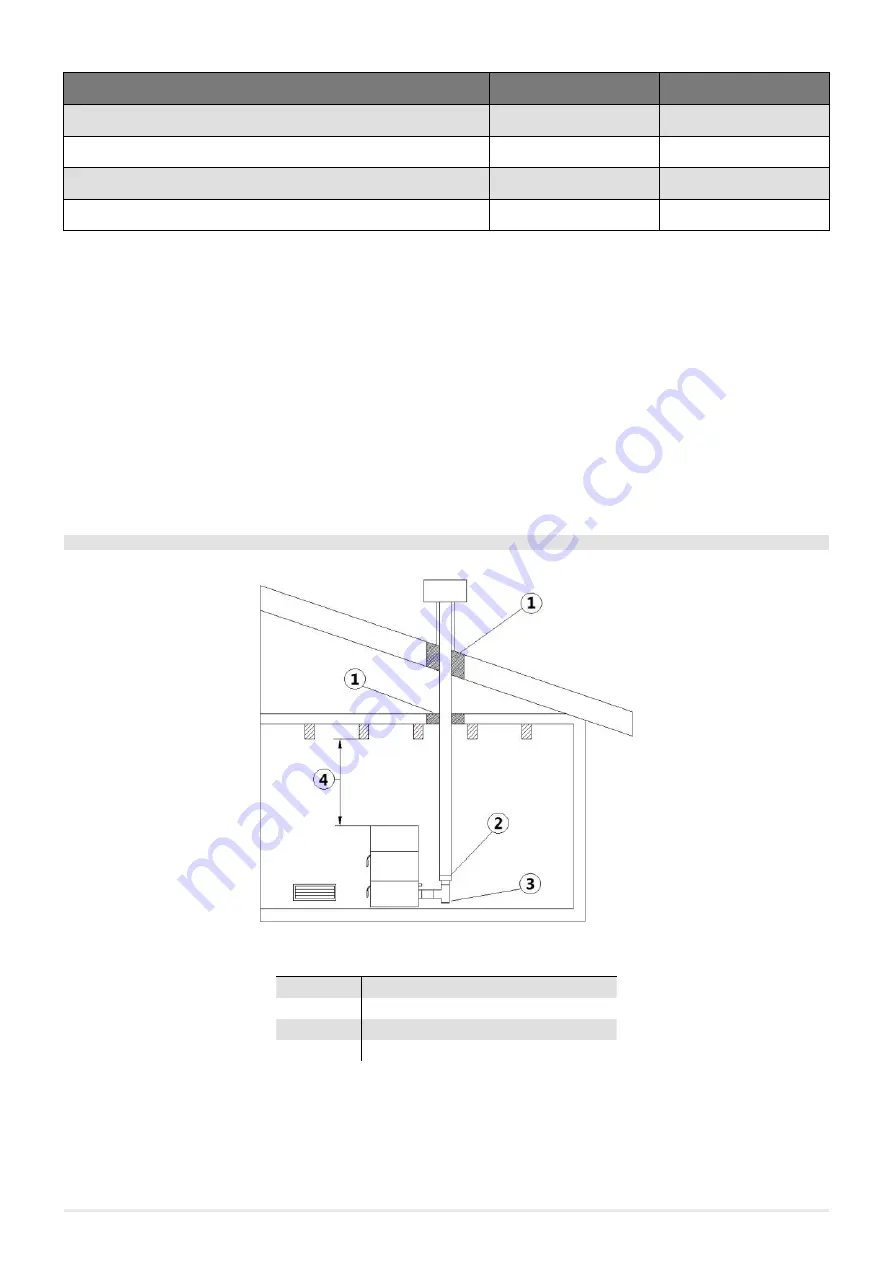
ZEFIRO
3
- ZEN AIRTIGHT
8
SYSTEM TYPE
Ø80 mm PIPE
Ø100 mm PIPE
Maximum length (with 3 unions)
4,5 mt
8 mt
Maximum number of unions
3
3
Level section (minimum inclination 3%)
2 mt
2 mt
Installation at a height above 1200 m a.s.l.
NO
Obligatory
• Use a plate pipe for stoves of Ø80 mm or Ø100 mm depending on the type of system and with silicone gaskets.
• It is forbidden to use metal, fibre cement or aluminium flexible pipes.
• For change of direction it is obligatory always to use a union (with angle > 90°) with inspection plug which enables an easy
periodic cleaning of the pipes.
• Please assure you that after the cleaning the inspection plugs are sealed with its efficient gasket.
• It is forbidden to exhaust flue gases directly from the wall towards the outside and closed spaces also at open top.
• The fume conduit must be placed at a distance of minimum 500 mm from flammable or heat-susceptible components.
• It is prohibited to connect more than one wood/pellet (*) or any other type of appliance (vent cowling...) to the same flue.
(*)
unless there are national derogations (for instance in Germany), which under suitable conditions allow for the installation of
several appliances in the same fireplace. In any case, strictly follow the product/installation requirements of the relative regulations/
legislation in force in that country.
3.9
EXAMPLES OF CORRECT INSTALLATION
Fig. 7 - Example 1
LEGEND
Fig. 7
1
Insulating material
2
Reduction from Ø100 to Ø80 mm
3
Inspection plug
4
Minimum safety distance = 0,5 mt
• Chimney flue installation Ø100/120 mm with an enlarged drilling for pipe transit.