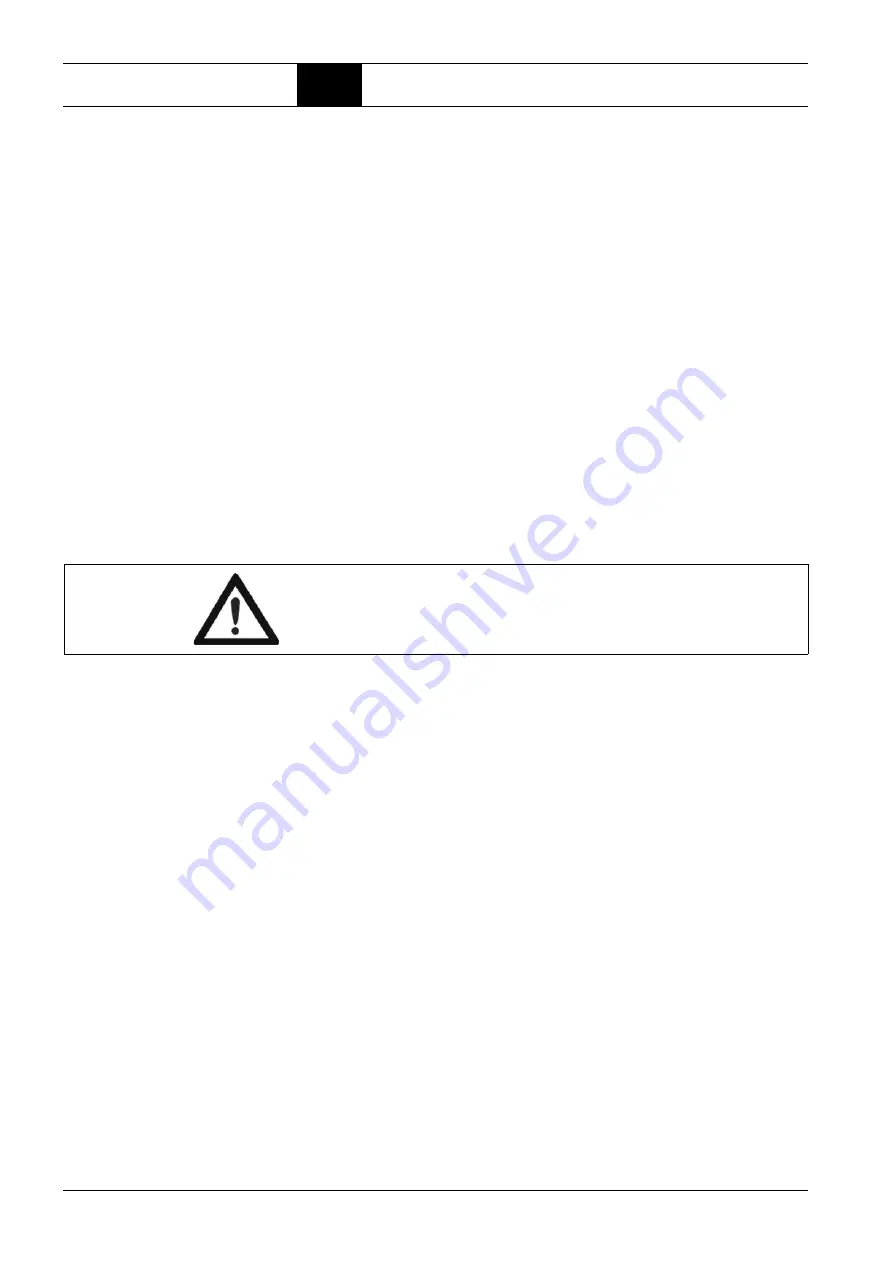
Accessory equipment
5.1
BOGE Duotherm BPT
Page 48
Operating instructions for S 40-3...S 150-3 series screw compressors
Commissioning
Proceed as follows during commissioning:
–
Check oil level in the oil circuit. If necessary, top up with oil.
–
Slowly open the stop valves in the water supply and discharge line.
–
Avoid pressure hammers!
–
Vent the pipelines.
Maintenance
Limescale, oxides as well as grease or oil will be deposited in the ducts in the
plate heat exchanger during operation
Regular cleaning will prevent thick deposits clogging individual ducts of the
plate heat exchanger.
Cleaning intervals
Excessively soiled or hard water:
6 months
Moderately soiled water, surface water: 1 year
Lightly soiled water:
3 years
Recommended cleaning agents
Grease or oil deposits:
Paraffin
Oxide or limescale deposits: formic acid, acetic acid or citric acid
Cleaning methods
Flushing:
–
First close all stop valves in the supply lines.
–
Close all stop valves in the discharge lines.
–
Wait until the plate heat exchanger has cooled down.
–
Open the flushing connections and drain the plate heat exchanger.
–
Flush out the plate heat exchangers.
For this purpose, pump one of the above mentioned cleaning agents
through the plate heat exchangers for an extended period of time.
–
After flushing, rinse the plate heat exchanger thoroughly with water
(e.g. using a pressure washer).
Enhance the cleaning action by the following measures:
–
Use a larger mass flow rate than for standard operation.
–
Flush the cleaning agent through the plate heat exchanger in the opposite
direction to standard operation.
Allow to react (tenacious soiling):
–
Dismantle plate heat exchanger.
–
Fill plate heat exchanger with one of the above-mentioned cleaning agents.
–
Allow the cleaning agent to act for at least six hours. Point the connections
upward to allow any gases that may occur to escape.
WARNING!
Always observe the instructions of the cleaning agent manufacturer!