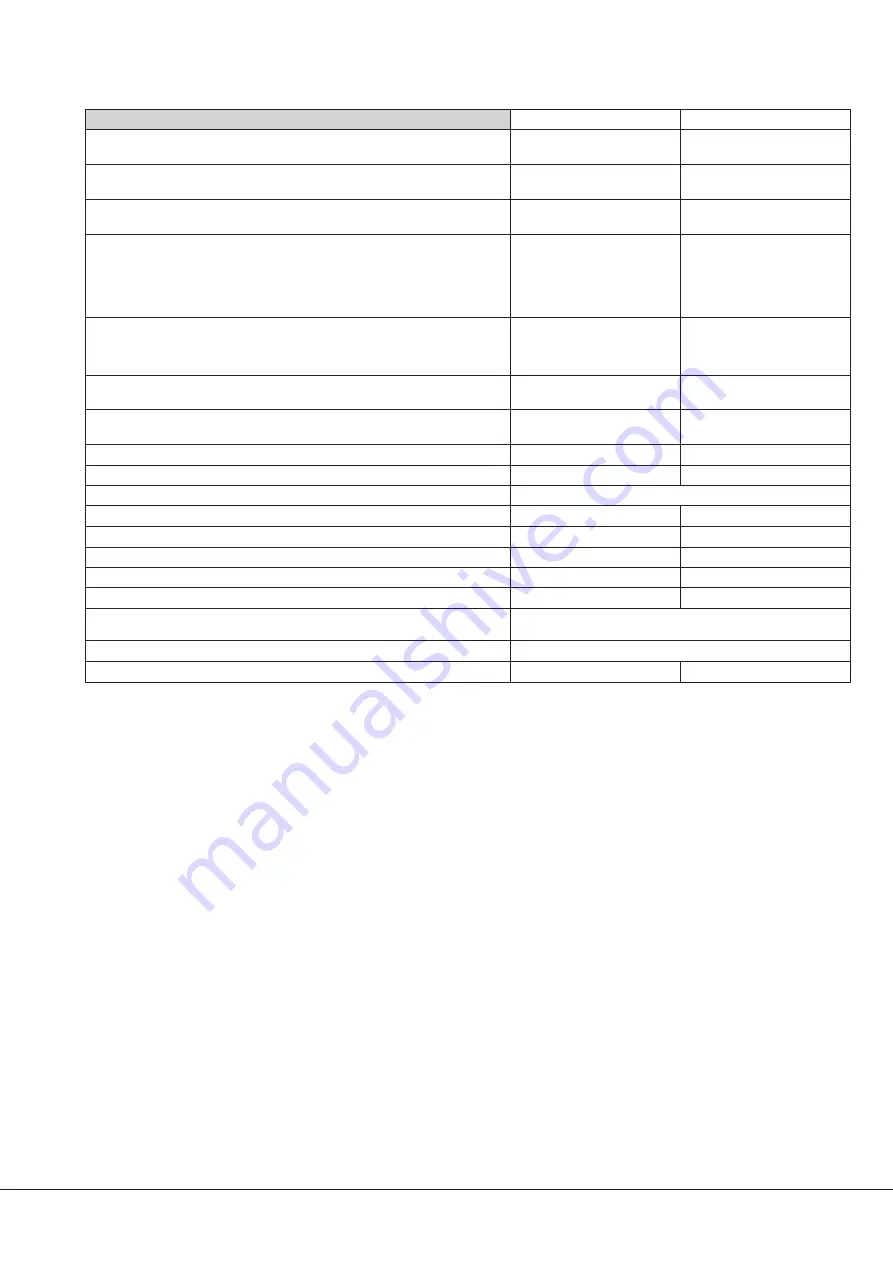
Technical Data
Technical data
NS 0070 C
NS 0160 C
Nominal suction capacity
50 Hz
60 Hz
m
3
/h (cfm)
m
3
/h (cfm)
70 (41)
85 (50)
135 (79)
160 (94)
Ultimate pressure
Torr
mbar
2,2 x 10
-2
3,0 x 10
-2
2,2 x 10
-2
3,0 x 10
-2
Nominal motor rating
50 Hz
60 Hz
kW
kW
4,0
4,4
5,5
6,6
Motor voltage and
current rating
50 Hz
D
200 V
D
230 V
D
255 V
Y 346 V
Y 400 V
Y 440 V
A
A
A
A
A
A
15.9
16.6
20
9.2
9.5
11.7
21
20.5
25
12.2
11.7
14.3
Motor voltage and
current rating
60 Hz
D
200 V
D
277 V
Y 346 V
Y 480 V
A
A
A
A
17.2
15.8
9.9
9.1
27
21
15.4
12.0
Nominal motor speed
50 Hz
60 Hz
min
-1
min
-1
3000
3600
3000
3600
Noise level (EN ISO 2151)
50 Hz
60 Hz
dB(A)
dB(A)
62
68
Ambient temperature
°C (°F)
0-40 (32-104)
0-40 (32-104)
Maximal counter pressure
Discharge
bar
0,2
0,2
Maximum inlet pressure
Atmospheric pressure
Cooling water temperature
°C (°F)
10 - 30 (50 - 86)
10 - 30 (50 - 86)
Cooling water requirement
l/ min
³
3
³
3
Cooling water pressure
bar
3 -6
3 -6
Nitrogen requirement
approx.
slm
0 - 18
0 - 18
Nitrogen overpressure
bar
1,5
1,5
Maximal allowed
operationnal speed
Refer to nameplate
Leakrate
mbar x l/s
£
1 x 10
-6
Weight
approx.
kg
250
250
NS 0070-0160 C
Technical Data
0870570353 (En)
Page 21
Summary of Contents for COBRA NS 0070-0160 C
Page 23: ...Note...