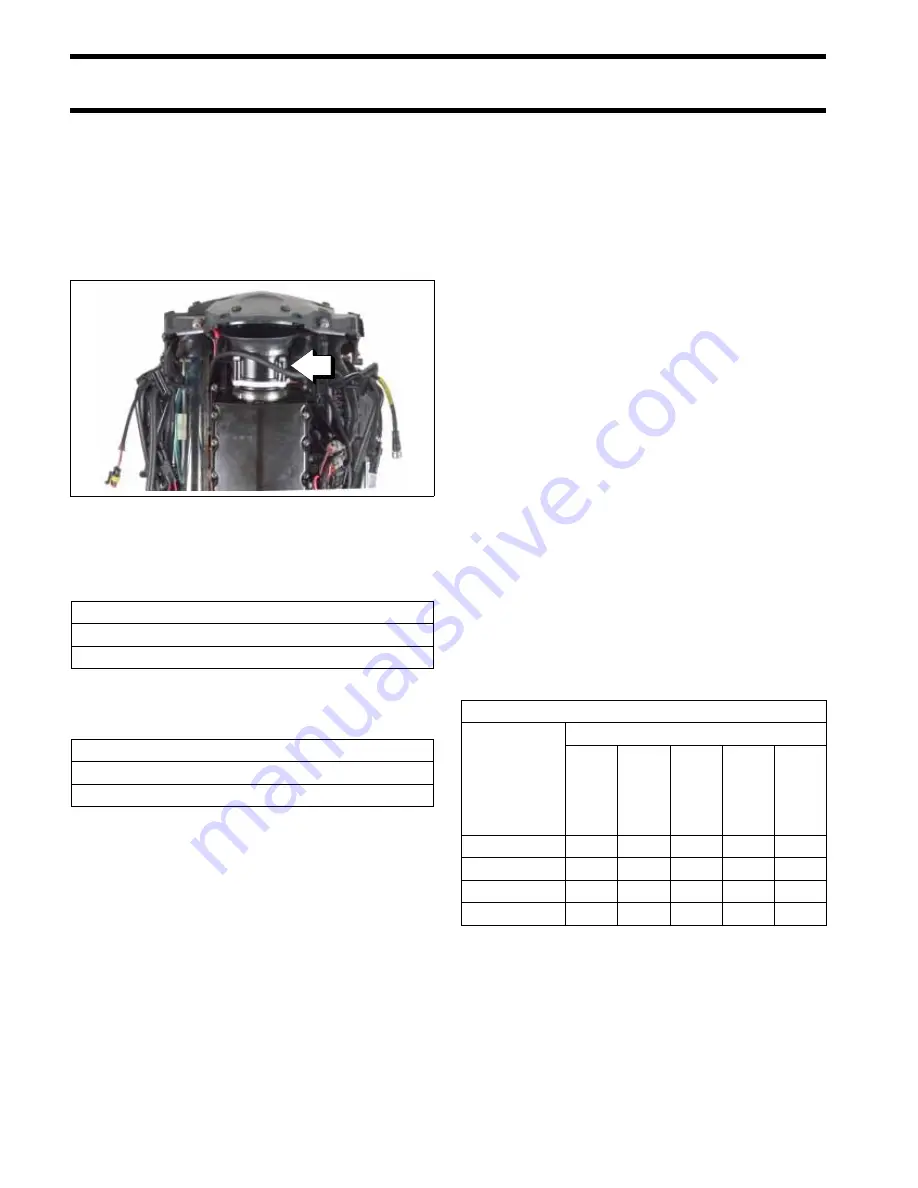
Evinrude ICON II Remote Control System
System Settings and Diagnostics
226
Throttle Valve Assembly
The electronic throttle body assembly converts
electronic signals sent from the Electronic Throttle
Controller (ETC) in the
EMM
into the mechanical
motion required to move the throttle plate.
Also see
Electronic Throttle Controller
If the ETC
cannot communicate with the electronic
throttle body for more than 250 milliseconds, the
EMM
:
If the throttle plate cannot achieve the com-
manded position, the
EMM
:
System Settings
and Diagnostics
Use
Evinrude Diagnostic
software, v 6.1 or higher
to communicate with the remote control. Refer to
Diagnostic software can change configuration set-
tings, view identification information and stored
faults, monitor control functions or update soft-
ware.
Multiple Engine Instancing
Multiple outboard installations require the transom
position of each outboard be identified.
Engine identity is set and stored in the
EMM
of
each outboard. By default the
EMM
of all out-
boards is set to instance zero (0) at the factory.
Outboards are identified as Instance 0 through 3,
from port to starboard, up to four outboards.
Engine identity of each outboard must be set
manually or with
Evinrude Diagnostics
software
v 6.1 or higher. Use the following chart to assign
the engine instance number to the outboard’s
position on the transom.
If duplicate engine identity numbers are detected,
the affected outboard’s NEUTRAL indicator LED
will flash rapidly.
1.
Throttle valve assembly
009173
Activates
S.A.F.E.
Stores
EMM
fault code 162
Engine Monitor: CHECK ENGINE display ON
Activates
S.A.F.E.
Stores
EMM
fault code 179
Engine Monitor: CHECK ENGINE display ON
1
Identity Numbers Chart
Number of
Outboards
Transom Position
Port
Port
Center
Center
St
arb
o
ar
d
Center
St
arb
o
ar
d
1
0
2
0
1
3
0
1
2
4
0
1
2
3
Summary of Contents for E 250 L HO AG B
Page 271: ...Powerhead Powerhead Views 271 11 Powerhead Views Starboard 009375...
Page 272: ...272 Powerhead Powerhead Views Port Non DPS Models 009406...
Page 273: ...Powerhead Powerhead Views 273 11 Port DPS Models 009374...
Page 274: ...274 Powerhead Powerhead Views Rear 200 225 250 HP Models 009407...
Page 275: ...Powerhead Powerhead Views 275 11 Rear 250 H O 300 HP Models 009376...
Page 276: ...276 Powerhead Powerhead Views Front Frame Removed 009379...
Page 277: ...Powerhead Powerhead Views 277 11 Front Frame Installed 009378...
Page 416: ...S 416...