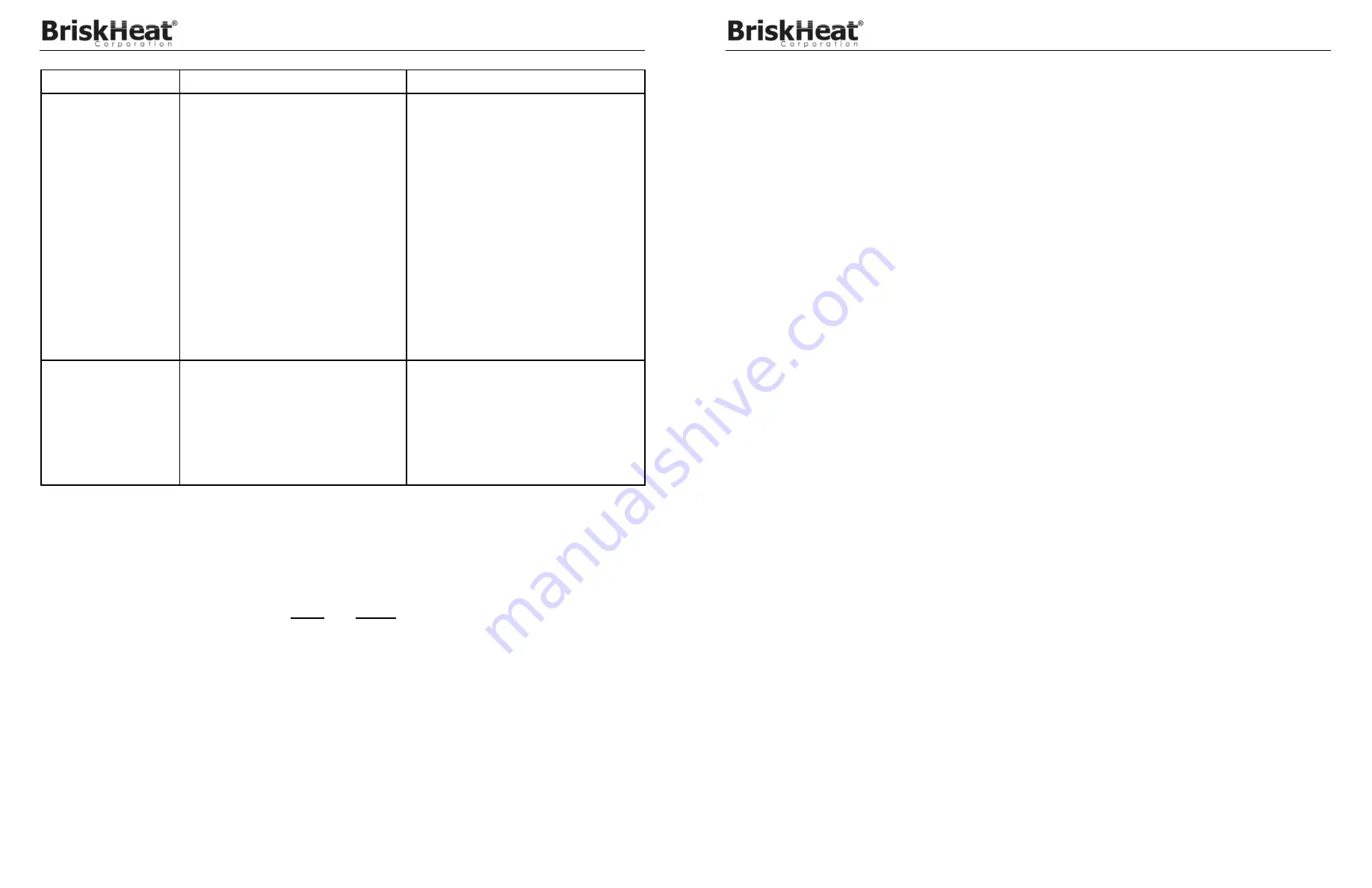
Self Regulating Heating Cable
© BriskHeat
®
Corporation. All rights reserved.
29
SYMPTOMS
PROBABLE CAUSE
CORRECTION
Power output is zero or
lower than rated.
