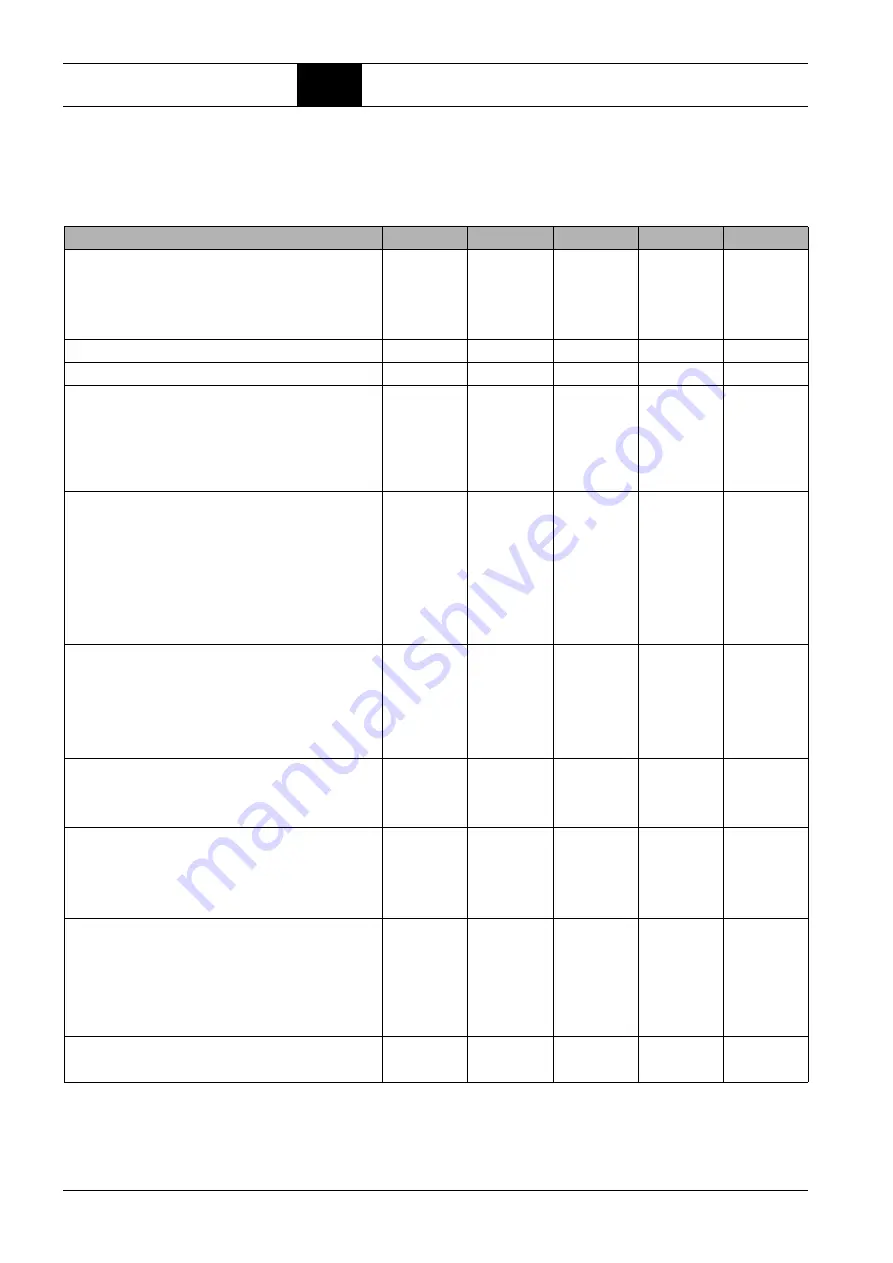
Product description
3.4
Technical data
Page 22
BOGE Operating instructions for scroll compressors, series EO 6...EO 22 D
3.4 Technical data
Technical data EO 6...EO 6 TR, part 1
Type
EO 6
EO 6 D
EO 6 R
EO 6 DR
EO 6 TR
Dimensions
– Width
[mm]
670
670
1785
1760
1825
– Depth
[mm]
1000
1000
745
745
1000
– Height
[mm]
972
1385
1670
1670
1725
Standard receiver capacity
[l]
–
–
270
270
350
Weight
[kg]
250
336
368
405
647
Maximum emitted sound pressure level
[±3 dB(A)]
as per EN ISO 2151
Super silenced 8 bar / 10 bar
[dB(A)]
62 / 59
62 / 59
62 / 59
62 / 59
62 / 59
Measuring surface
[dB(A)]
15
15
15
15
15
Sound power level 8 bar / 10 bar
[dB(A)]
77 / 74
77 / 74
77 / 74
77 / 74
77 / 74
Compressor
Max. final compression temperature
[°C]
250
250
250
250
250
Compressed air outlet temperature over intake air
temperature, approx.
[K]
15
15
15
15
15
Volume flow in accordance with ISO 1217 Annex C at:
– p
max
= 8 bar
[m
3
/min]
0.62
0.62
0.62
0.62
1.24
– p
max
= 10 bar
[m
3
/min]
0.49
0.49
0.49
0.49
0.98
Drive motor
Rated power
[kW]
5.5
5.5
5.5
5.5
2x 5.5
Nominal speed
– with motors for 50 Hz
[rpm]
1465
1465
1465
1465
2x 1465
– with motors for 60 Hz
[rpm]
1765
1765
1765
1765
2x 1765
Protection class
IP
55
55
55
55
55
Design
IMB
3
3
3
3
3
ISO class
F
F
F
F
F
Electrical Connection
Supply voltage / frequency
1
)
[V/Hz]
1)
Standard equipment. Supply voltages and frequencies are detailed on a sign in the switch cabinet.
400 / 50
400 / 50
400 / 50
400 / 50
400 / 50
Recommended fuse protection at 400 V
2
)
3
)
[A]
2)
Different supply voltages alter the values for the fuses.
3)
Use fuse cut-outs gG or miniature circuit-breakers with C characteristic.
* per compressor.
25
25
25
25
25*
Supply voltage / frequency of dryer
1)
[V/Hz]
–
230 / 50
–
230 / 50
–
Deviating voltage / frequency
Supply voltage / frequency
[V/Hz]
230 / 50
220/440 / 60
220 / 60
380 / 60
440 / 60
230 / 50
220/440 / 60
220 / 60
380 / 60
440 / 60
230 / 50
220/440 / 60
220 / 60
380 / 60
440 / 60
230 / 50
220/440 / 60
220 / 60
380 / 60
440 / 60
230 / 50
220/440 / 60
220 / 60
380 / 60
440 / 60
Recommended fuse protection at 220 V / 230 V
[A]
32
32
32
32
32*
Recommended fuse protection at 380 V / 440 V
[A]
25
25
25
25
25*