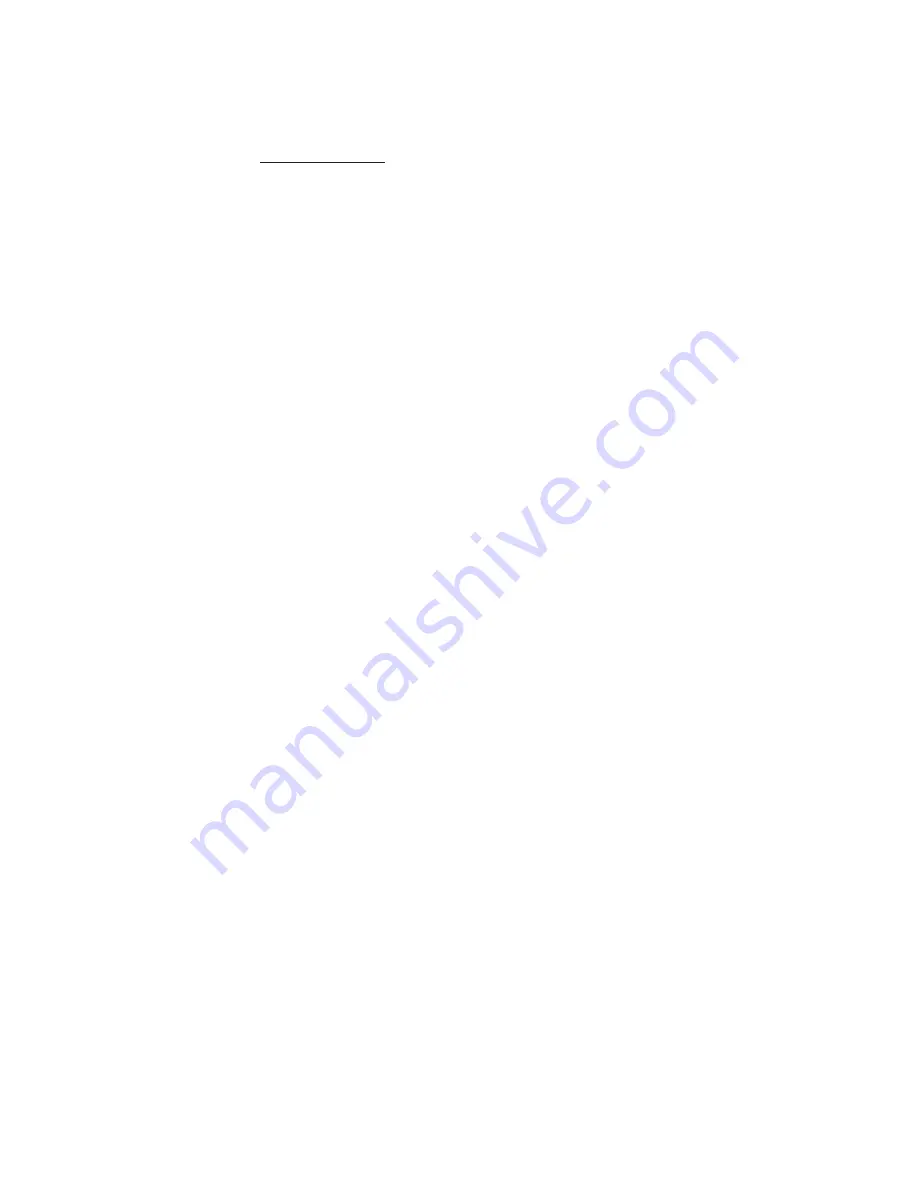
15
Test all the switches on the master control panel and monitor the LEDs.
NOTE: The BGW master control is powered by 220V/1ph VAC, please check for first time operation.
CAUTION: After switching off the inverter, please wait for at least 3 minutes before switching it on again.
Quick repetitions to switch the inverter on and off could damage the inverter due to the residual volt-
age. Please refer to the inverter manual for details.
Check the flux vacuum is properly powered by the toggle switch at the master control, make sure enough flux is
filled to the flux separator and the correct flux valves of the flux feed / recovery hoses are open.
Test the switches on the wire feeding control (eg. Lincoln NA3) make sure there is wire feed to the nozzle.
As soon as the inverter is powered up, the speed display should indicate the speed preset by the users. User can
test run the BGW at the preset speed and full speed.
NOTE: When the inverter is off, the display should indicate “000” when the frame is not moving.
WELDING
Choose the weld direction by setting the travel switch to left or right, adjust the weld speed according to the
welding procedure. Set NA-3 travel switch to” hand” so the frame would travel without welding.
Set to correct CV-VV switch position inside the NA Control. Preset appropriate welding voltage / current at the NA-
3 control, then switch NA-3 to “Auto”.
Release the flux valve to allow sufficient amount of flux to drop on the arc start area and cover the wire stick out.
NOTE: For models with electric flux valve option, the flux would feed automatically when the wire touches the work
when the operator presses “inch down” to feed wire prior welding.
Press “start” pushbutton of the NA3 and the start the weld sequence (wire slowly feeds to the work, the arc
strikes and weld travel begins).
During welding, operator should closely observe if the welding arc is tracking the weld joint, use the laser pointer
as the position indicator and finely adjust the torch position via the manual cross slide if necessary.
When the welding operation is complete, simply press the “STOP” bottom at the NA3 control panel and the BGW
frame would stop traveling with the termination of the welding arc.
NOTE:
* For safety reasons, please power off the system before disconnecting any of the control cables to the
master control.
* In order to increase the consumed life of the flux belt mechanism, user is recommended to extend the support
guide wheels as the mean of support when the BGW is not welding (flux belt must be firmly in contact with the
shell plate during welding operation for flux recovery).
* Excessive suction force would prohibit flux feeding during the welding operation, adjust the vacuum hose
valve if necessary.
If the machine is going to weld in the direction opposite of what it was previously set up for, simply shut down the
manual hose valve at one side and open the hose valve at the other side.