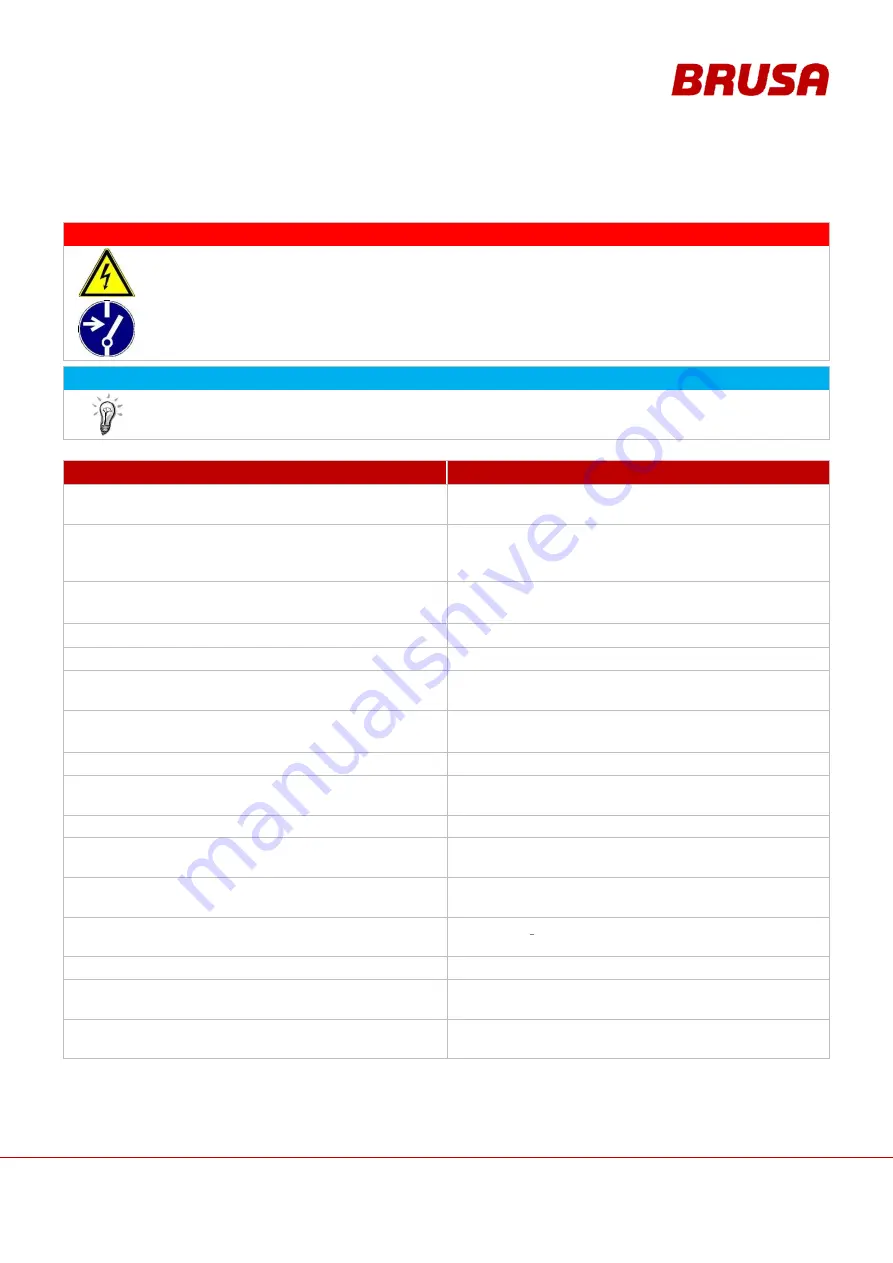
53
Technical data
and startup
9
Start-up
DANGER
High voltage!
Danger to life!
While connecting the HV wiring, fatal injuries can occur if the HV wiring is live!
So check that the HV battery is not live before start-up!
INFORMATION
In this chapter, you will be lead step-by-step through each stage of the start-up. The given procedure
must absolutely be adhered to!
PROCEDURE STEP
ILLUSTRATION / OTHER INFORMATION
1.
Have the necessary additional documentation and
the required additional equipment ready.
see chapter
4.2 Scope of the entire documentation
2.
Install the provided software.
This step is only necessary if the inverter is
not
integrated into a customer-provided CAN network
and/or
no
customer specific software is used for this.
3.
Integrate the device mechanically into the specified
position.
Use the screws and torques stated,
see chapter
6.6.2 Fixing (as in example DMC524)
4.
Ensure that the HV battery is not active.
---
5.
Build the interlock circuit and check the functioning.
see chapt.
8.3.8 Pin 19 IL1, Pin 20 IL2 (Interlock 1 + 2)
6.
If it is not already done, build all the connections at
the inverter.
see chapter
7.
Close the
service cap
.
see chapter
The interlock switch is activated.
8.
Ventilate and check the cooling system.
see chapter
9.2 Ventilate and check cooling system
9.
Connect the motor with inverter over the motor
sensor cable.
---
10.
Build the 12V supply.
---
11.
Establish communication between the
and the inverter.
see manual
Param operation.pdf
12.
Parameters can now be set for the inverter with the
applied software
(e.g.
PARAM_Tool
from BRUSA).
see manual
Param operation.pdf
13.
If it is not already done, load the motor parameter
table onto the inverter.
see chapter
9.3 Load motor parameter table onto
14.
Build the HV supply.
see chapter
15.
If it has not already been done, carry out rotor offset
adjustment.
DMC5_RotorOffest_adjustment.pdf
16.
The inverter is now ready for operation and can be
operated though CVI.
see chapter