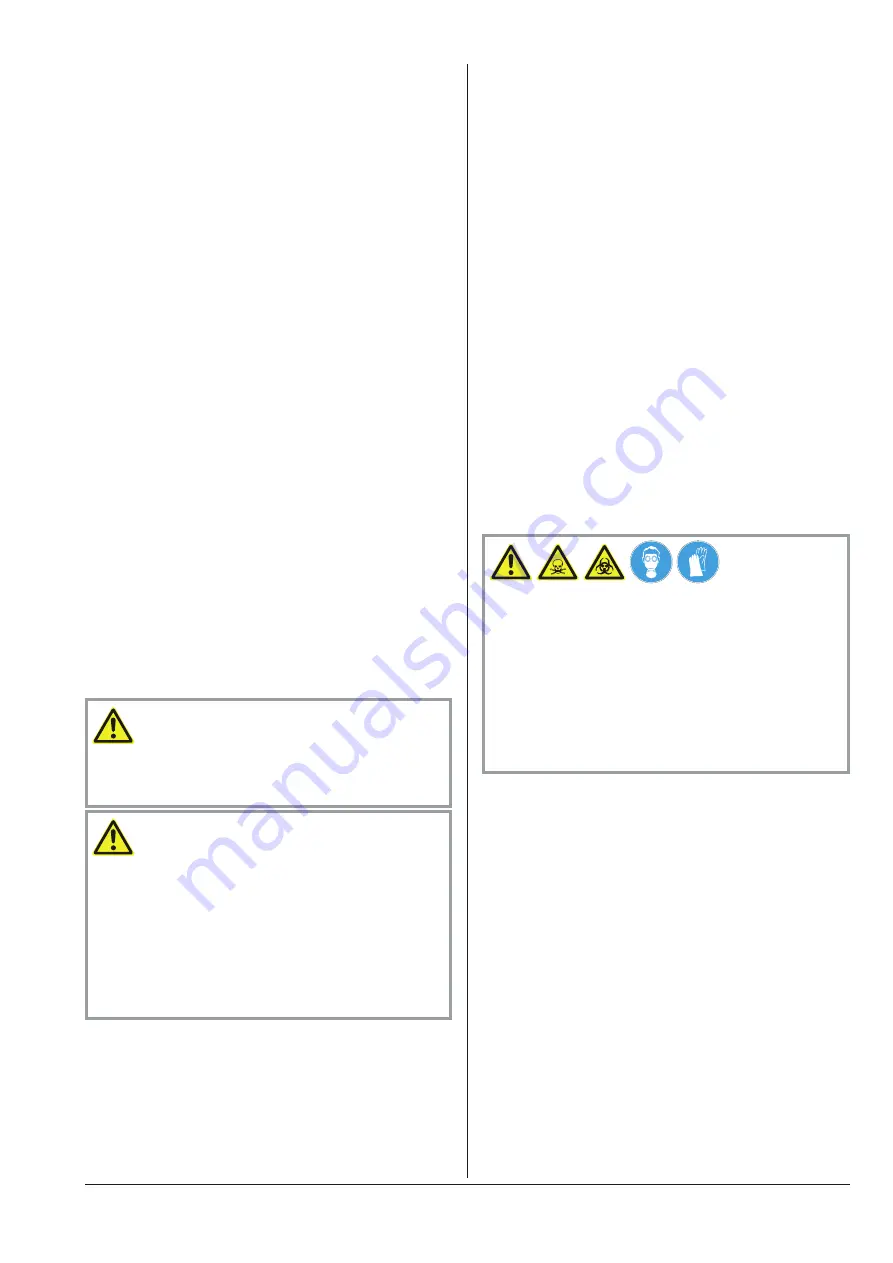
Replace the exhaust filter (
page 10: Exhaust Filter)
In case an inlet air filter is installed:
Replace the inlet air filter
Check the inlet screen, clean if necessary
Version with gas ballast with paper filter:
Replace the filter
Every 500 - 2000 Operating Hours:
(
page 9: Oil Life):
Change the oil (
page 9: Oil Change)
Checking the Oil
Checking the Level
Make sure that the vacuum pump is shut down and the oil has col-
lected at the bottom of the oil separator (f)
Read the level on the sight glass (g)
In case the level has dropped underneath the MIN-marking:
Top up oil (
page 9: Topping up Oil)
In case the level exceeds the MAX-marking:
Excessive dilution with condensates - change the oil and check
the process
If appropriate retrofit a gas ballast (Busch Service) and observe
the chapter Conveying Condensable Vapours (
page 8)
In case the level exceeds the MAX-marking despite proper use of the
gas ballast:
Replace the filter
Topping up Oil
Note
: Under normal conditions there should be no need to top up oil
during the recommended oil change intervals. A significant level drop
indicates a malfunction (
page 12: Troubleshooting).
