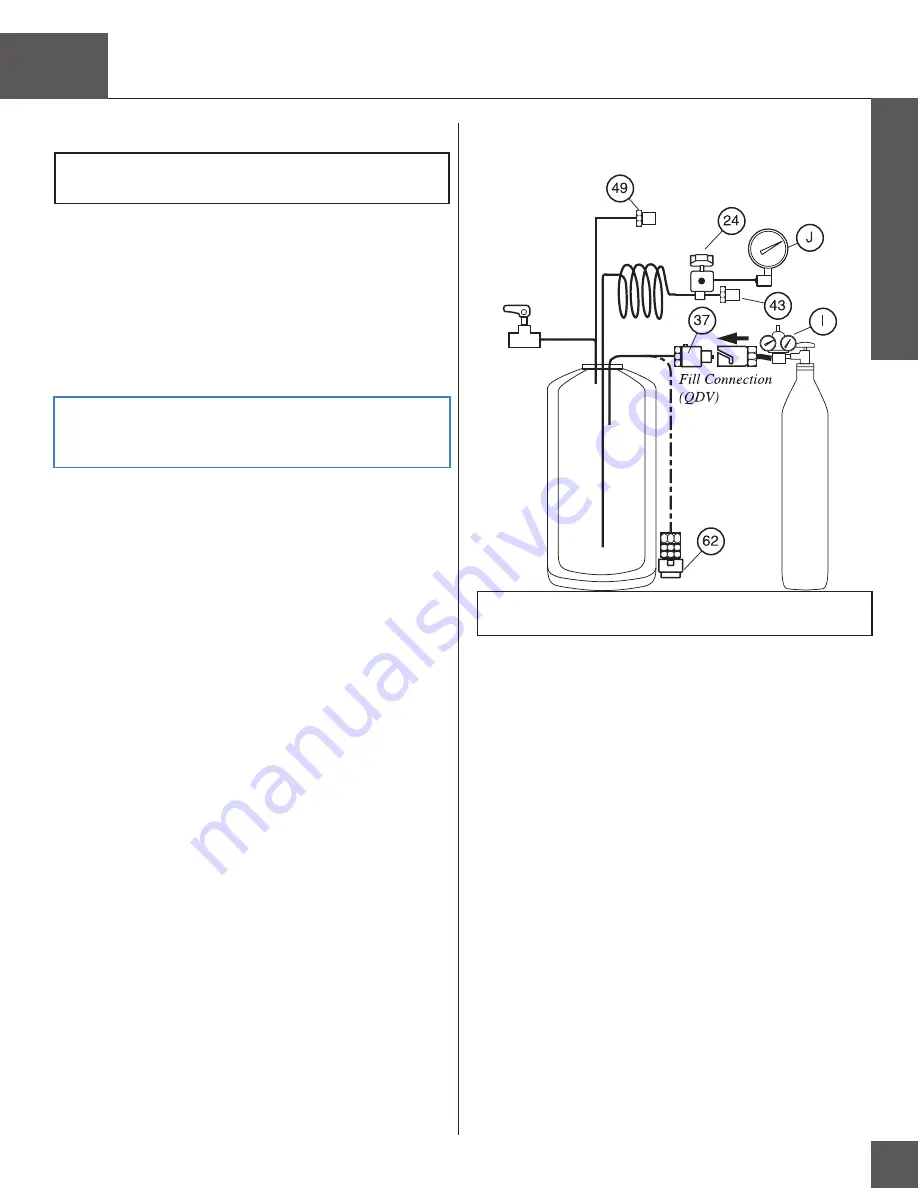
Hi Flow Stroller Technical Service Manual • PN 14314465 Rev
F
32
H
i F
lo
w S
tr
oller
Repair Procedures
X
RP27 – Case Cleaning
a. Clean using household glass cleaner or Simple Green D and
lint-free cloth. Do not get glass cleaner inside case or onto any
plumbing components. Simple Green D is available at www.
simplegreend.com
b. If necessary, a soft bristle brush can be used to help remove dirt
and debris. If desired, Caire, Inc. Technical Service can sup-
ply a specific list of additionale reccommended cleaning tools.
c. Allow unit to dry thoroughly before filling.
RP28 – Normal Evaporation Rate Test
a. Fill unit following procedure found in the Patient Operating
Instructions (POI).
b. Push button and check that all 8 LEDs are on, or verify that
the spring scale reads full.
c. Check for leaks in QDV and vent valve.
d. Let unit sit 16–18 hours.
e. Make sure FCV and vent valves are closed.
f. Do not move unit during this time.
g. If the Hi Flow is at least half full (4 LEDs), the unit passes.
Maximum loss rate prior to dewar servicing is 1.75 lbs./day
(0,8 kg/day).
NOTE: Clean case only after unit is empty and warm. Do not
clean in oxygen enriched atmosphere.
NOTE: Only use disinfectants or cleaning agents approved
for use with this equipment by CAIRE such as Sporicidin®,
HydroPure®, Hydroklean®, or others as specified by CAIRE.
RP2
9
–
Relief Valve Test
FIGURE
21
:
Relief Valve Test
WARNING:
The unit must be empty, warm and vented before
starting procedure.
a.
Remove case (RP4).
b.
Assemble pressure gauge (Item J) and adapter assembly.
Thread
hose barb onto pressure gauge. Push tubing onto hose
barb
and
attach with clamp.
c.
Assemble oxygen regulator, hose and pneumatic adapter.
Connect assembly to oxygen gas source. Connect pneumatic
adapter to unit QDV (Item 37
or 62
).
d.
Slowly begin increasing pressure to between 1,
35-1,4
8
bar/
19,7-2
1
,
5
psig. PRV (Item
49
) should begin venting
(audible noise will be heard or bubbling will be seen if leak
testing).
e.
Slowly begin decreasing the pressure until the PRV (Item
49)
closes, meaning the audible noise is no longer heard or the
bubbling is no longer seen if leak testing. The pressure at
which
the audible noise or bubbling is no longer seen should
be
greater than 1.
24
bar/
18
psig
.
f.
Hold PRV (Item 49) closed (with finger) and increase pres-sure
to 1,9-2,3 bar (27-33 psig). SRV (Item 43) must begin
open
(audible venting and/or bubbling of leak test solution).
g.
Slowly begin decreasing the pressure until the SRV
(Item 43)
closes, meaning the audible noise is no longer heard or the
bubbling is no longer seen if leak testing. The pressure at
which
the audible noise or bubbling is no longer seen should
be
greater than 1,
68
bar/2
4,3
psig
.
h.
Slowly begin decreasing the pressure
in order to release the
finger from the PRV.