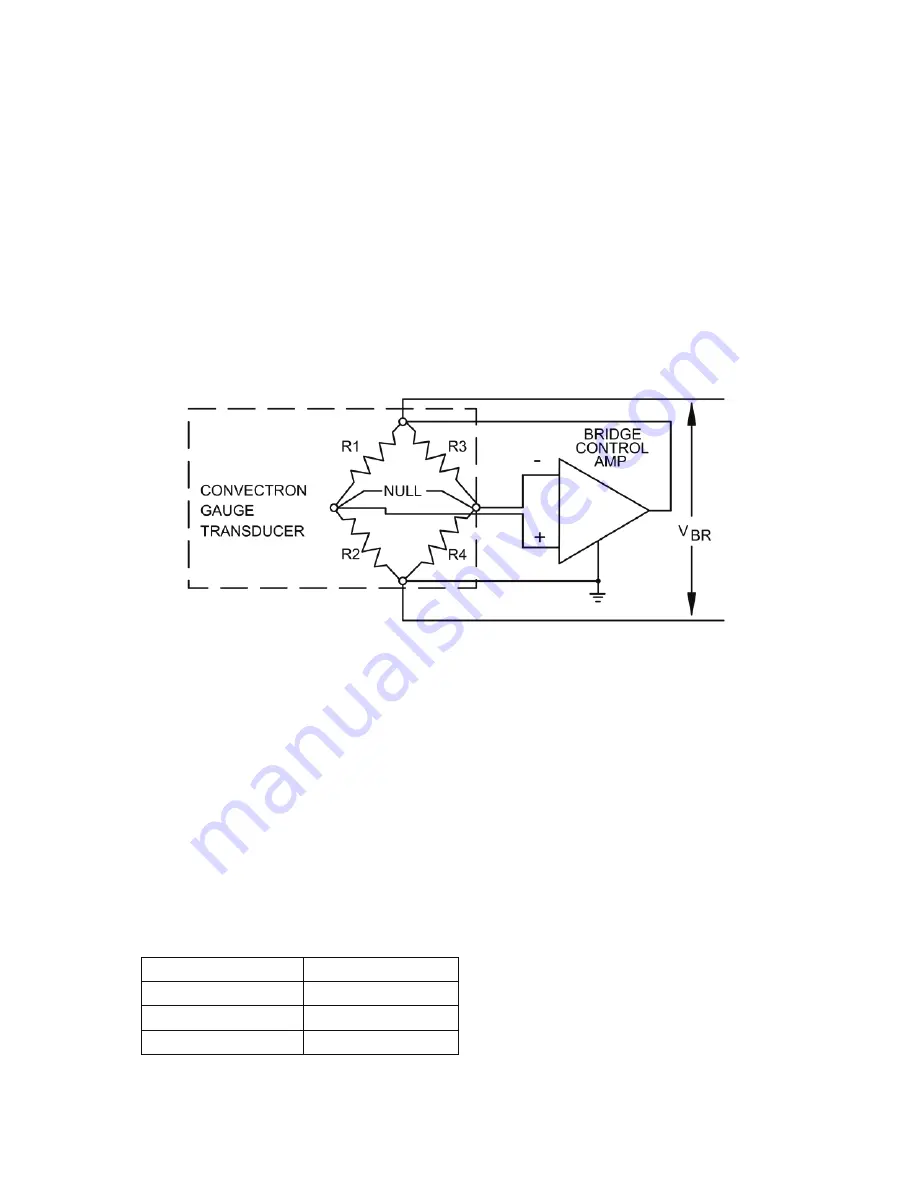
36
MANUAL P/N 316005 REV: B
2.6 Theory of Operation
The Convectron transducer is represented in Figure 2-13 as R1, R2, R3, and R4. These four resistances
form the legs of a bridge circuit, with R1 designating the sensor wire of the transducer. R2 is a resistive
network in the tube which compensates for changes in the ambient temperature. At bridge null:
R1=R2xR3/R4. If there are no changes in ambient temperature, the value of R1 is a constant and the bridge
is balanced.
As the vacuum system pressure is decreased, there are fewer molecules in the system to conduct the heat
away from the sensor wire causing the temperature and resistance of R1 to increase. The increased
resistance of R1 causes the bridge to unbalance and a voltage is developed across the null terminals. The
bridge control circuit senses the null voltage and decreases the voltage across the bridge until the null
voltage is again zero. When the bridge voltage is decreased, the power dissipated in the sensor wire is
decreased causing the resistance of R1 to decrease to its previous value. The opposite events happen for a
pressure increase. The bridge voltage is a non-linear function of pressure.
Figure 2- 13 Simplified Schematic of the Convectron Gauge
All materials have been chosen for ultra high vacuum service, corrosion resistance and bakeability to 150 °C.
The gauge tube envelope is type 304 stainless steel. All metallic joints in the envelope are welded. No solder
is used within the envelope. The following materials are exposed to the vacuum: Type 304 stainless steel,
Carpenter Alloy 52, Kovar, Kapton gold plated tungsten, and borosilicate glass and Dow Corning 9015 glass.
The blue trim cover is molded of polysulfone thermoplastic suitable for service to 150 °C.
2.7 Convectron Gauge Troubleshooting
2.7.1 Transducer Test Procedure
Do not perform electrical continuity tests with instruments applying in excess of 1 volt when the tube is at
vacuum, or 5 volts when at atmospheric pressure.
The 275 transducer should show the following resistances (pin numbers are embossed on the transducer
cap):
Pins 1 to 2
20 to 25 ohms
Pins 2 to 3
50 to 60 ohms
Pins 1 to 5
175 to 190 ohms
Any pin to envelope
open circuit
If the resistance from pin 1 to 2 is about 800 ohms, the sensor wire is broken.