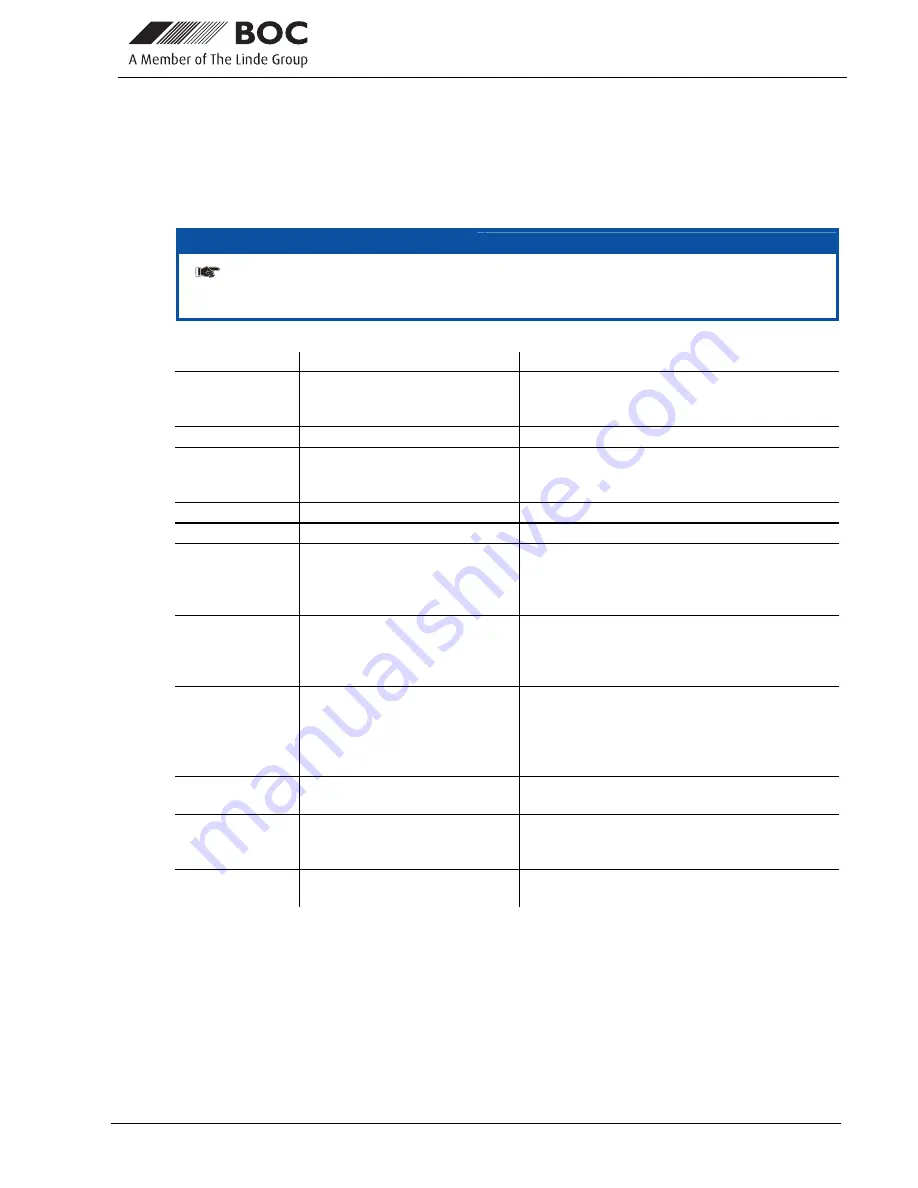
Rectifying faults
Machine faults (error messages)
099-000143-BOC01
16.11.2009
61
7
Rectifying faults
All machines are subject to rigorous production checks and final checks. If despite this, anything fails to
work at any time, please check the machine using the following chart. If none of the fault rectification
procedures described leads to the correct functioning of the machine, please inform your authorised
dealer.
7.1
Machine faults (error messages)
NOTE
A welding machine error is indicated by the collective fault signal lamp (A1) lighting up
and an error code (see table) being displayed in the machine control display. In the event
of a machine error, the power unit shuts down.
• Document machine errors and inform service staff as necessary.
Error message
Possible cause
Remedy
E1
Water fault
Only occurs if a water cooling
unit is connected.
Ensure that sufficient water pressure can be built
up. (e.g. top up water)
E2
Temperature error
Allow machine to cool down.
E3
Electronics error
Switch machine off and on again.
If the fault persists, inform the service
department.
E4
see "E3"
see "E3"
E5
see "E3"
see "E3"
E6
Balancing error in voltage
recording.
Switch machine off, place the torch on an
insulated surface and switch on again.
If the fault persists, inform the service
department.
E7
Balancing error in current
recording.
Switch machine off, place the torch on an
insulated surface and switch on again.
If the fault persists, inform the service
department.
E8
Error in one of the electronics
supply voltages or excess
temperature of the welding
transformer.
Allow machine to cool down. If the error message
persists, switch the machine off and back on
again.
If the fault persists, inform the service
department.
E9
Low voltage
Switch off the machine and check the mains
voltage.
E10
Secondary overvoltage
Switch machine off and on again.
If the fault persists, inform the service
department.
E11
Overvoltage
Switch off the machine and check the mains
voltage.