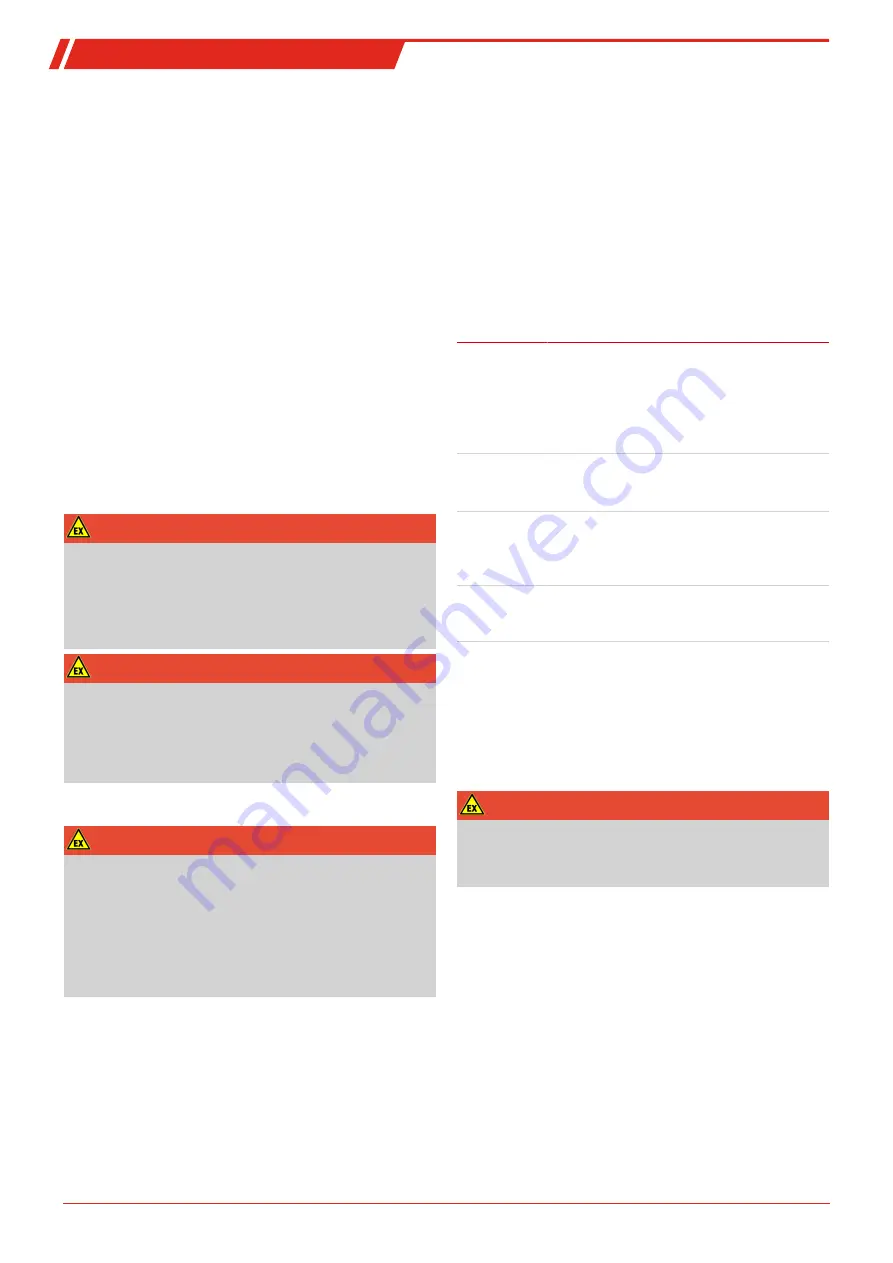
AGF-VA-23, K-AGF-VA-23
• Maintenance and cleaning instructions must be followed.
• When used with moist gasses, a condensate separator
must be installed. Moist gasses can clog pores in the filter.
Gas pressure building up can result in an impermissible
temperature rise.
• Observe the grade of filtration of the fine mesh filter and
if necessary install a pre-filtration to ensure larger solid
particles do not clog the filter prematurely.
• Observe the durability list in this document. Only use me-
dia compatible with the filter materials.
• Do not repair the filter. Damaged filter components must
be replaced.
• Do not paint, laminate or otherwise coat the filters.
• Observe the applicable constructor regulations, e.g. EN
60079-14, for installation and mounting.
• All metallic parts of the filter must be connected to an
earth potential. The resistance of a continuity test must
not exceed 1 MΩ (1*10
6
Ω).
• The sealing materials, e.g. Teflon tape, must be conduct-
ive so all parts of the filter are earthed. If necessary, install
an earth bridge.
Operation and Control
DANGER
Risk of explosive gasses leaking and crossing zones
Check the filter is tight prior to operation.
Inadequately sealed filters can leak. Gas may leak or the am-
bient atmosphere be drawn in. Use a suitable method for the
leakage test, appropriate for the application.
DANGER
Explosion hazard due to isolated metal parts
Never operate the filter without the pressure spring in the
base. If lost, the filter must be taken out of service. Operation
without the pressure spring poses an explosion hazard and
considered improper use.
Operation with moisture detector
DANGER
Explosion hazard
To operate the filter in an explosive atmosphere with mois-
ture detector, the moisture detector and controller must be
ignition protection class intrinsically safe “i”. The use of non-
intrinsically safe components may result in ignition in explos-
ive atmospheres.
Also note the specifications under EN 60079-14 in this respect.
Service
Please note the following instructions. Failure to do so may
result in explosive gasses escaping and crossing zones.
• Check the filter is tight after any maintenance and the in-
tervals specified in the maintenance schedule. Inad-
equately sealed filters can leak. Gas may leak or the ambi-
ent atmosphere be drawn in. Use a suitable method for
the leakage test, appropriate for the application.
• There must be no internal or external Ex atmosphere
when performing maintenance. If necessary, flush the fil-
ter with inert gas. Switch off pumps on the gas circuit and
close supply and discharge lines.
• After performing any maintenance, before closing the fil-
ter be sure the pressure spring is installed inside the filter
if previously removed, or is seated correctly.
Service schedule
When using the filters in ATEX areas, follow this maintenance
schedule:
Component
Interval in operating
hours
Work to be performed
Filter element Weekly, and depend-
ing on the contamina-
tion level of the filter
element.
• Visually inspect for
contamination.
• If contaminated,
replace the filter
element and O-
ring.
O-ring
Every time the filter
cover is removed.
• Clean O-ring con-
tact surfaces.
• Replace O-ring.
Entire filter
Weekly and depend-
ing on the external
level of contamina-
tion.
• Remove layers of
dust with a damp
cloth.
Entire filter
Every 6 months and
every time the filter is
opened.
• Perform a leak test.
When replacing the filter element, the seal must also be re-
placed.
Cleaning
Dust deposits on the filter must be removed regularly.
Clean the outside of the filter using only a clean, damp cloth
(do not use cleaners containing solvents).
DANGER
Spark formation due to electrostatic discharge (explo-
sion hazard)
Only clean the filter with a clean, damp cloth.
4 Transport and storage
Only transport the product inside the original packaging or a
suitable alternative.
The equipment must be protected from moisture and heat
when not in use. They must be stored in a covered, dry and
dust-free room at a temperature between -20 °C to 50 °C (-4 °F
to 122 °F).
6
Bühler Technologies GmbH
BX410012 ◦ 10/2021