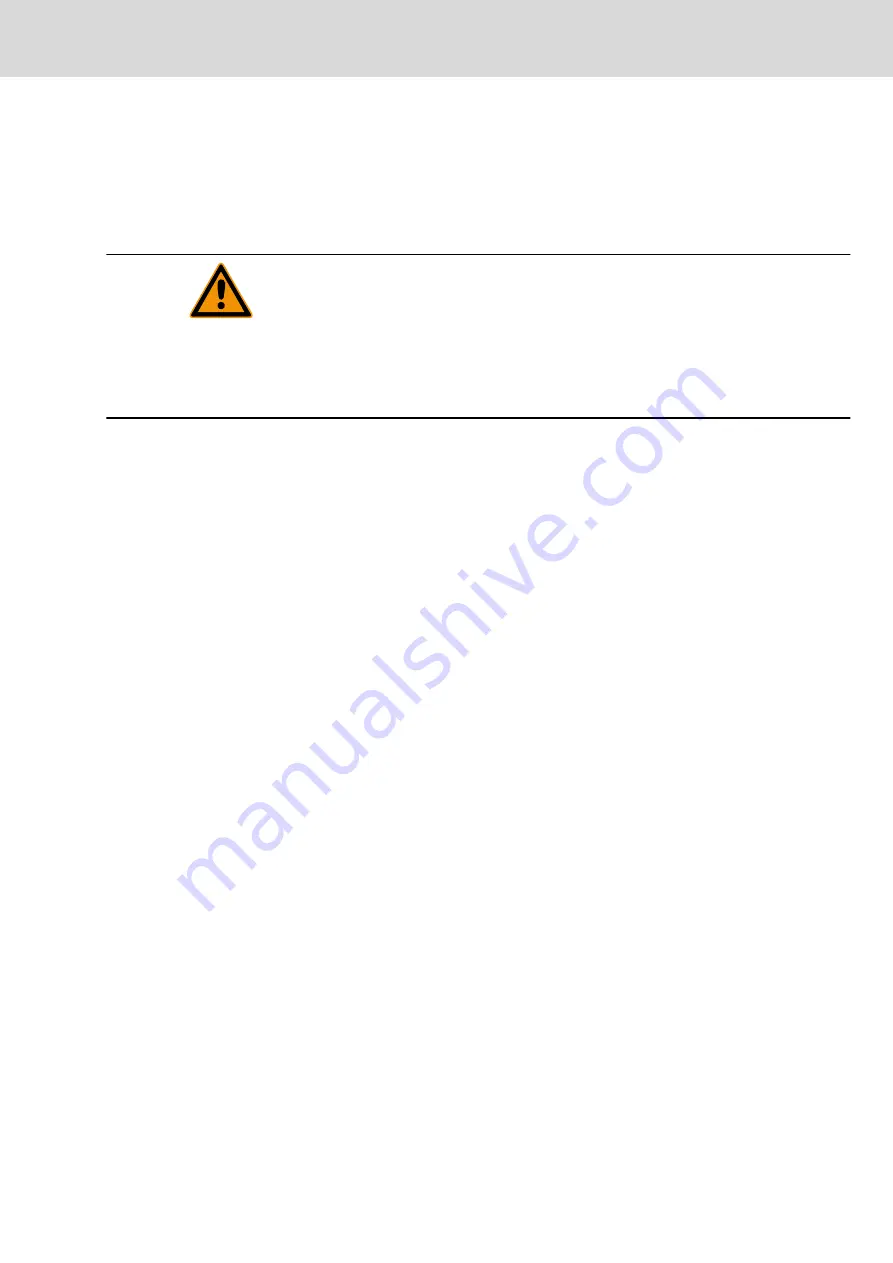
3.6
Protection Against Electric Shock (PELV) by Protective Extra-
Low Voltage
All connections and terminals on Rexroth products with voltages of 5 to 50 volt
are protective extra low voltages, made to protect against contact in accordance
with the following standards:
WARNING
High electric voltage by incorrect connection! Risk of death or bodily
injury by electric shock!
●
Only devices, electrical components and lines with a Protective Extra Low
Voltage (PELV) may be connected to any connections or terminals with
voltages of 0 to 50 volt.
●
Only connect voltages and circuits that have safe isolation from dangerous
voltages. Safe isolation can be achieved, for example, by isolating trans‐
formers, safe opto-electronic couplers or mains-free battery operation.
3.7
Protection Against Dangerous Movements
Dangerous movements can be caused by faulty control of connected motors.
Some common examples are:
●
improper or wrong wiring of cable connections
●
incorrect operation of the equipment components
●
wrong input of parameters before operation
●
malfunction of sensors, encoders and monitoring devices
●
defective components
●
software or firmware errors
These errors can occur immediately after equipment is switched on or even
after an unspecified time of trouble-free operation.
The monitoring in the drive components will normally be sufficient to avoid faulty
operation in the connected drives. Where personnel safety is concerned, par‐
ticularly where there is a risk of physical injury and/or damage to property, this
fact should not be relied on exclusively. Until the integrated monitoring functions
become effective, it must be assumed in any case that faulty drive movements
will occur. The extent of faulty drive movements depends upon the type of con‐
trol and the state of operation.
Project Planning Manual | Rexroth IndraControl VAU 01.1Z
Electric Drives
and Controls
| Bosch Rexroth AG
11/45
Safety Instructions for Electric Drives and Controls