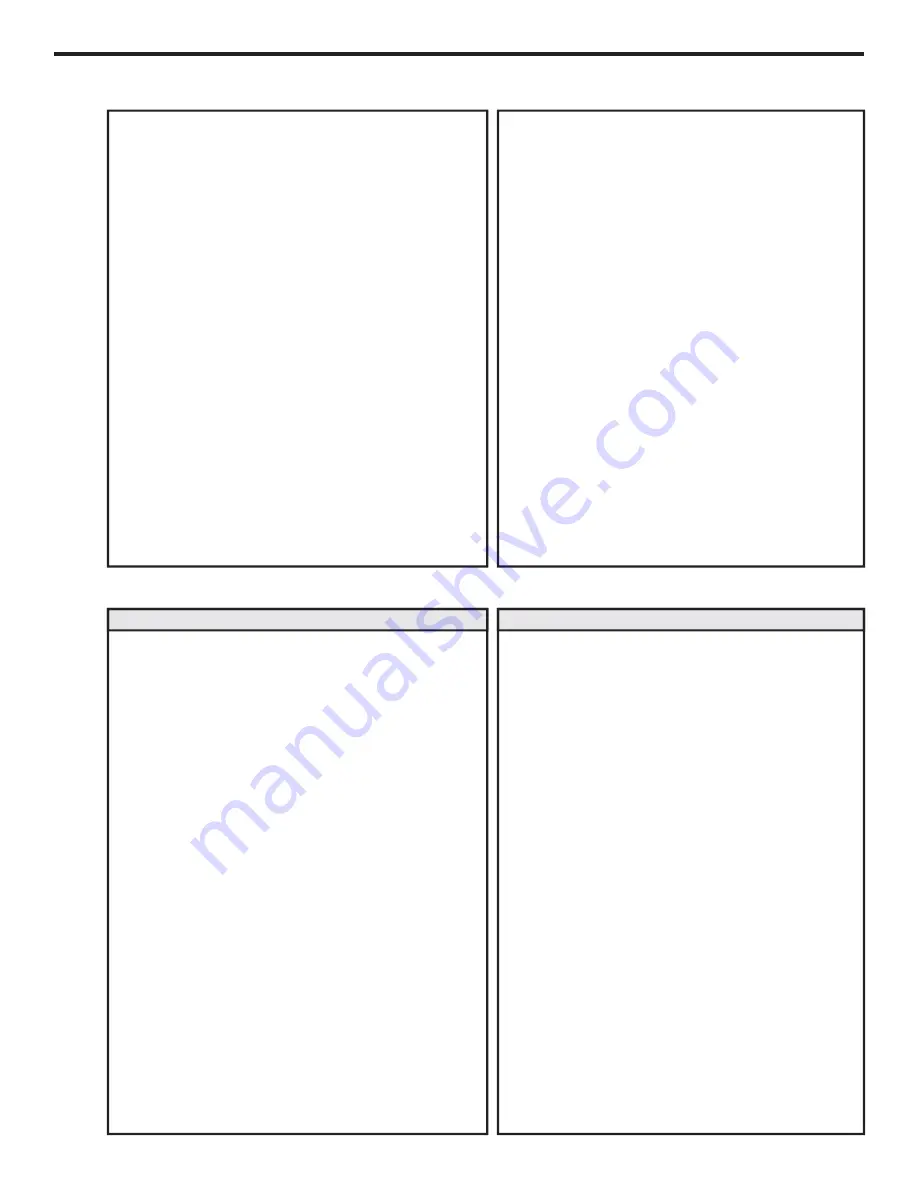
Pump Tube Assembly:
®
Tubing:
.................Flex-A-Prene
Adapter Fittings:
PVDF
NOTE
: This is model specific, and two are provided.
Injection / Back-Flow Check Valve:
Body & insert:
....................PVDF
Check Ball:
.........................Ceramic
Spring:
................................Hastelloy C-276
Ball Seat O-Ring:
................FKM (optional EPDM)
Static Seal O-Ring:
.............FKM (optional EPDM)
Ancillary Items Provided:
Suction Tubing:
..................3/8” OD x 1/4” ID x 10’ Clear PVC
Discharge Tubing:
.............3/8” OD x 1/4” ID x 10’ Polyethylene
(LLDPE)
Suction Strainer:
...............PVDF
Suction Strainer:
Body:
...................................PVDF
Check Ball:
.........................Ceramic
Ball Seat O-Ring:
................TFE/P (Optional EPDM)
With “M” Tubing M/NPT Connections Only:
Suction Strainer:
Body:
...................................PVDF
Check Ball:
.........................Ceramic
Ball Seat O-Ring:
................TFE/P (Optional EPDM)
2.0
Engineering Specifications
2.1
Materials of Construction
Wetted Components:
Non-Wetted Components:
Enclosure:
413 Aluminum (Polyester powder coated)
Pump Head:
®
Valox (PBT) thermoplastic
Pump Head Cover:
Polycarbonate for added strength and chemical resistance.
