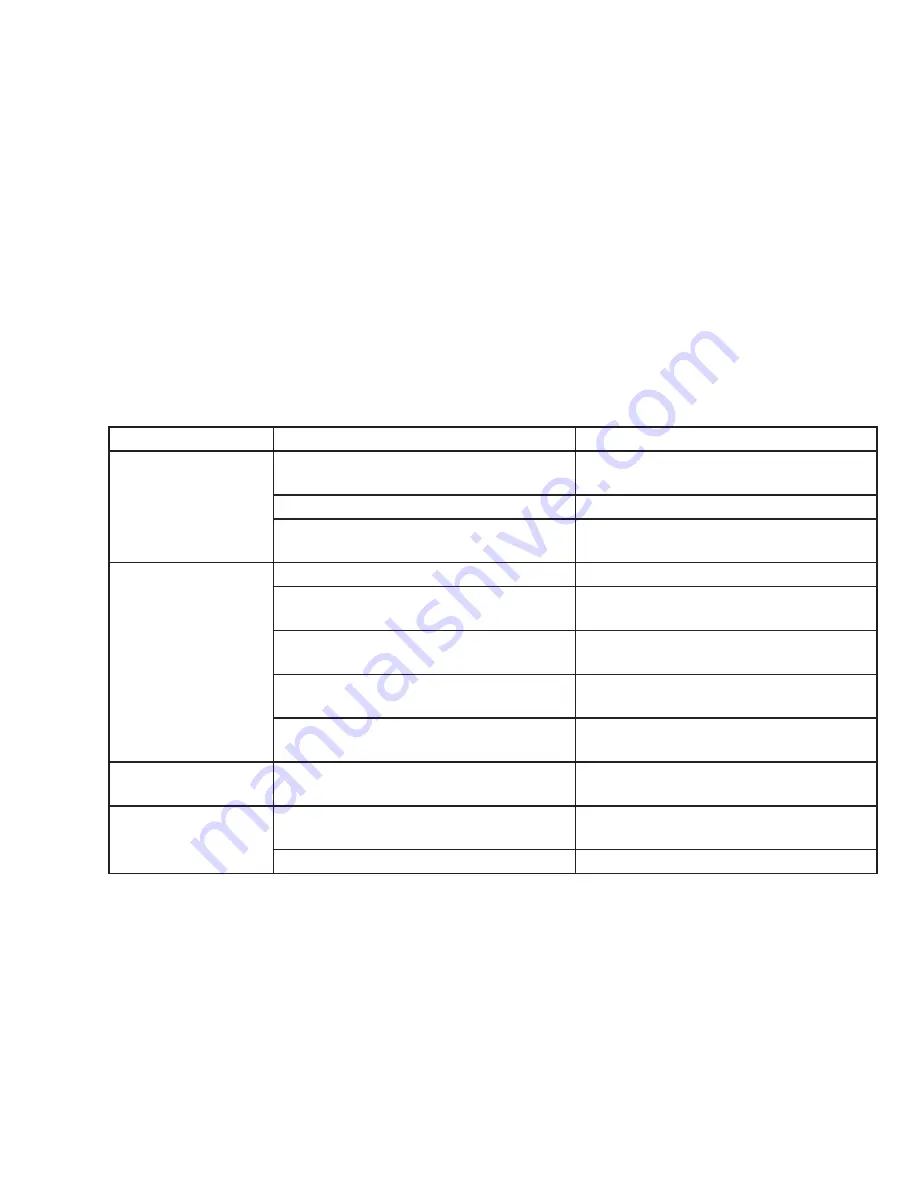
9
MAINTENANCE
The weaver unit should be periodically checked and cleaned to maximize service life.
Before use:
Check all screws in the torch clamp. Tighten as needed. Loose fasteners may cause inconsistent
weld quality.
During use:
Monitor motor and welding torch for abnormal noise or overheating.
After each use:
1. Clean control panel to remove dust and other debris.
2. Inspect slide adjustment and torch for weld spatter or other debris. Clean as needed.
3. Inspect power cable and torch cable for cracked, cut or damaged insulation. Replace as needed.
4. Inspect connectors for damaged pins or loose connections. Replace as needed.
TROUBLESHOOTING
Symptom
Cause
Repair
Control Pendant
Display is not LIT
Disconnected Power Cable
Verify power cable is properly
connected to machine.
Faulty Power Cable
Replace cable.
Control Pendant Fuse Tripped or
Disconnected
Replace fuse. If problem persists,
contact service rep.
No Arc when Start
button is pressed
Weld Contact switch set to OFF
Turn Weld Contact switch to AUTO.
Loose contact of Welding Leads
Check ground connections. Verify good
contact on clean, unpainted surface.
Bad or incorrectly wired Weld Contact
switch
Check Wiring. Replace switch, if
needed.
Weld Contact Cable is bad or
improperly connected
Verify cable is correctly connected.
Replace cable if bad.
Weld Power Source turned OFF
Turn ON Weld Power Source
Torch targets wrong
position
Loose fastener on Torch Clamp
Check and tighten screws, replace if
needed.
Arc continues after
Stop button is
pressed
Crater Fill timer has not timed out.
Check timer settings and adjust if
needed.
Faulty or incorrectly wired Stop button
Check Wiring. Repair as needed.