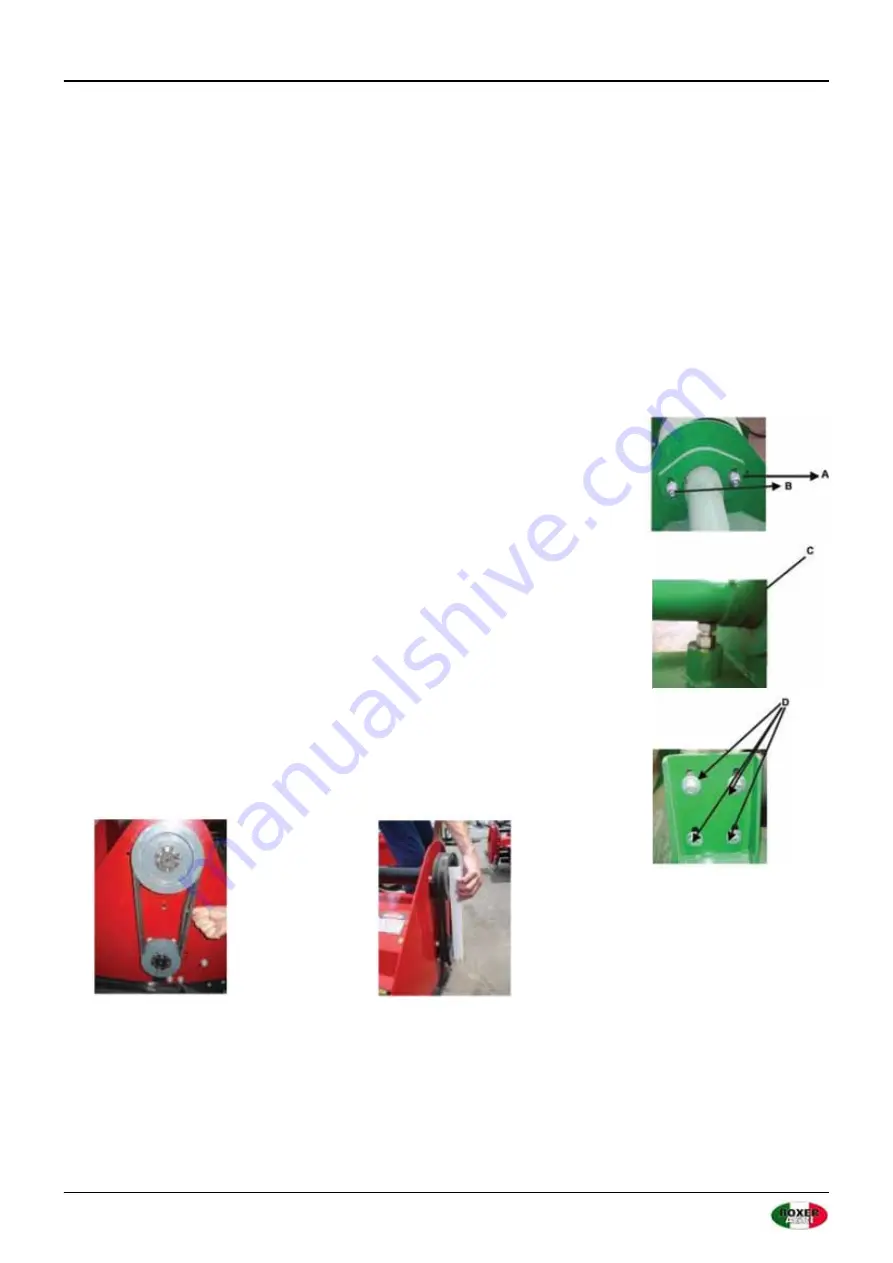
Page 30/42
MULCHING MOWER MASTER SERIES | User manual
February 2021
7.4
Adjusting the mulcher mower unit
Attach the mower unit to the tractor on a flat, level surface. Use an adjustable top link.
Lower the three-point mounting to its lowest position.
Adjust the length of the top link with the rear roller in contact with the ground, such that the lower edge on the side
of the mower unit is parallel to the ground.
The skids, the rear roller and the three-point mounting should be adjusted such that the distance between the
cutting tools and the ground is at least 50 mm.
Adjust the height of the roller to increase or decrease the blade clearance as required.
Operate the mower unit at a maximum PTO speed of 540 rpm.
7.5
Adjusting the drive belts
The correct drive belt tension is achieved by adjusting the belt pulleys. The pulleys
can be adjusted via the drive train height adjustment.
To do this, loosen screws A and B and loosen the height adjustment lock nut C and
the screws D holding the PTO transmission.
Adjust the drive belt tension. The correct belt tension is reached when the belt can
be deflected 10 mm max. in the center.
Align the transmission and drive shaft such that the drive shaft is parallel to the
body.
Use a spirit level or other tool to check that the pulleys are perfectly vertically
aligned, i.e. they must be vertically parallel above each other. If they have moved,
contact the seller for technical support. The pulleys are secured by an expander
cone on the respective shaft and can be moved horizontally after loosening the
expander cone.
10 mm deflection max.
Check the vertical alignment of the pulleys using a
spirit level. The pulleys must be absolutely parallel.