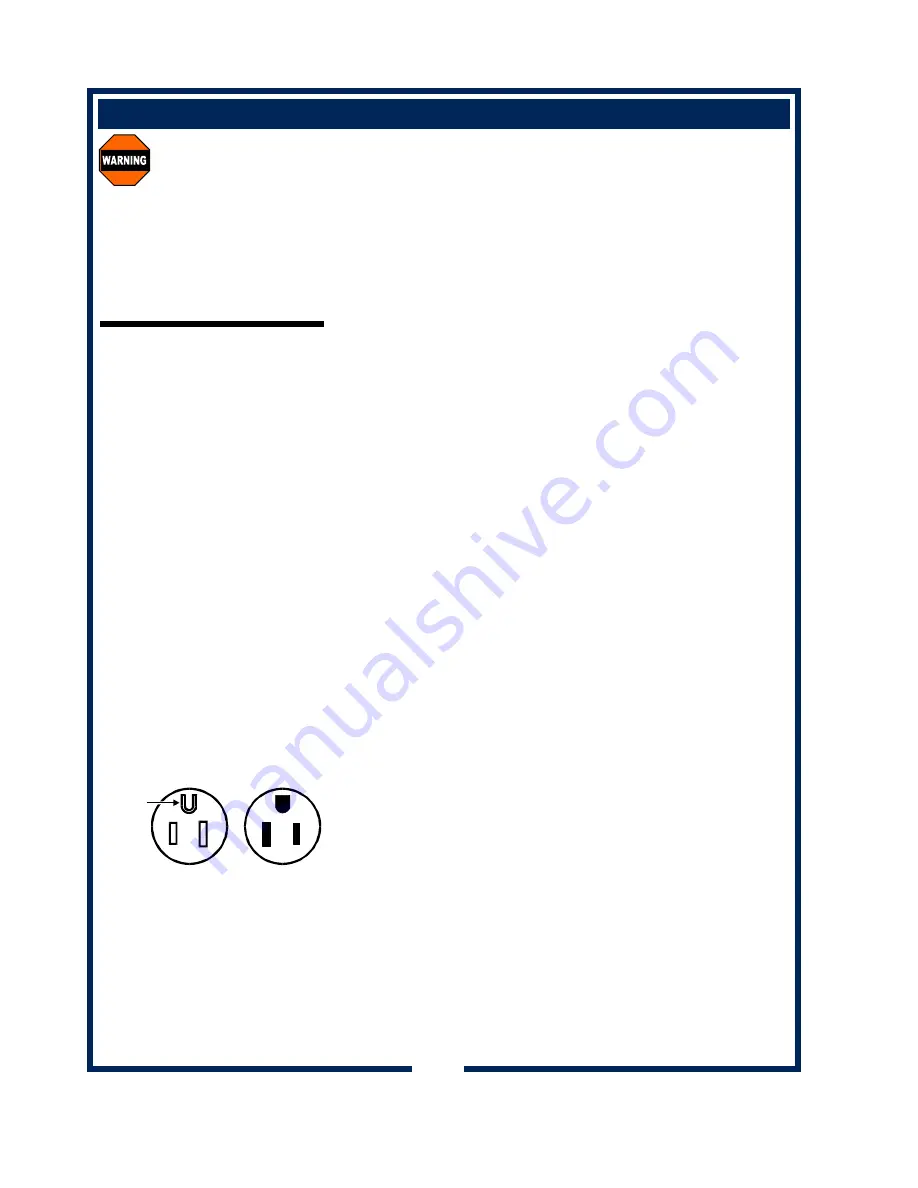
6
WARNING:
SHOCK HAZARD
Brewer must be properly
grounded to prevent possible
shock hazard. DO NOT
assume a plumbing line will
provide such a ground.
Electrical shock will cause death
or serious injury.
IMPORTANT:
Supply power must match
nameplate for voltage and
phase. Connecting to the
wrong voltage will damage the
brewer or result in decreased
performance. Such damage is
not covered by warranty.
IMPORTANT:
Do not connect brewer to
electrical power until you are
ready to fill the tank. See
instructions on page 7.
IMPORTANT:
The ground prong of the plug is
part of a system designed to
protect you from electrical shock
in the event of internal damage.
Never cut off the ground prong
nor twist a blade to fit an
existing receptacle. Contact a
licensed electrician to install the
proper circuit and receptacle.
ELECTRICIAN’S INSTALLATION INSTRUCTIONS
REFER TO ELECTRICAL SPECIFICATIONS - Page 1
Check the nameplate to determine correct electrical service
required for the Brewer to be installed.
IMPORTANT:
Before connecting to electricity, make sure
brewer is connected to the water supply.
This brewer is equipped with a cord and plug. It will require a
115 - 125 volt 20 amp circuit (50/60 Hz, 2 wire plus ground, with
NEMA 5-15R or 5-20R Receptacle).
See Figure 3 below left.
NEMA 5-15R
RECEPTACLE
NEMA 5-15P
PLUG
GROUND
PIN
Fig. 3 Power Supply Plug
INSTALLATION (continued)