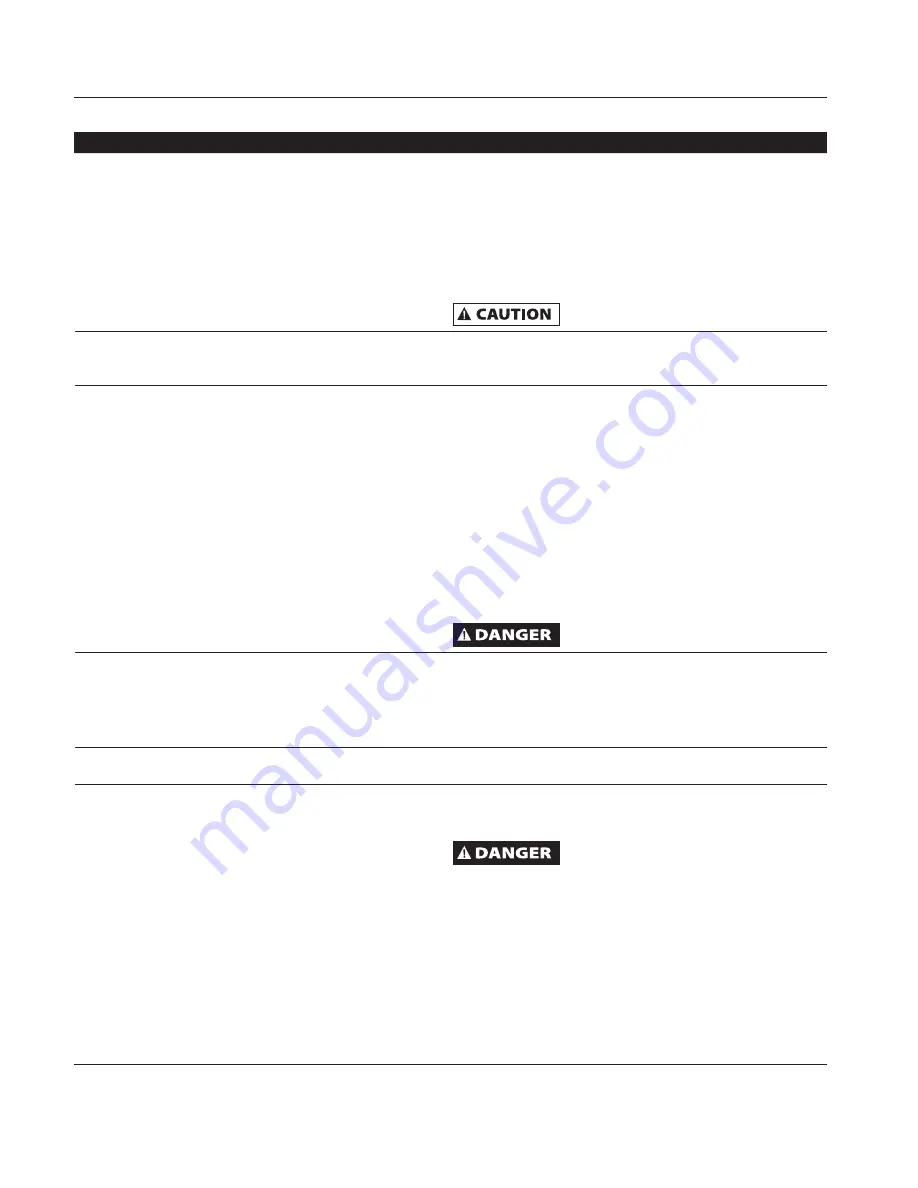
8
Operating Instructions
www.chpower.com
Troubleshooting Chart
Symptom
Possible Cause(s)
Corrective Action
Low discharge pressure
1. Air demand exceeds pump capacity
1. Reduce air demand or use a compressor with more capacity.
2. Air leaks
2. Listen for escaping air. Apply soap solution to all fittings and
connections. Bubbles will appear at points of leakage. Tighten or
replace leaking fittings or connections.
3. Restricted air intake
3. Clean the air filter element.
4. Blown gaskets
4. Replace any gaskets proven faulty on inspection.
5. Leaking or damaged valves
5. Remove head and inspect for valve breakage, misaligned valves,
damaged valve seats, etc. Replace defective parts and reassemble.
Install a new head gasket
each time the head is removed
Pump overheating causes
air filter to melt
1. Insulating gasket between filter and
head is missing
1. Install gasket.
2. Broken valves/blown gasket
2. Replace valves or install new gasket.
Excessive noise (knocking)
1. Loose motor or compressor pulley
1. Loose motor or compressor pulleys are a very common cause of
compressors knocking. Tighten pulley clamp bolts and set-screws.
2. Lack of oil in crankcase
2. Check for proper oil level; if low, check for possible damage to
bearings. Dirty oil can cause excessive wear.
3. Worn connecting rod
3. Replace connecting rod. Maintain oil level and change oil more
frequently.
4. Worn piston pin bores
4. Remove piston assemblies from the compressor and inspect for
excess wear. Replace excessively worn piston pin or pistons, as
required. Maintain oil level and change oil more frequently.
5. Piston hitting the valve plate
5. Remove the compressor head and valve plate and inspect for
carbon deposits or other foreign matter on top of piston. Replace
head and valve plate using new gasket. See Lubrication section for
recommended oil.
6. Noisy check valve in compressor
system
6. Replace.
Do not disassemble check
valve with air pressure in tank
Large quanity of oil in
the discharge air
NOTE:
In an oil lubricated
compressor there will
always be a small amount
of oil in the air stream.
1. Worn piston rings
1. Replace with new rings. Maintain oil level and change oil more
frequently.
2. Compressor air intake restricted
2. Clean filter. Check for other restrictions in the intake system.
3. Excessive oil in compressor
3. Drain down to full level.
4. Wrong oil viscosity
4. Use Mobil 1
®
10W-30.
Water in discharge air /
tank
Normal operation. The amount of
water increases with humid weather
1. Drain tank more often. At least daily.
2. Add a filter to reduce the amount of water in the air line.
Motor hums and runs
slowly or not at all
1. Use of extension cord
1. Do not use an extension cord. Use longer air hose with larger
diameter.
2. Malfunctioning check valve or
unloader valve
2. Replace check valve, unloader valve or pressure switch.
Do not disassemble check
valve with air pressure in tank
3. Low voltage
3. Check with voltmeter, check reset switch on motor. If reset switch
trips repeatedly, find and correct the cause. See next item.
4. Malfunctioning pressure switch -
contacts will not close
4. Repair or replace pressure switch.
Summary of Contents for Portable Air Compressor
Page 31: ...31 Notes Notas...