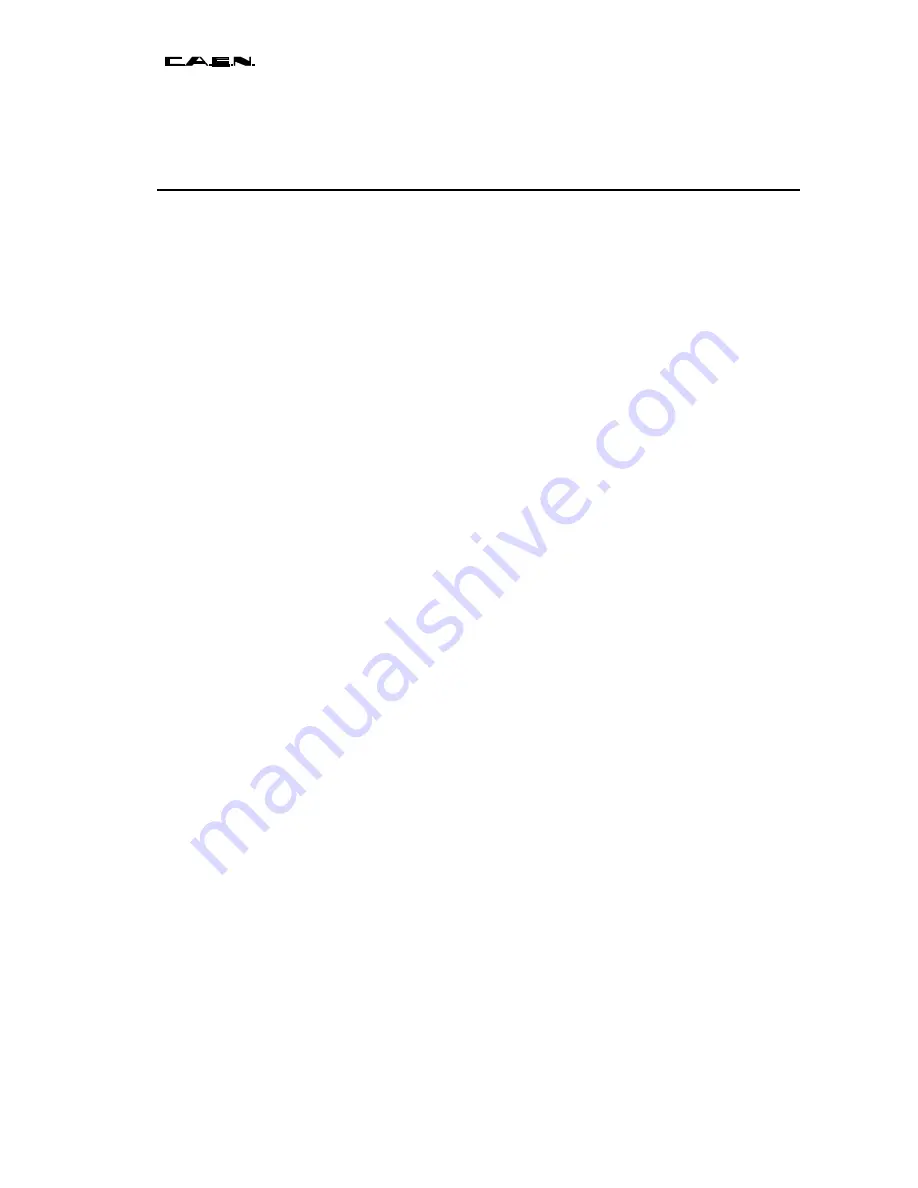
Document type:
Title:
Revision date:
Revision:
Installation Guide (MUT)
Mod. SY1527, universal multichannel power supply system
03/12/02
3
NPO:
Filename:
Number of pages:
Page:
00103/97:1527x.MUTx/03 HWGUIDE_REV3.DOC
62
11
via network facilities. Actually, Telnet and WWW access facilities allow system’s remote
debugging and technical support, including future firmware upgrading.
2.2
Short Functional description
A block diagram of the SY1527 system is shown in Fig. 2.2, p.13.
A single crate can host up to 16 Channel Boards, which can be chosen in a wide range
of plug-in boards, from standard HV/LV boards and floating boards to generic I/O boards
monitoring external parameters or branch controllers. All the types of boards can be
freely mixed in the same crate, fitting the user's needs.
Both the System’s Power-On and the Channel Out Enable can be performed either
locally or remotely. Remote Enable is performed by sending the proper input signal via
the relevant front panel connector.
Each crate may be controlled either locally or remotely. Local control is performed
manually through a key-pad, a compact switch and a 7.7" colour LCD located on the
front panel. Remote control is feasible via the interface connectors located on the front
panel. These include a RS232 interface, which can be used to plug in a video terminal
(ANSI VT100 or compatible) or a IBM
TM
PC, a VGA port to connect an external standard
VGA monitor and a PS/2 connector to plug in an external keyboard. The usual HIGH
SPEED (H.S.) CAENET interface is also available to daisy-chain more SY1527 crates
(up to 99 crates).
A sophisticated Software User Interface is available both in local or remote control,
featuring symbolic names for channels, custom status displays and other features
designed to help the management of a large number of channels.
Programmable parameters for each power channel include two voltage values (
V0set
,
V1set
) and two current limit values (
I0set
,
I1set
). The switching from one value to the
other is performed via two external (NIM or TTL) input levels (VSEL, ISEL). The
maximum rate of change of the voltage (Volt/second) may be programmed for each
channel. Two distinct values are available,
Ramp-Up
and
Ramp-Down
. Any command
to change the voltage will result in a linear voltage increase or decrease with time, the
rates being determined by the Ramp-Up or Ramp-Down parameters, respectively.
For the
boards with programmable current hardware protections
the ISET channels’
values represent a software-controlled hardware protection on the channels' currents. In
this case the channel cannot draw a current higher than its programmed limit.
For the
boards with fixed current hardware protections
, i.e. boards which have the
current hardware protection fixed to a common value for all the channels, the IMON
values are used to signal a fault, but the channels can draw a current larger than the
ISET values.
In both cases, if a channel tries to draw a current larger than the programmed limit, it is
signalled to be in OVERCURRENT. The System detects this state as a fault and reacts
according to the setting of the
TRIP
parameter, namely:
1) TRIP = infinite
(constant CURRENT mode)
If the Board has programmable current hardware protections, the output voltage is
varied to keep the current below the programmed limit. The channel acts like a
current generator.