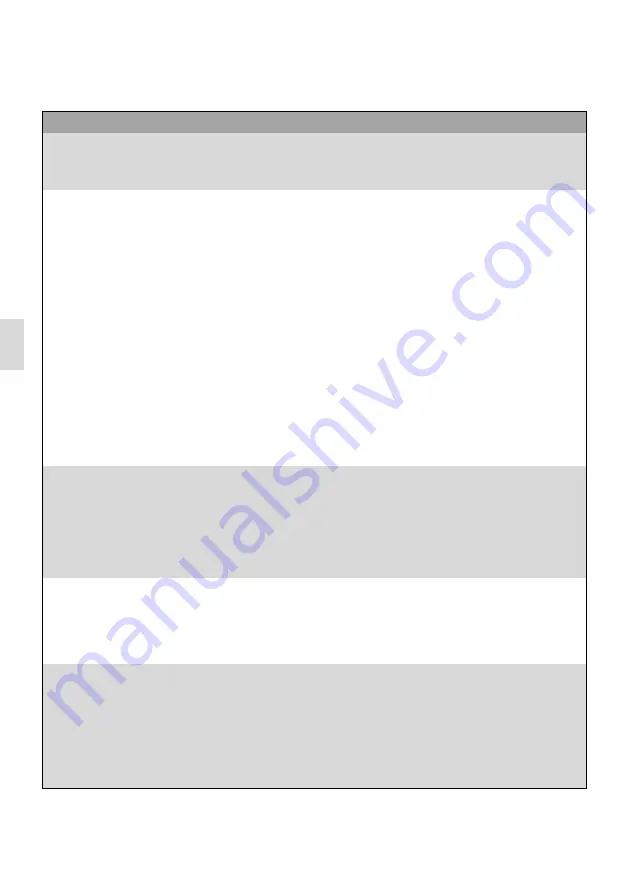
Bominox, S.A. - Installation and Maintenance Instructions
EN 12
E
N
5
Troubleshooting
These instructions do not cover all the details of variations of the equipment nor do they cover each and
every one of the possible conditions that may arise in relation to the installation, use or maintenance.
Contact Bominox if additional technical information is required.
Problem
Causes
Solutions
The pump does
not start
•
There is no voltage in the network
Connect power supply
•
Motor and/or power cables are
damaged
Repair the motor and/or replace cables
•
Protection against actioned overload
Rearm protection
The pump does
not have
sufficient flow
•
Rotation direction incorrect
Reverse the rotation direction by
exchanging the position of the two
wires on the motor’s power supply.
•
Discharge pressure too high.
Reduce load losses by changing the
tubes for tubes with a larger diameter.
•
Cavitation (insufficient available NPSH) Increase the suction level difference
(raised the tank or lower the pump)
Place the pump as close as possible to
the suction tank
Increase the diameter of the suction
tube
Check whether the tube is obstructed
and clean it if necessary
Work with the liquid at a lower
temperature
Pressurise the tank
•
The pump sucks air
Check the seal of the suction tube and
all of its connections
•
Viscosity too high
Increase the temperature of the liquid
Install a larger pump
Motor overload
•
Flow too high
Close the discharge valve
Reduce the diameter of the impeller
Reduce rotation speed using a
frequency variator
•
Density and/or viscosity too high
Fit a higher power motor
Reduce the diameter of the impeller
•
Foreign bodies inside the body
Check and remove
•
The impeller is grazing with the body
Adjust impeller
Vibrations and
noise
•
Cavitation (insufficient available NPSH) See solutions in the previous section
(The pump does not have sufficient
flow)
•
Worn motor bearings
Change them
•
Pressure in the tubes
Fit fastening on the tubes
•
Foreign bodies inside the body
Check and remove
Liquid leak
•
Mechanical seal damaged or worn
Check that the pump has not been
running dry
Check that the materials are compatible
with the liquid being pumped
Replace the mechanical seal
•
O-ring damaged or worn
Check that the seal is compatible with
the liquid being pumped
Replace the O-ring ensuring that it is
not incorrectly fitted or pinched