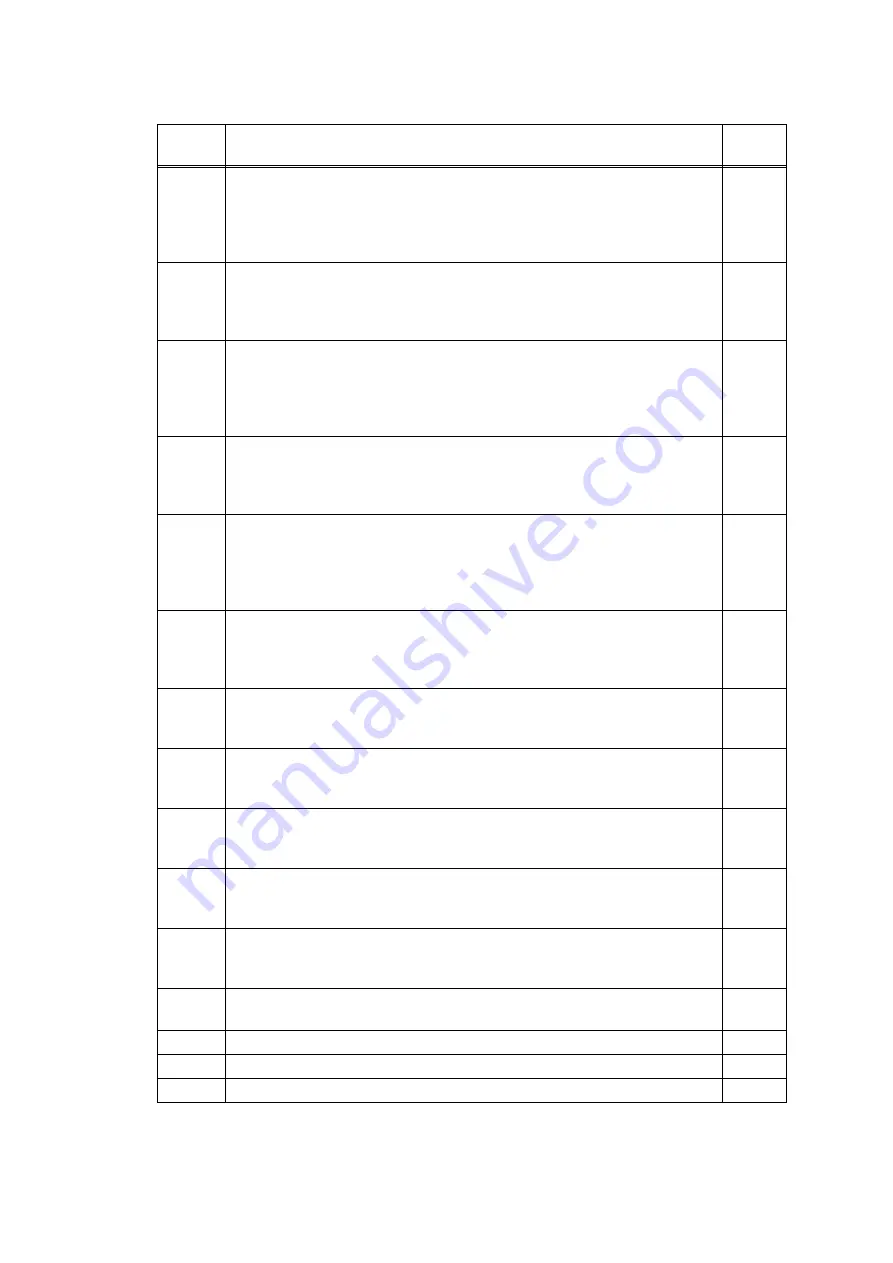
Confidential
2-15
Error
Code
Contents
Refer to
page:
8111
The paper size and paper type of each tray set during print setting are
different from before printing. This error occurs when the MP tray or
manual feed slot has been specified as a pickup tray with the highest
priority and plain paper has been specified as the paper type in auto tray
switching print.
8112
The paper size and paper type of each tray set during print setting are
different from before printing. This error occurs when the paper tray #1
has been specified as a pickup tray with the highest priority and inkjet
paper has been specified as the paper type in auto tray switching print.
8113
The paper size and paper type of each tray set during print setting are
different from before printing. This error occurs when the MP tray or
manual feed slot has been specified as a pickup tray with the highest
priority and inkjet paper has been specified as the paper type in auto tray
switching print.
8114
The paper size and paper type of each tray set during print setting are
different from before printing. This error occurs when the paper tray #1
has been specified as a pickup tray with the highest priority and Glossy
paper has been specified as the paper type in auto tray switching print.
8115
The paper size and paper type of each tray set during print setting are
different from before printing. This error occurs when the MP tray or
manual feed slot has been specified as a pickup tray with the highest
priority and Glossy paper has been specified as the paper type in auto
tray switching print.
8116
The paper size and paper type of each tray set during print setting are
different from before printing. This error occurs when the paper tray #2
has been specified as a pickup tray with the highest priority and plain
paper has been specified as the paper type in auto tray switching print.
8120
Recording paper size error (during PC printing/Copy/AirPrint printing)
The registration sensor and paper width sensor detect that the size of the
loaded recording paper does not match the recording paper size setting.
8200
Paper jam
- Paper width sensor cannot detect leading edge or width of recording
papers.
8400
Paper jam
- Registration sensor stays in paper feeding state even after completion
of paper ejection action.
8700
Paper jam
- Switchback sensor stays in paper feeding state even after completion of
paper ejection action.
8800
Paper jam
- Switchback sensor cannot detect paper feeding state even papers are
fed during printing.
8900
Paper width sensor cannot detect origin specified on the paper feed
roller.
8F00
Paper feed motor cannot stop.
8F01
PF encoder sensor cannot detect rotation of the paper feed motor.
9F00
3rd tray paper feed motor cannot stop.