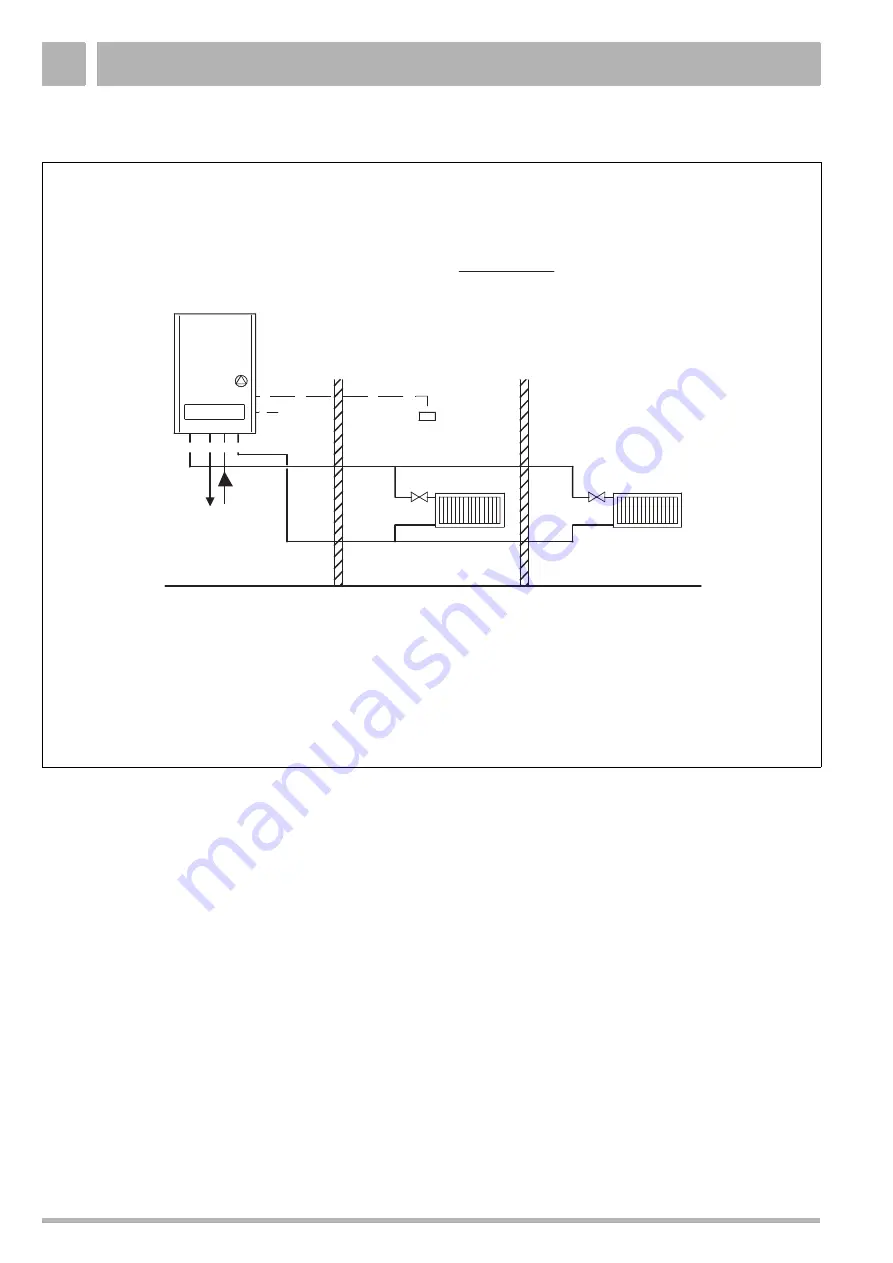
Installation
1
20
Installation and maintenance instructions for wall-mounted condensing gas boiler 600 - 28C • 01/2004
Subject to modifications resulting from technical improvements!
Boulter Buderus Ltd. • http://www.boulter-boilers.com
1.10.6 System example
fig. 26 System example
Condensing gas boiler 600 Series
with downstream heating circuit without actuator
Key to abbreviations:
Note that example systems are to be regarded
as schematic representations only.
1) Thermostat valve not required or to be opened fully, if regulation is carried out via ModuLine room-temperature controlled system .
2) If system is regulated via ModuLine external-temperature controlled unit.
AB DHW
warm
EK DHW
cold
RK CH
return
HV Radiator
valve
VK CH
flow
HV
2x0,75
2
EK RK
VK AB
ModuLine
Reference room
HV
Other rooms
Mains
Condensing gas boiler
600 – 28C