***
1. Low or no input voltage.
2. Circuit is shorter than design shows.
a. Splices or tees may not have been
connected.
b. Heating cable may have been
severed.
3. Improper crimping causing a high resistance
connection.
4. Control thermostat is wired in the opened
position.
5. Pipe is at an elevated temperature.
6. Heating cable has been exposed to
excessive moisture.
7. Heating cable has been exposed to
excessive temperatures.
1. Repair electrical supply lines and equipment.
2. Check routing and length of heating cable
(use “as-builts”), and recalculate power
requirements.
a. Connect and recheck the power.
b. Locate and repair the damaged heating
cable. Recheck the power.
3. Re-crimp using correct procedure.
4. Rewire in the normally closed position.
5. Check pipe temperature and recalculate the
output.***
6,7. Replace the heating cable.
Power output appears
correct but pipe
temperatures are
below design value.
1. Insulation is wet.
2. Insufficient heating cable was used on
valves, supports, and other heat sinks.
3. Thermostat was set incorrectly.
4. There are thermal design inconsistencies.
1. Remove and replace with dry insulation and
insure proper weatherproofing.
2. Splice in additional heating cable but do not
go over maximum circuit length.
3. Reset the thermostat.
4. Check with the local or factory representatives
for design conditions. Modify as
recommended.
C.
D.
*** The power output on lower resistance heating cables is temperature sensitive and requires a special procedure to determine it’s
value.
1. Check the pipe temperature under the thermal insulation.
2. Allow heating cable to stabilize for 10 minutes and then measure the current.
3. Calculate the power (watts / ft.) of the heating cable by multiplying the current by the input voltage and dividing by the actual
circuit length
4. Compare this measured value to the power output curves for the heating cable at the measured pipe temperature. If the
heating cable’s actual output is substantially below the theoretical output, the bus wire interface with the core has been
damaged by the fault current and the cable must be replaced. This is not a highly accurate method of analysis, so use
discretion in comparing theoretical and actual values.
I xV
Watts
Ft.
Ft.
=
Self Regulating Heating Cable
© BriskHeat
®
Corporation. All rights reserved.
30
HEAT TRACE INSTALLATION RECORD
1. Circuit No._______________________________
2. Receiving Documentation
Date _____________________________________________
Item
DESIGN
ACTUAL
A. Cable Type
_______________________ _______________________
B. Cable Length
_______________________ _______________________
3. Receiving Testing
Date _____________________________________________
A. Check for physical damage
O.K. ___________________ Damage ________________
B. Continuity Check
Check for continuity between power leads.
O.K. ___________________ Open ___________________
C. 500VDC min., 2500VDC recommended,
megger check between leads and
sheath, 20 megohms min.
Megohms _________________________________________
D. Lot No.
No. ______________________________________________
4. Post Installation Testing
Date _____________________________________________
A. Continuity Check
Check for continuity between cold leads.
O.K. ___________________ Open ___________________
B. 500VDC min., 2500VDC recommended,
megger check between leads and
sheath, 20 megohms min.
Megohms _________________________________________
C. Visually Check Cable Installation Prior to
Release for Thermal Insulation.
Visual Check O.K. __________________________________
5. Final Testing and Commissioning
Date _____________________________________________
A. Circuit approved for testing by client.
Approved _________________________________________
B. 500VDC min., 2500 VDC recommended,
megger check between leads and
sheath, 20 megohms min.
Megohms _________________________________________
C. Energized Testing
(all test data to be within 10% of design data)
DESIGN ACTUAL
1. Circuit Voltage
_______________________ _______________________
2. Initial Current
_______________________ _______________________
3. Current after 15 minutes of operation
_______________________ _______________________
4. Current after 30 minutes of operation
_______________________ _______________________
5. Pipe temperature
_______________________ _______________________
6. Circuit Acceptance
_______________________ _______________________
This circuit has been tested and documented in accordance with the above itemized data. This circuit by:
Contractor_____________________________________________________________ Date_____________________
The
Heat Trace Installation Record
can be used to monitor the initial installation and check out process. This form can be used in
conjunction with the
Periodic Inspection Record
shown in
Figure 20
.
Figure 21