Note
: During operation the exhaust filter gets saturated with oil. It is
therefore normal that the oil level will drop slightly after replacement
of the exhaust filter.
CAUTION
_a
Filling oil through the suction connection (c) will result in breakage
of the vanes and destruction of the vacuum pump.
Oil may be filled through the filling port (b) only.
CAUTION
_a
During operation the oil separator is filled with hot, pressurised oil
mist.
Risk of injury from hot oil mist with open filling port.
Risk of injury if a loosely inserted filling plug (b) is ejected.
Remove the filling plug (b) only if the vacuum pump is stopped.
The vacuum pump must only be operated with the filling plug (b)
firmly inserted.
Make sure that the vacuum pump is shut down and locked against
inadvertent start up
Remove the filling plug (b)
Top up oil until the level reaches the middle of the sight glass (g)
Make sure that the seal ring is inserted into the filling plug (b) and
undamaged, if necessary replace the filling plug (b)
Firmly reinsert the filling plug (b) together with the seal ring
Checking the Colour of the Oil
Note
: The oil should be light, either transparent, a little foamy or a little
tarnished. A milky discolouration that does not vanish after sedation of
the oil indicates contamination with foreign material. Oil that is either
contaminated with foreign material or burnt must be changed
(
page 9: Oil Change).
In case the oil appears to be contaminated with water or other conden-
sates despite proper use of the gas ballast:
Replace the filter
Oil Life
The oil life depends very much on the operating conditions. A clean
and dry air stream and operating temperatures below 100 °C are ideal.
Under these conditions the oil shall be changed every 500 to 2000 op-
erating hours or after half a year.
Under very unfavourable operating conditions the oil life can be less
than 500 operating hours. Extremely short life times indicate malfunc-
tions (
page 12: Troubleshooting) or unsuitable operating conditions,
though.
Chosing a synthetic oil instead of a mineral oil can extend the oil life.
To select the oil best suited oil for your process please contact your
Busch representative.
If there is no experience available with regard to the oil life under the
prevailing operation conditions, it is recommended to have an oil anal-
ysis carried out every 500 operating hours and establish the change in-
terval accordingly.
Oil Change
DANGER
_age32
In case the vacuum pump conveyed gas that was contaminated
with harmful foreign material the oil will be contaminated with
harmful material.
Danger to health during the changing of contaminated oil.
Danger to the environment.
Personal protective equipment must be worn during the changing
of contaminated oil.
Contaminated oil is special waste and must be disposed of sepa-
rately in compliance with applicable regulations.
Draining Used Oil
Note
: After switching off the vacuum pump at normal operating tem-
perature wait no more than 20 minutes before the oil is drained (the oil
shall still be warm when being drained).
Make sure that the vacuum pump is shut down and locked against
inadvertent start up
Make sure that the vacuum pump is vented to atmospheric pres-
sure
Put a drain tray underneath the sight glass (g)
Remove the sight glass (g) and drain the oil
When the oil stream dwindles:
Reinsert the sight glass (g)
Switch the vacuum pump on for a few seconds
Make sure that the vacuum pump is shut down and locked against
inadvertent start up
Remove the sight glass (g) again and drain the remaining oil
Make sure that the seal ring is inserted into the sight glass (g) and
undamaged, replace if necessary
Firmly reinsert the sight glass (g) together with the seal ring
Dispose of the used oil in compliance with applicable regulations
RB/RC 0006 C/E
Maintenance
0870152229
page 9
Summary of Contents for R5 RB 0006 C
Page 20: ......