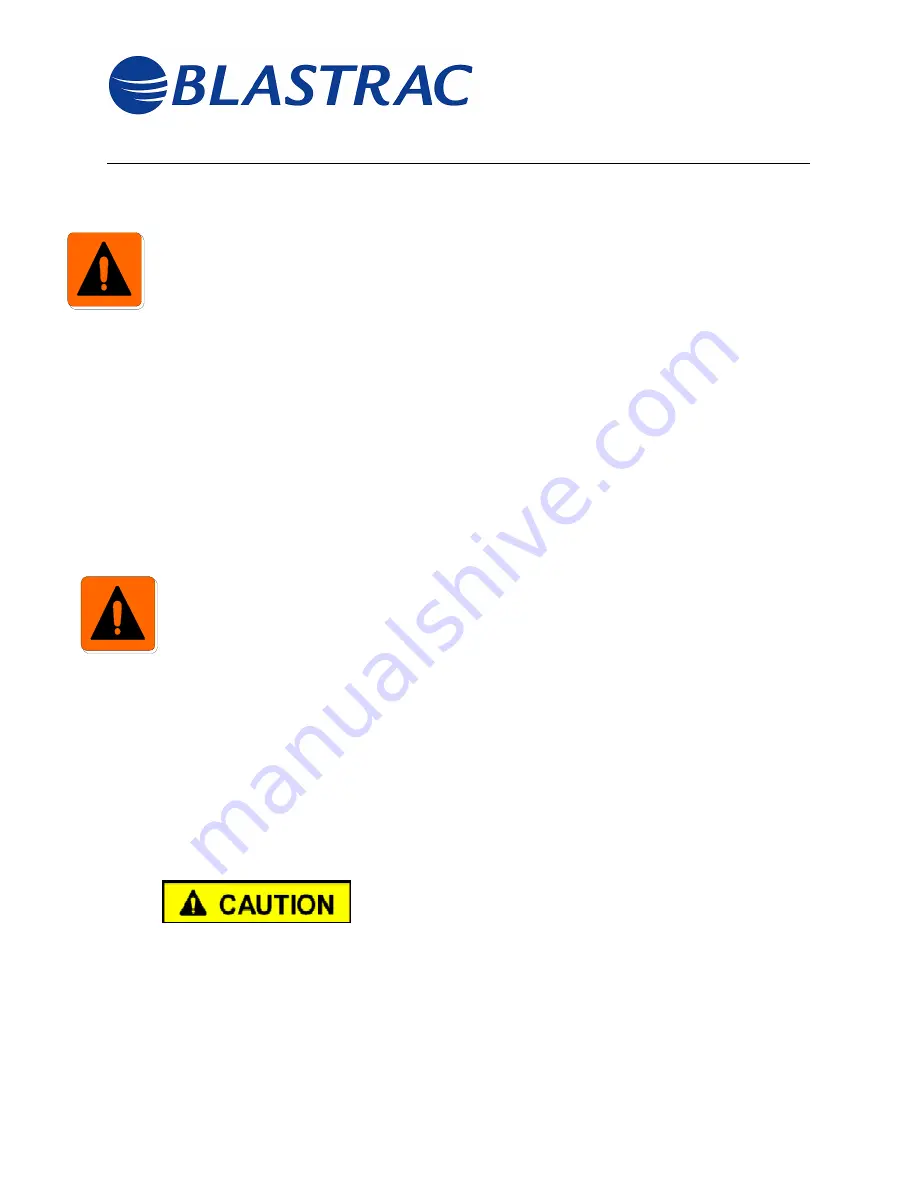
Operating Instructions Manual BMG-2500 MULTI GRINDER
33
JANUARY 2005
© International Surface Preparation Group, Inc.
11.2
Diamond plug tools
11.2.1
When running the machine with diamond plugs the motor turning direction is not a concern. The
diamond plugs are not sensitive to direction.
11.2.2 The plugs are hot from friction build-up! Wear appropriate gloves when handling the
plugs.
See section 10.6. Switch diamond plugs into different locations in the holder arms every 2
to 3 hours. Move left rotating plugs into the right rotating arms and right rotating plugs into left
rotating arms. This will promote even wear on the plugs and helps to clear off any build-up of
removed materials.
11.2.3
When removing adhesives, the diamond plugs will heat the surface of the floor and cause the
adhesive to build-up over the diamonds. Play sand can be used to clear off this build-up. Simply
throw dampened play sand, not dripping wet, on the floor and work the machine over it. Wet sand
is heavier and will not be thrown away from the plugs as they work over it. The end result should
be clean diamond plugs. If sand is not available, run the machine over bare concrete taking care
not to cause excessive removal of the floor.
11.3
Tungsten carbide cutters.
11.3.1
Tungsten carbide cutters come in square and triangle shapes. Each shape has a special tool
holder block that must be used. When attaching the square cutters to the block holders, tighten
the bolts and nuts hand tight. The square cutters must be able to move slightly to lie flat with the
floor.
11.3.2 Friction causes the cutters, nuts, bolts and holder blocks to become hot. Wear appropriate
gloves when handling these components.
After running the cutters over approximately 500
square feet, they will have lost their sharp edge. Loosen the nuts and bolts securing the cutters to
the blocks only enough to allow them to be rotated 90 degrees. This will expose another sharp
edge on the cutters and can be done four (4) times with each new cutter. Retighten the nuts and
bolts hand tight. Triange cutters are only good for (3) turns and will be rotated 120 degrees.
11.3.3
Make sure that the holder blocks are attached to the arms in the proper direction to allow the
tungsten carbide cutters to come in contact with the floor. See figures 14 and 15.
11.3.4
To prevent a build-up of removed material that sticks to the cutters and holder blocks, spray the
surface of these items with a non-stick cooking spray.
11.3.5 Water and dish soap create a slippery work surface. Walking on the floor covered by this
mixture and the resulting residue from removed material must be avoided until mopped
up.
When removing sticky materials like carpet or tile adhesives, sprinkle the surface to be
cleaned with a mixture of water and dish soap. This mixture can be made in the water tank and
can be metered out according to the need. Start by adding small amounts of soap first, for
example ½ cup soap to 1 tank full of water. A thin wet layer should be sufficient. Do not allow
puddles of standing liquid to form. The soap will cause the adhesive to lose its ability to stick to
itself and the cutters.