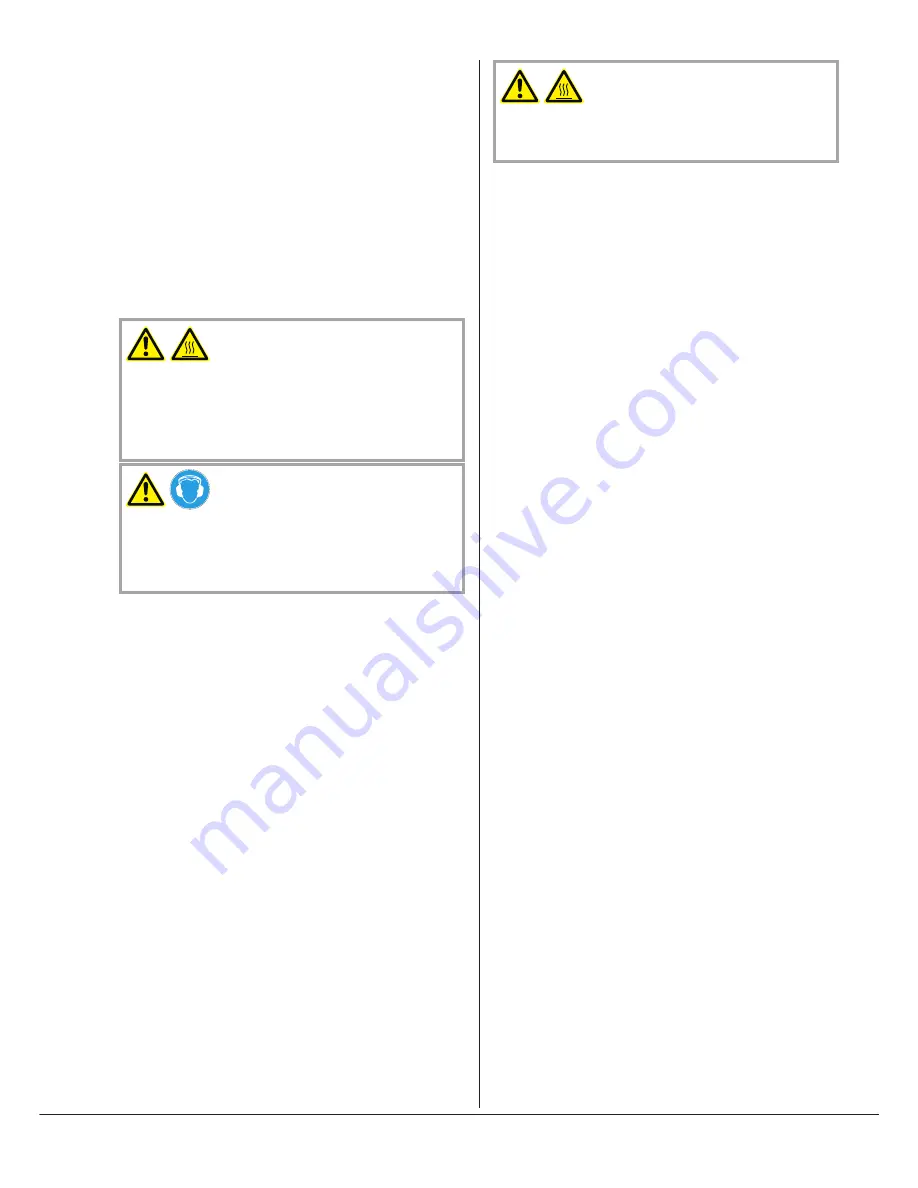
Make sure that the system is leak-tight and that there is no leakage of
dangerous substances.
If in doubt on drawn process-related liquids, we recommend the
installation of a separator.
Drawing substances with a higher density than air leads to an increased
thermal and mechanical load on the vacuum pump and is permissible
only after consultation with Busch.
Max. allowed temperature of the drawn gas:
See “Oil, Ambient temperature range”
Dispose of the used oil according to applicable environmental
protection regulations.
