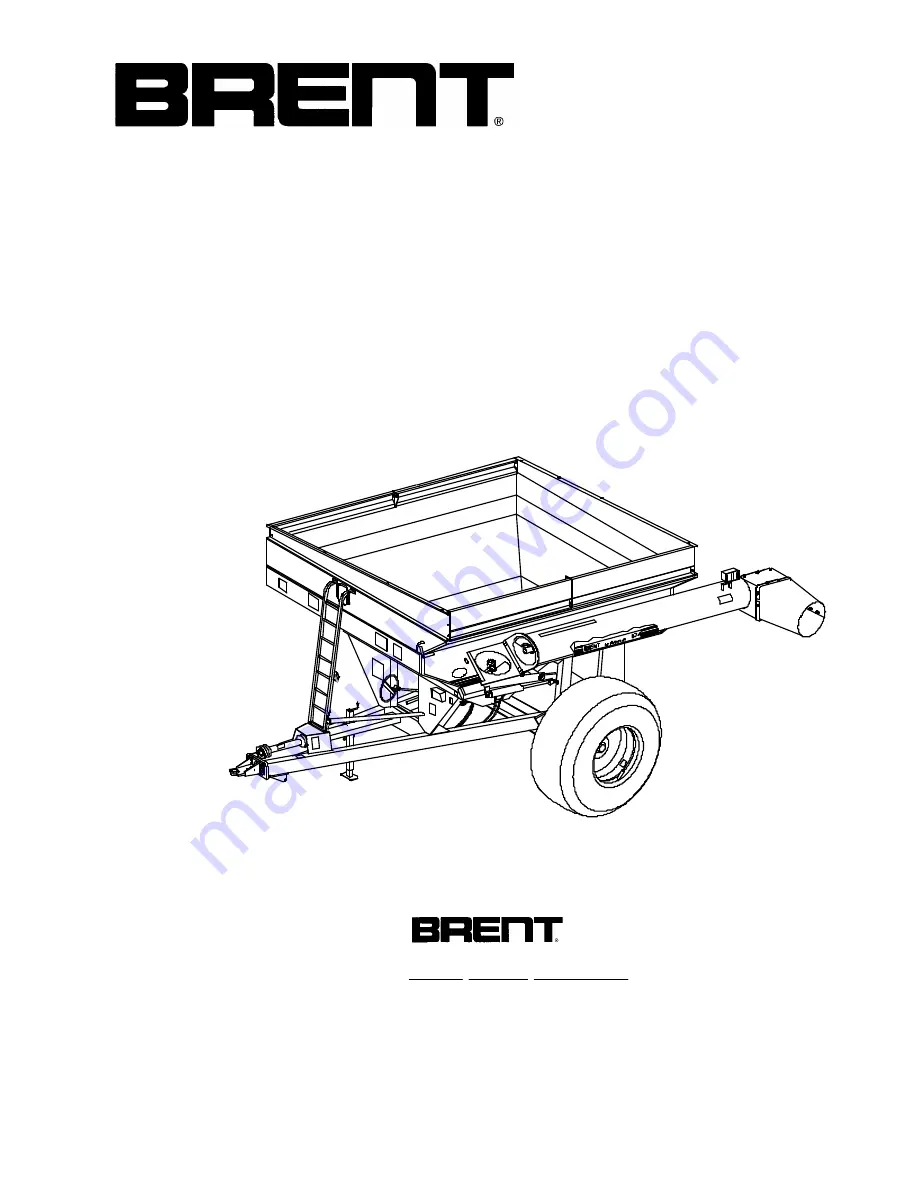
OPERATOR'S MANUAL
PARTS CATALOG
Unverferth
Manufacturing Co., Inc.
27612 Temple Ave.
Shell Rock, IA 50670
PH: 319-885-6571
Fax: 319-885-6576
Part #250475
Manufactured At:
MODELS
674 & 672
Corner Auger
TM
GRAIN CART
Model 674 Beginning With Serial Number B1651100
Model 672 Beginning With Serial Number B1649100
®
250915H
Summary of Contents for Corner Auger
Page 30: ...2 6 250937 06 30 00 ...
Page 44: ...2 20 233214D 07 14 98 ...
Page 50: ...3 2 SCALE KIT LAYOUT 250917 04 16 01 ...
Page 62: ...3 14 NOTES ...
Page 64: ...4 2 250932 11 13 97 ...
Page 70: ...4 8 234913 MODELS 672 674 TARP 04 01 02 ...
Page 79: ...4 17 NOTES ...