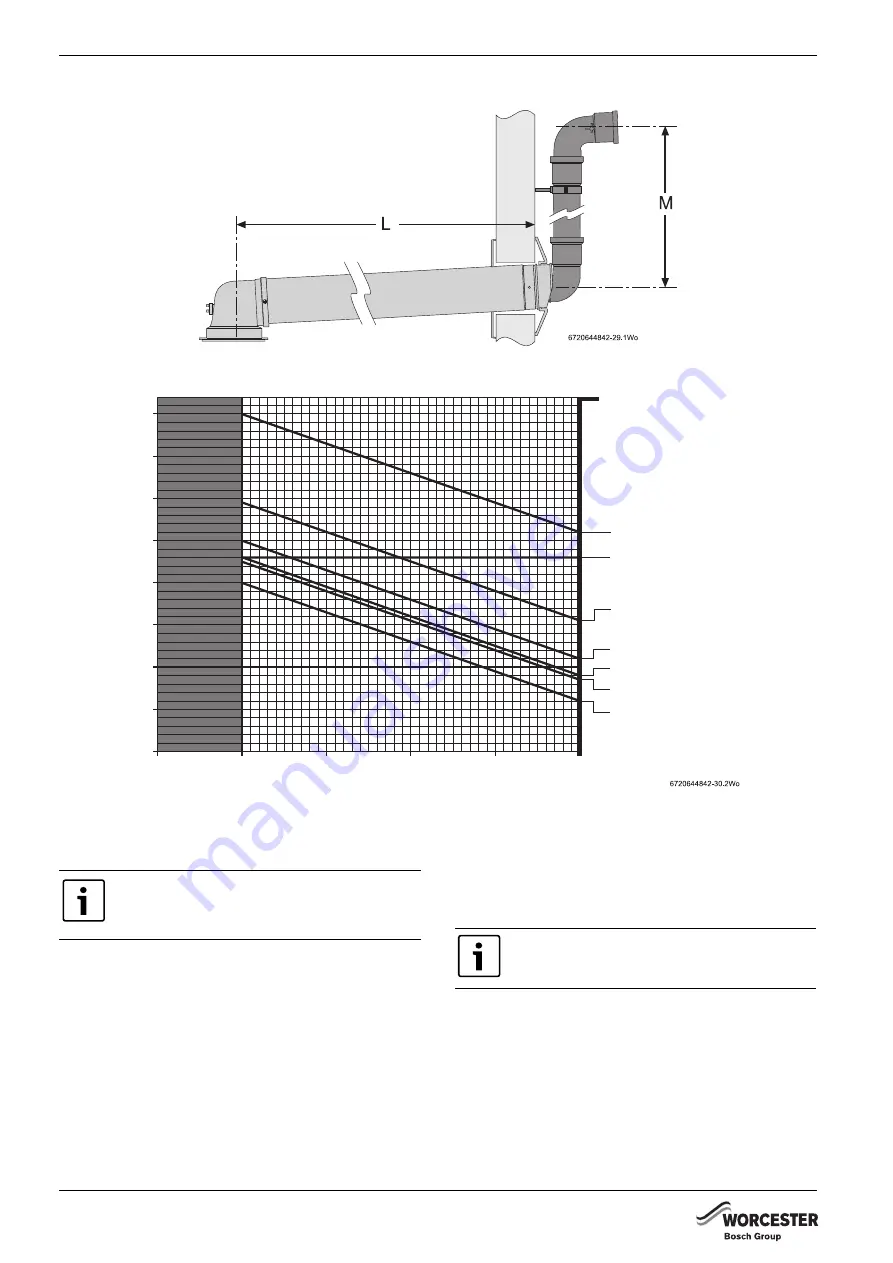
PRE-INSTALLATION
6 720 644 842b (2010/12)
18
6.2.1
DETERMINE THE PLUME MANAGEMENT SYSTEM LENGTH
Fig. 32 Effective lengths L and M
Fig. 33 Effective flue lengths versus plume management lengths
PLUME LENGTH
Refer to figure 33 to determine the appropriate plume
length versus the flue length (L).
The flue length is the effective length (L), which includes
the effective length of any bends plus the straight flue
lengths.
Once the length L is know, find that value on the vertical
scale of the graph and read that across to the line that
represents the installed boiler.
From that point read down to the horizontal scale to
determine the maximum plume length (M) allowed.
For the CDi range of boilers, the available plume length
(M) is reduced as the flue length (L) increases. Any flue
must have a minimum of 500mm plume length.
0
500
1,500
2,500
3,500
4,500
0
1,000
2,000
3,000
4,000
5,000
6,000
7,000
8,000
27CDi
Maximum Plume Length
for all boilers
30CDi
BG532/i
37CDi & BG537/i
42CDi, 40CDi Regular &
BG542/i
30CDi Regular, System &
BG430/i
MINIMUM PLUME KIT LENGTH 500 mm
Ef
fective Flue length ‘L
’ mm
Plume management length allowed ‘M’ mm
Si, i Junior, i System & Ri
The minimum plume length for all boilers
stated on the front page of this manual is
500mm.
The Si, i System, i Junior and Ri can use up
to 4,500mm of plume management
regardless of flue length.
Summary of Contents for WORCESTER Condensfit II GREENSTAR 60/100 HORIZONTAL FLUE
Page 26: ...6 720 644 842b 2010 12 26 NOTES ...