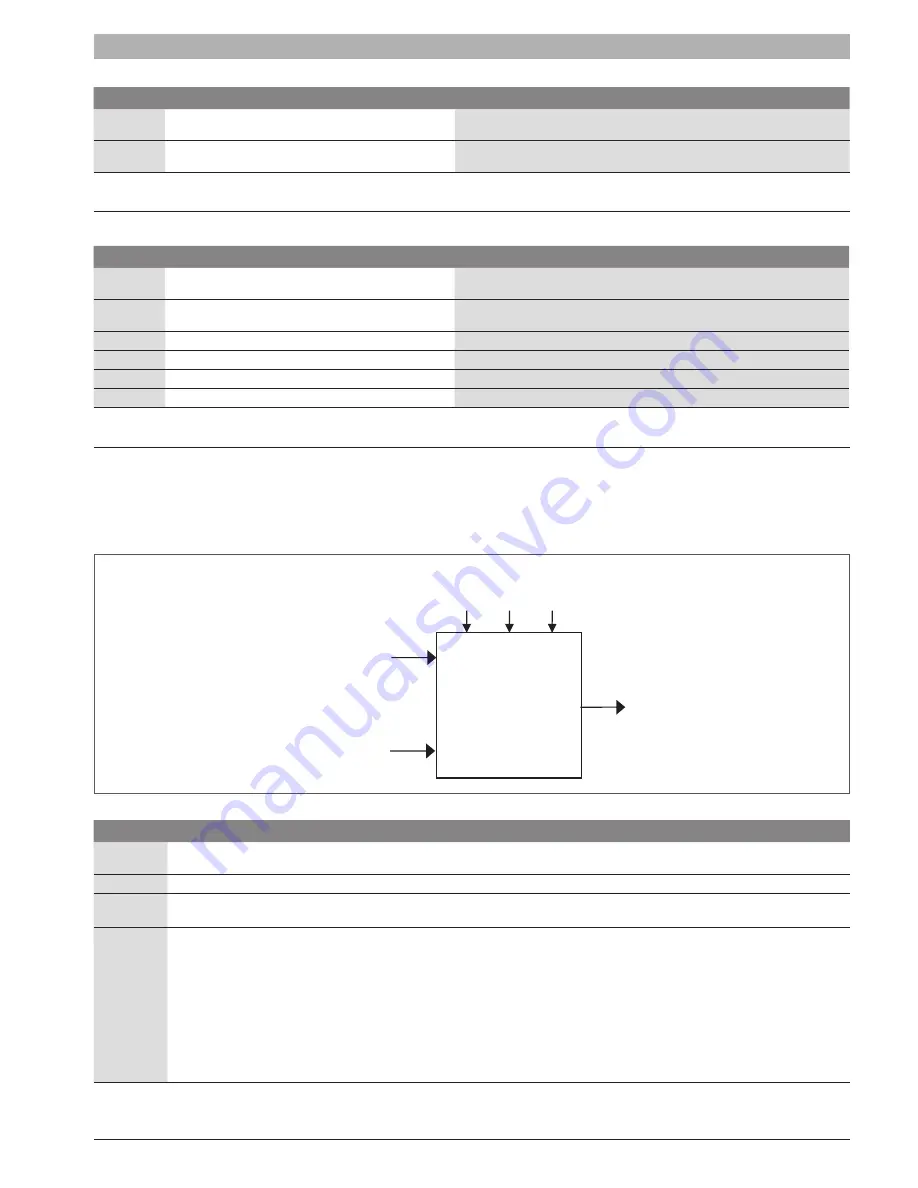
SSB
6720892984 (2019/02) US
Service reminder | 59
Error no .
Error
Description
162
FLUE_BLOCKED
Flue is blocked, demand needs to be stopped with fan at ignition speed*, but
no error needed to be stored at this time
163
LOWEXFLOW_PROTECTION
Flow is too low, demand needs to be stopped with fan at ignition speed*, but no
error needed to be stored at this time
F .4
Warnings
Error no .
Error
Description
200
CC_LOSS_COMMUNICATION
Cascade System: Leading burner lost communication with one of the
depending burners.
201
CC_LOSS_BOILER_COMM
Cascade System: Leading boiler lost communication with one of the depending
boilers.
202
OUTDOOR_WRONG
Outdoor sensor is open of shorted
203
T_SYSTEM_WRONG
T_System sensor is open of shorted
204
T_CASCADE_WRONG
T_Cascade sensor is open of shorted
205
MAX_HIGH_LIMIT_WARNING
Too many physical high limit test attempts within 24 hours.
Appendix G - PID: Proportional-Integral-Derivative controller
For demand handling a software PID controller is implemented.
The PID controller calculates its output value as a function of the PID parameters, the setpoint and the input. The output can be used to control the fan for
regulation of power, or pump for controlling the flow, depending on the application.
Parameters used for the calculation are:
Input value
(sensor value, such as temp.)
Setpoint
Output value
PID
PARAMETERS
P I D
Input value
As input the parameter that needs to be controlled is given. In most cases this is a sensor temperature. This PID controller will then
control this input value to the given setpoint.
Setpoint
The setpoint value is the target value to which the input value is controlled to. This must be entered in the same format as the input value.
Output
The output is the target power to control the input value towards the setpoint.
The output value can be scaled between a minimum and maximum output so this can be used in a understandable format.
P
The P parameter of the PID-controller is used to adjust the speed of the regulation.
With a larger P-factor the regulation is faster, but it is more likely to create overshoot on the regulation.
The formula is P_Power = P * Error, where the error is the difference between the setpoint and the actual temperature in 1/32 degree
temperature steps. The P is a positive value when the difference (Setpoint > actual temperature) is also positive. This value is a part of the
output power.
The P is a negative value when the difference is also negative (Setpoint < actual temperature).
This means that this part of the output power is negative.
Summary of Contents for SSB1000 SA
Page 82: ...6720892984 2019 02 US SSB ...
Page 83: ...SSB 6720892984 2019 02 US ...