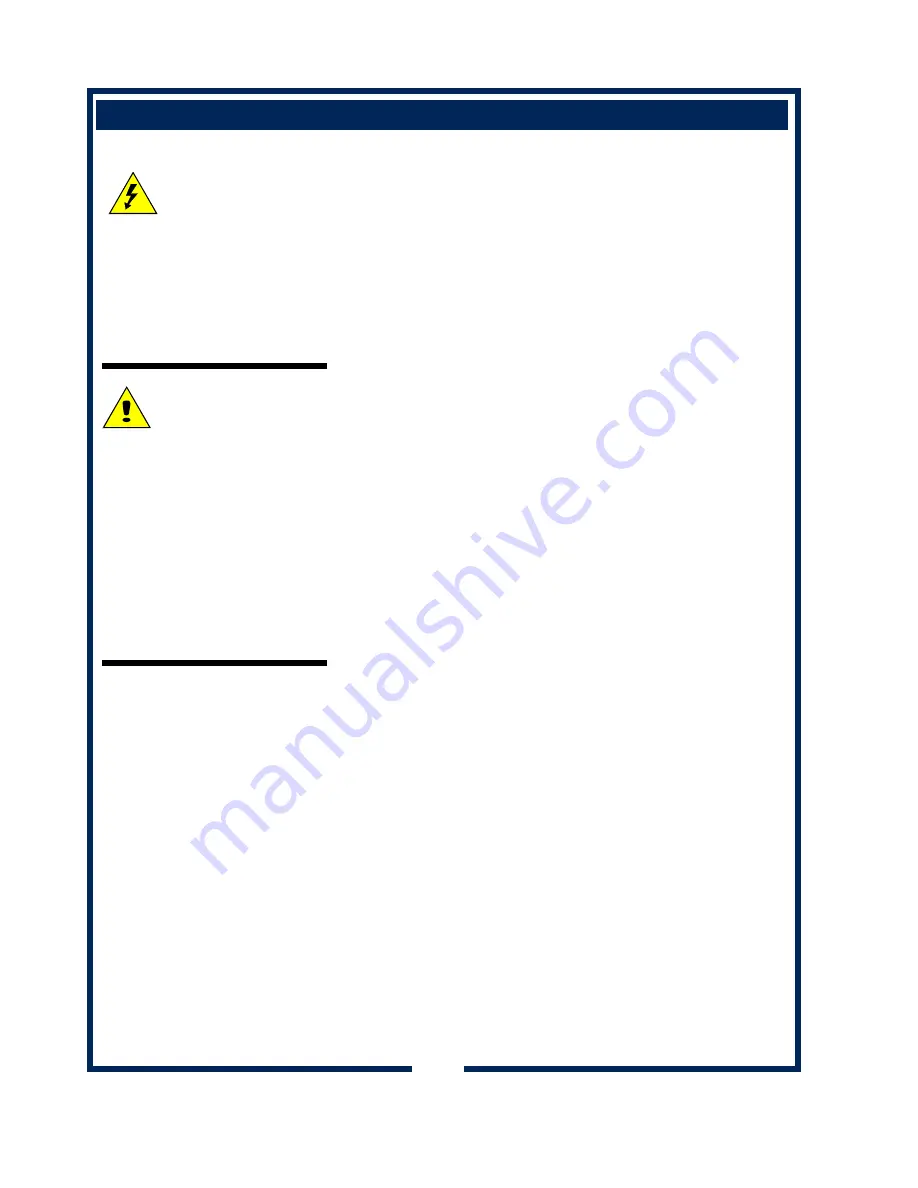
INSTALLATION
4
READ THIS CAREFULLY BEFORE STARTING THE INSTALLATION
Unpack the unit. Inspect all components for completeness and
condition. Ensure that all packing materials have been removed
from the unit.
LEVELING THE UNIT
Verify that an adjustable leg is installed at each corner of the
dispenser.
Set dispenser in its operating location. Level the dispenser. A
spirit level should be placed on the top of the unit, at the edge,
as a guide when making level adjustments.
Level the unit from left to right and front to back by turning the
adjustable feet. Be sure all four feet touch the counter to prevent
tipping.
PLUMBER’S INSTALLATION INSTRUCTIONS
Dispenser should be connected to a
POTABLE WATER, COLD
WATER
line. Flush water line before connecting to dispenser.
DO NOT use a saddle valve with a self-piercing tap for the water
line connection. Such a tap can become restricted by waterline
debris. For systems that must use a saddle tap, shut off the main
water supply and drill a 3/16” (minimum) tap for the saddle
connection, in order to insure an ample water supply. Remember
to flush the line prior to installing the saddle.
The dispenser must be installed on a water line with average
pressure between 20 PSI and 90 PSI. If your water pressure
exceeds 90 PSI at anytime, a pressure regulator must be
installed in the water supply line to limit the pressure to not more
than 90 PSI in order to avoid damage to lines and solenoid.
A water shut-off valve should be installed on the incoming water
line in a convenient location (Use a low restriction type valve,
such as a 1/4-turn ball valve, to avoid loss of water flow thru the
valve.
Model 9460KFT requires a 1/4" female flare fitting to connect to
the water inlet fitting on the bottom of the unit.
CAUTION
EQUIPMENT
ELECTRIC DAMAGE
DO NOT plug in or energize this
appliance until all Installation
Instructions are read and
followed. Damage to the
Brewer will occur if these
instructions are not followed.
CAUTION
UNSTABLE
EQUIPMENT HAZARD
It is very important for safety
and for proper operation that the
appliance is level and stable
when standing in its final
operating position. Provided
adjustable legs must be
installed at each corner of the
unit. Failure to do so will result
in movement of the dispenser
which can cause personal Injury
and/or damage to brewer.
NOTE:
Water supply inlet line
must meet certain minimum
criteria to insure successful
operation of the dispenser.
Bloomfield recommends 1/4"
copper tubing for installation of
less than 12 feet and 3/8" for
more than 12 feet from a 1/2"
water supply line.