The vacuum pump is thermally suitable for continuous operation.
The vacuum pump is ultimate pressure-proof.
The pumping of other vapours must be previously approved by the
Busch Company.
CAUTION
During operation the surface of the vacuum pump may exceed
temperatures of 70°C.
Risk of burns!
The vacuum pump must be protected against contact during
operation, provide a guard if necessary
CAUTION
The vacuum pump emits sound of high intensity.
Risk of hearing damage.
Users spending a longer period of time in the vicinity of a
non-insulated vacuum pump must wear suitable hearing protection.
l
Make sure that the vacuum pump and the primary pump are
switched off and cannot accidentally be switched on again.
l
Make sure that protective devices will not be disconnected
l
Make sure that cooling air inlets and outlets are not covered or
obstructed and that the cooling air flow can circulate without
obstruction
l
Make sure that the “Installation Prerequisites” (see “Installation
Prerequisites and Commissioning”) are followed, particularly follow
those instructions that ensure sufficient cooling
Cooling water
To drain the cooling water, the hoses have to be removed and the
cooling water system blown through with compressed air, until all the
water has been completely removed.
Advice: When there is danger of frost, the cooling water must be fully
drained at a standstill of the pump, as described above.
Limitations of use
D
P = differential pressure between the outlet and the inlet of the
vacuum pump. See table “Technical Characteristics”. Do not exceed
the values given in the table.
Maintenance
For all maintenance work, the vacuum pump or the vacuum system
must be switched off and it must be ensured that it cannot accidentally
be switched on again.
Any dismantling of the pump must be executed by qualified personnel
only. Before dismantling, the end user of the vacuum pump must fill in
a “Certificate about Absence of Danger” which will inform about
possible risks and dangers and corresponding measures.
Without this document duly filled in and signed by an authorised
person, the pump cannot be dismantled.
CAUTION
During operation, the surface of the vacuum pump may exceed
temperatures of 70°C.
Risk of burns!
l
Prior to any work that requires touching the vacuum pump, let the
vacuum pump cool down
When draining the oil:
u
Let the vacuum pump cool down for no more than 20 minutes
l
Prior to disconnecting the inlet or discharge lines, make sure that
these pipes/ lines have been vented to atmospheric pressure
Maintenance Schedule
NOTE
: The maintenance intervals depend very much on the individual
operating conditions. The intervals given below must be considered as
starting values which should be shortened or extended as appropriate.
Particularly heavy duty operation, e.g. high dust loads in the
environment or in the process gases, other contaminations or ingress of
process material, can make it necessary to shorten the maintenance
intervals significantly.
Weekly
l
Check the oil level (see “Checking the oil”)
Monthly:
l
Make sure that the vacuum pump and the primary pump are
switched off and cannot be accidentally be switched on again
l
Check the vacuum pump for oil leaks - in case of leaks have the
vacuum pump repaired (Busch service)
In case of operation in a dusty environment:
u
Make sure that the working area is free from dust and dirt,
clean if necessary (see “Every 6 Months”)
l
Make sure that the oil level at the gears and bearings is in the
target circle of the oil sight glasses
Yearly:
l
Make sure that the oil level at the gears and bearings is in the
target circle of the oil sight glasses
Every 16000 Operating hours, at the latest after 4 years
l
Have a major overhaul done on the vacuum pump (Busch service)
Checking the oil
Checking the oil level at the gears and bearing
housings
l
Make sure that the vacuum pump and the primary pump are
switched off and cannot accidentally be switched on again
l
Read the level on the oil sight glasses (OSG, 220/ 222)
In case the level has dropped below the target circle:
u
Top up with oil (see “Topping up Oil”)
In case the level is above the target circle:
u
Change the oil (see “Change the oil”)
Maintenance
Page 9
Summary of Contents for WY 4500 C
Page 13: ...Exploded drawing Page 13 Exploded drawing ...
Page 20: ......
Page 22: ...Note ...
Page 23: ...Note ...