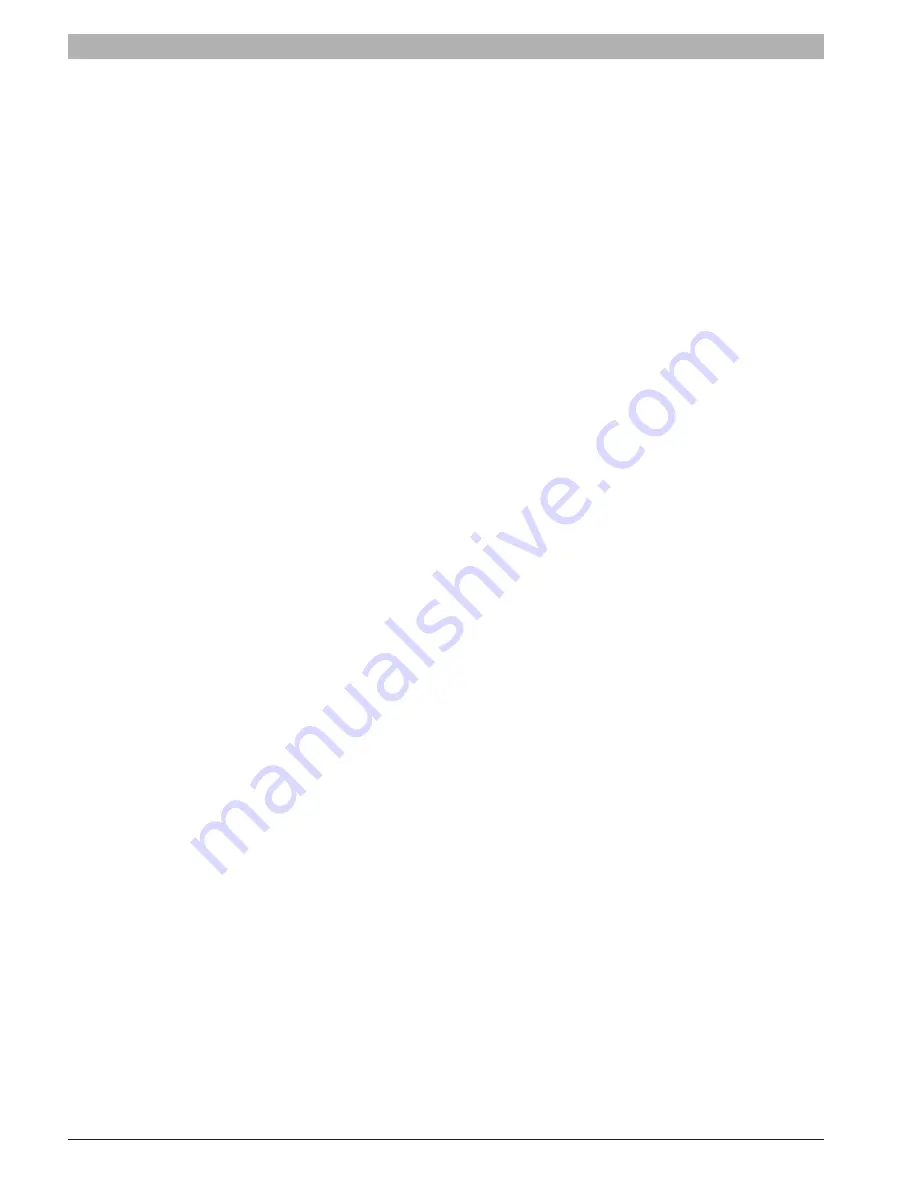
6720892984 (2019/02) US
SSB
10 | BURNERS cascade
3 .2 .3
Communication with LabVision PC software
There are two options for communication with the LabVision PC software.
The 850US Device (Argus-to-USB) can either be parallel connected to
the cascade communication bus or separately to the J8 connection on the
leading burner.
When the 850US Device (Argus-to-USB) is connected to the J8
connection, switch S1 has to be set in the ON position. This powers
the communication bus to allow communication with the Labvision PC
software.
NOTE: there is less information available when connected to the J8
connection on the leading burner. Only the information known by
the leading burner can be shown in the Labvision PC software.
3 .3
Cascade – Heating only (Rev . 4 .0 .905 .15250)
Managing burner
When a burner is set as Managing (Address = 1), the controller of this
burner will drive the cascade. The CH mode of this managing burner
applies to all other burners. It is only required to set the CH mode on the
managing burner.
• The outdoor temperature sensor connected to the managing burner
will be the outdoor sensor for the cascade operation
• The system sensor (
T_System
) connected to the managing burner
will be the control sensor for the cascade supply temperature.
• The (modulating) thermostat connected to the managing burner will
be the CH heat demand input for the cascade system.
Based on the system temperature
(T_System)
and the requested
Cascade_Setpoint
the managing burner calculates a required burner
setpoint, to achieve the requested
Cascade_Setpoint
.
The managing burner provides the calculated setpoint to all dependent
burners. The modulating power of the dependent burners is PID
controlled based on the calculated setpoint and dependent burner supply
temperature.
Cascade CH setpoint adaption
When the system temperature is not high enough the setpoint for all
burners will be adjusted.
The boiler setpoint will be increased when the system temperature
drops below
Cascade_Setpoint
and decreased when it rises above
Cascade_Setpoint temperature
.
This is determined as following:
A PID-control loop over the system temperature
(Cascade_Setpoint /
T_System)
calculates the adjustment of the boiler setpoint. The range of
the PID controller is between
(Cascade_Se Max_Range_
Up_Limit)
and
(Cascade_Setpoint – Min_Range_Down_
Limit)
. This offset is added to the
Cascade_Setpoint
and then this
calculated boiler setpoint will be limited at
CH_Max_Setpoint
(by
default 80°C (176°F)).
When the system temperature is above cascade setpoint, the calculated
boiler setpoint will be decreased with a step defined by parameter
PID_
Slew_Rate_Step_Down
(default 1°C (1,8°F)).
In case the system temperature is below cascade setpoint the calculated
boiler setpoint will be increased with a step defined by parameter
PID_
Slew_Rate_Step_Up
(default 1°C (1,8°F)).
The PID calculation does not start immediately but after a certain delay
period to stabilize the system first.
The delay period is
Start_PID_Modulation_Delay_Factor
(settable), for example 60 minutes.
Summary of Contents for SSB1000 SA
Page 82: ...6720892984 2019 02 US SSB ...
Page 83: ...SSB 6720892984 2019 02 US ...