Permanently lubricated sealed motor shaft support ball bearing.
Cover Screws:
Stainless steel
Roller Assembly:
®
Rotor:
..................................Valox (PBT)
Rollers:
...............................PVDF
Roller Bearings:
.................SS Ball Bearings
Motor Shaft:
Chrome plated steel
TFD System Sensor Pins:
Hastelloy C-276
Power Cord:
3 conductor, SJTW-A water-resistant
Tube Installation Tool:
GF nylon
Mounting Brackets and Hardware:
316 stainless steel
Motor:
Brushed DC, 1/8 H.P.
Duty Cycle:
Continuous
Motor Speed Adjustment Range 100:1:
1.0% - 100% motor speed (1.3 to 130 RPM)
Enclosure:
NEMA 4X (IP66), Polyester powder coated aluminum.
Maximum Overall Dimensions:
7-1/2” W x 10-1/4” H x 14” D (19 W x 26 H x 35.6 D cm)
Product Weight:
28.4 lb. (12.9 Kg)
Approximate Shipping Weight:
35 lb. (15.9 Kg)
Maximum Working Pressure
(Excluding pump tubes)
:
50 psig (3.4 bar)
NOTE
: See the individual pump tube assembly maximum pressure
ratings.
Maximum Suction Lift:
30 ft. of water at sea level (14.7 atm psi)
Ambient Operating Temperature:
O
O
O
O
14 F to 125 F (-10 C to 52 C)
Ambient Storage Temperature:
O
O
O
O
-40 F to 158 F (-40 C to 70 C)
Operating Voltage:
115VAC/50/60Hz, 1ph (1.5 Amp Maximum)
230VAC/50/60Hz, 1ph (0.7 Amp Maximum)
220VAC/50/60Hz, 1ph (1.0 Amp Maximum)
240VAC/50/60Hz, 1ph (1.0 Amp Maximum)
Power Cord Options:
115V50/60Hz = NEMA 5/15 (USA)
230V50/60Hz = NEMA 6/15 (USA)
220V50/60Hz = CEE 7/VII (EU)
240V50/60Hz = AS 3112 (Australia/New Zealand)
Page 4
3.0
Features
>
Peristaltic pump design does not have valves that can clog requiring maintenance.
>
Self priming - even against maximum line pressure. By-pass valves are not required. Cannot vapor lock or
lose prime.
>
Variable speed DC motor.
>
Rated for continuous duty (24X7).
>
Specially engineered tubing for long life at high pressures. Meets FDA 21 CFR requirements for food
contact applications.
>
Patented Tube Failure Detection (TFD) system. Senses tube failure by detecting chemical in pump head.
>
Molded squeeze rollers and molded alignment rollers for optimum squeeze, unparalleled accuracy, and
tube life.
>
Heavy duty rotor - single piece plastic rotor means no flexing and increased accuracy with no metal springs
or hinges to corrode.
>
Inject at maximum pressure in either direction (clockwise and counter clockwise).
>
Compatible with Blue-White’s output Flow Verification Sensor (FVS) system.
Enclosure Rating:
NEMA 4X:
Constructed for either indoor or outdoor use to provide a degree of protection to personnel against
incidental contact with enclosed equipment; to provide a degree of protection against falling dirt,
rain, sleet, snow, windblown dust, splashing water, and hose-directed water; and that will be
undamaged by external formation of ice on enclosure.
IP66:
No ingress of dust; complete protection against contact. Water projected in powerful jets against
enclosure from any direction shall have no harmful effects.
3.1
Agency Listings
Symbol
Explanation
!
WARNING (Risk of electric shock)
CAUTION (Refer to the users’ guide)
GROUND, PROTECTIVE CONDUCTOR TERMINAL
This pump is ETL listed to conforms to the following: UL Standard 1081 as a motor operated water
pump. CSA Standard C22.2 as process control equipment
Page 5
This pump complies to the Machinery Directive 2006/42/EC, Low Voltage Directive 2014/35/EU,
EN 60335-2-41, EMC Directive 2014/30/EU & EN 55014-1, EN 55014-2.
®
FlexFlo
®
FlexFlo
This pump is certified to NSF/ANSI Standard 50 - Equipment for Swimming Pools, Spas, Hot Tubs,
and Other Recreational Water Facilities.