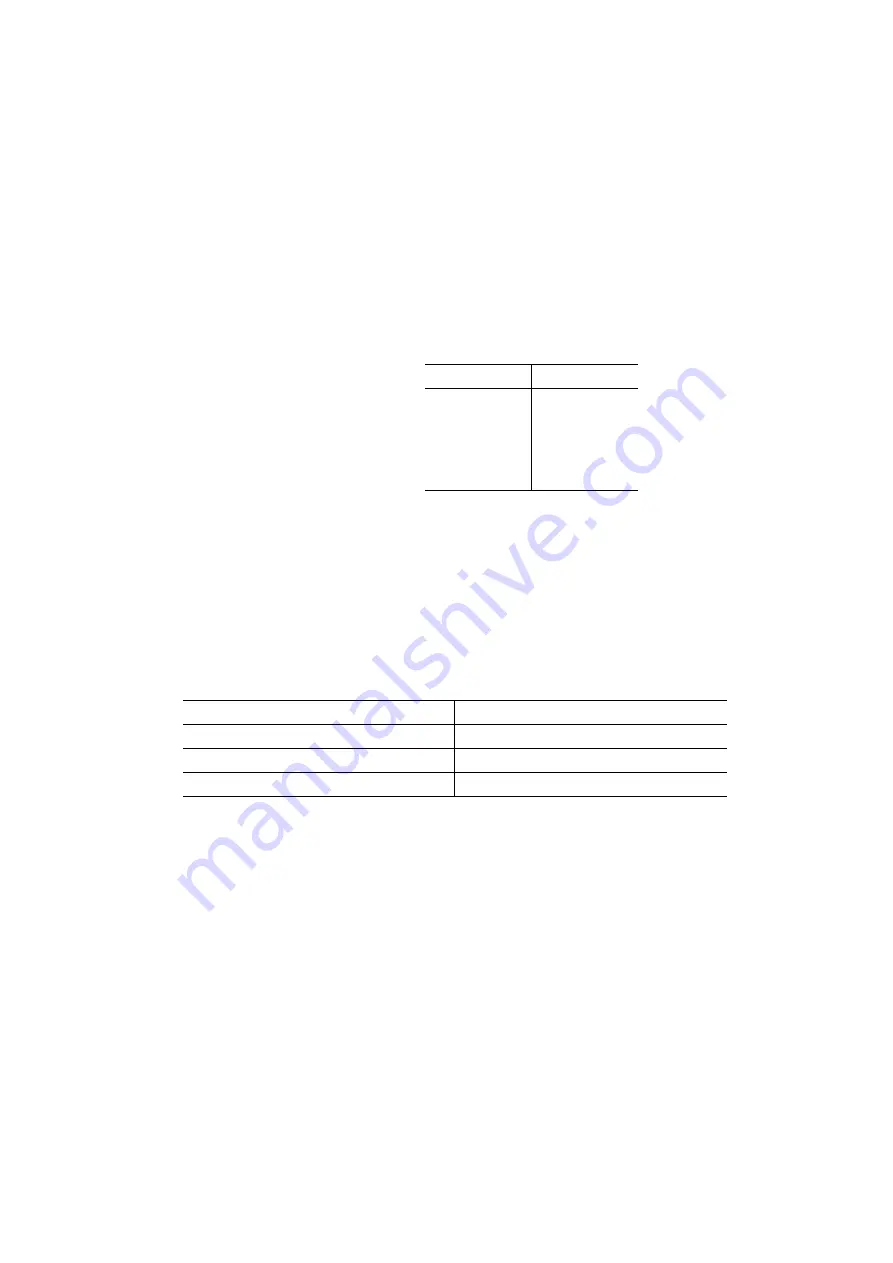
I - 2
1.1.4 Printing Mechanism
(1) Print system
Thermal transfer onto plastic and fabric tapes
(Fixed thermal print head and tape feed mechanism)
(2) Print speed
10 mm/second
(3) Print head
- Type
Thermal print head
- Heat generator
Consists of 64 heating elements vertically
aligned in 180 dpi
- Size of a heating element
0.18 mm wide by 0.127 mm high
(4) Character size
1.1.5 Tape Cassette
(1) Cassette
Cartridge type (TZ cassette)
(2) Types of tape cassettes
- Laminate tape cassette
- Non-laminate tape cassette
- Fabric tape cassette
(3) Tape size
1.1.6 Tape Cutter
(1) Tape cutting
Manual cutting with the cutter lever
(2) Cutter unit
User-replaceable
Size
1
2
3
4
5
16 dots
23 dots
29 dots
42 dots
56 dots
Type of tape
Width
Laminate tape
6, 9, 12 mm
Non-laminate tape
3.5, 6, 9, 12 mm
Fabric tape
12 mm
Summary of Contents for PT1090 - P-Touch - Labelmaker
Page 1: ...SERVICE MANUAL MODEL PT 1090 ...
Page 7: ...I 3 Figure 1 1 2 Display and Key Arrangement USA version EUROPE version ...
Page 74: ...A 1 Appendix 1 Main PCB Circuit Diagram NAME CODE MAIN PCB CIRCUIT DIAGRAM PT1090 LW4024001 ...
Page 75: ...A 2 Appendix 2 Key PCB Circuit Diagram NAME CODE KEY PCB CIRCUIT DIAGRAM PT1090 LW4025 001 ...